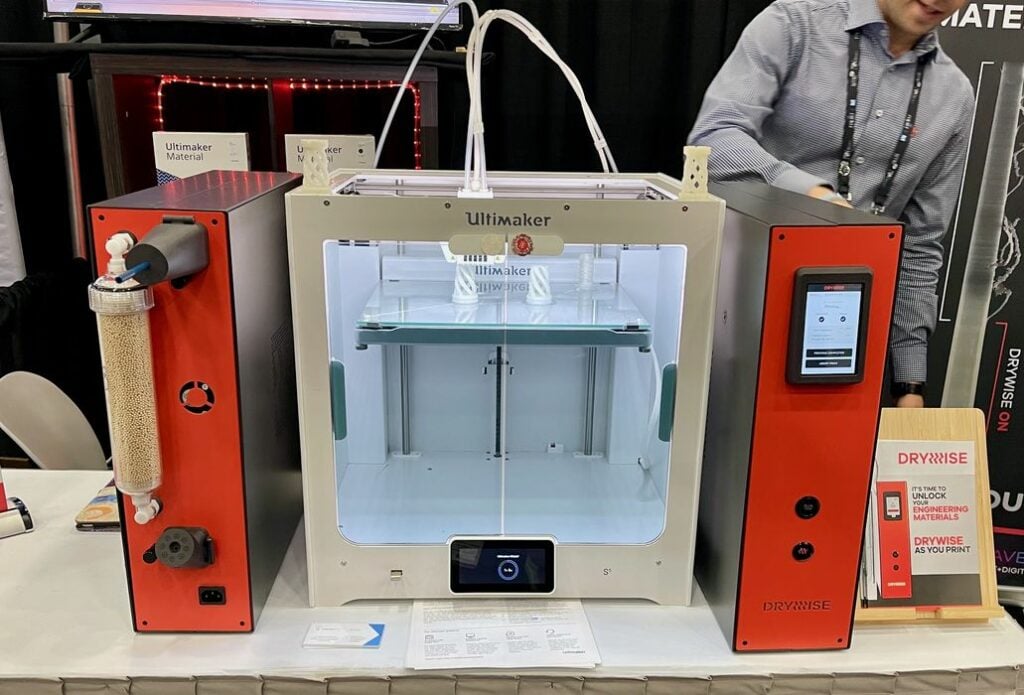
I took a closer in-person look at Thought3D’s new Drywise filament drying solution.
Filament drying is something relatively new to the 3D print scene. While the most commonly used materials, such as PLA, ABS, PETG and even TPU don’t really require serious drying, more recent interest in engineering materials is driving up the necessity of filament drying.
Why dry filament? It turns out that several types of materials are hygroscopic, meaning they tend to soak up moisture from the air and incorporate it into the filament. The amount of absorption depends on the type of material involved, as well as the ambient humidity conditions where it is exposed.
The problem is that the absorbed moisture basically boils during extrusion, as the hot end temperatures are always above 100C. This forms bubbles in the extrusion, which messes with the precisely calculated flow, can weaken parts as there are air gaps instead of solid material, and finally they can greatly disturb the surface quality of a part. You just don’t want bubbles.
Commonly used materials do have some very slight absorption characteristics, but that is usually alleviated by simply storing the spools in sealed bags with a desiccant.
However, some engineering materials are extremely hygroscopic. The most notable of these would be nylons and PVA soluble support material.
Nylon in particular requires special attention because it can absorb enough moisture in a single day to seriously corrupt a 3D print. It must be stored securely and dried before 3D printing.
There are now several types of drying equipment on the market to help with this issue, including Thought3D’s Drywise, which was first announced last December.
Most of the drying solutions keep the entire spool in a sealed chamber where moisture is drawn out over time with heat, vacuum or both. But the Drywise does things quite differently.
Instead of drying the filament as a whole, it instead dries the filament as it is being printed! You could say it’s a “Real Time Drying Solution”.
The filament is drawn through the Drywise where it is exposed to heat sufficient to remove moisture. As you might imagine, this requires precision thermal controls, which are a key part of the Drywise solution. The sensor solution makes the Drywise “smart”. It’s a completely closed system (air-wise) as they make use of O-rings in the design.
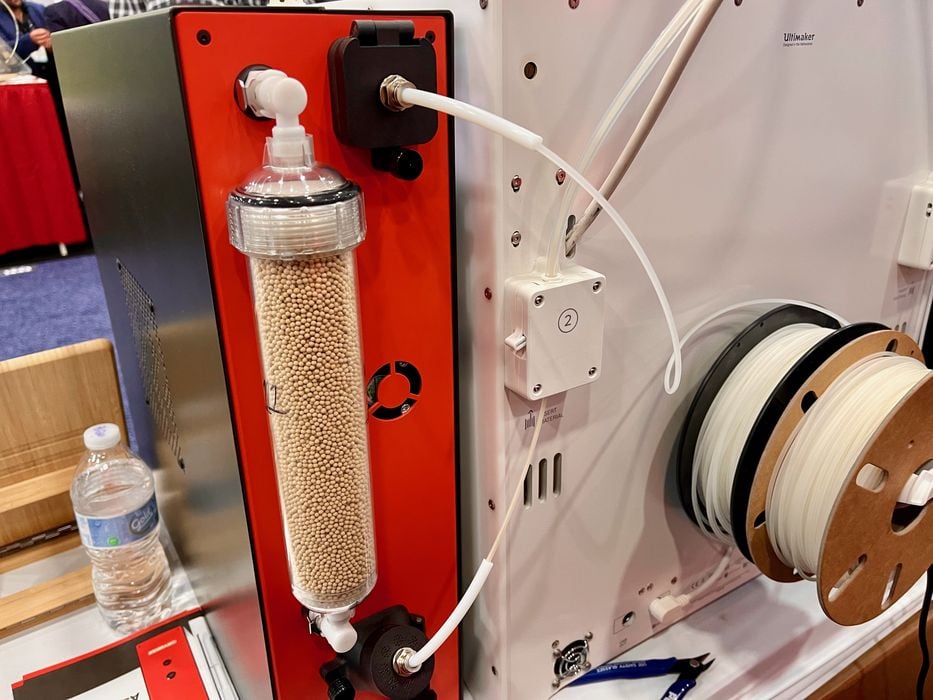
The drying process is assisted by a huge cylinder of desiccant alongside the Drywise. This is replaceable when sufficiently consumed.
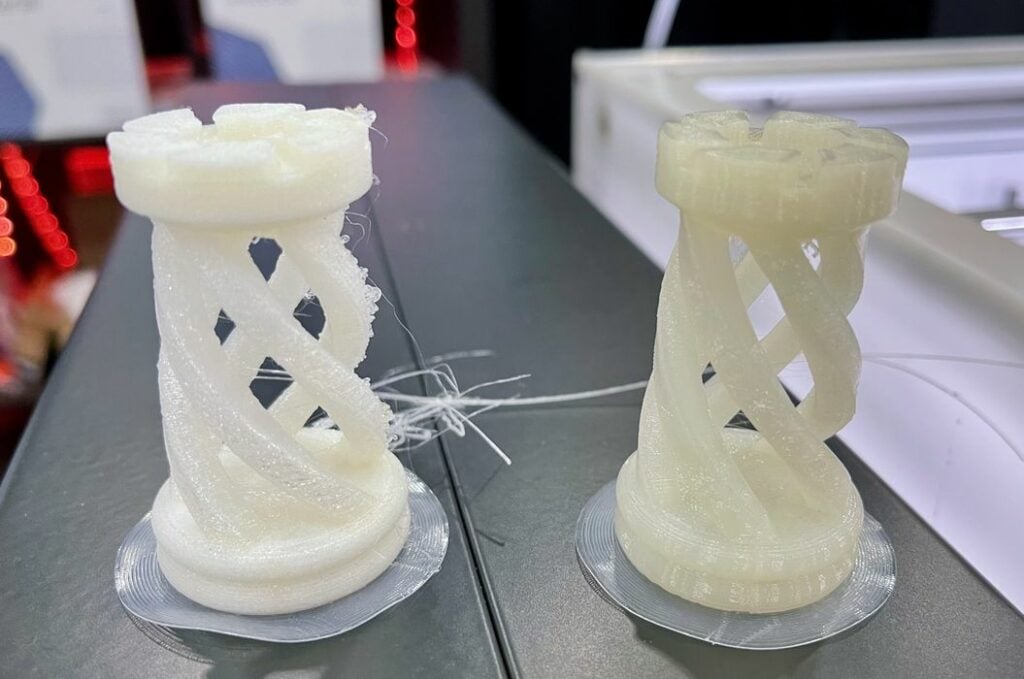
Does it work? See the different here with this nylon 3D print. One side has a dry filament sourced from the Drywise, while the other print used non-dried filament in open air. The surface quality and other print characteristics are much better with the dried filament.
Currently the Drywise is available for 2.85mm filament only, which will certainly make Ultimaker and LulzBot operators happy. However, what about the rest of us using 1.75mm filament?
Thought3D representatives told me they are actively working on developing a 1.75mm solution, which could appear by 2022Q3.
You might wonder why this isn’t out sooner, as shouldn’t be a simple matter to just adjust the Drywise gearing system to accept a smaller diameter?
It turns out there is much more to the story. The original 2.85mm filament is significantly larger than 1.75mm filament, and this means that the 1.75mm Drywise would be able to dry the smaller filament quite a bit faster. This means a complete re-tuning of the system, which is likely why we haven’t seen it yet.
If you need a filament drying solution for your 2.85mm 3D printer, consider looking at the Drywise.
One more thing: Thought3D’s original product was the well-known Magigoo line of adhesive solutions. These wet fluids are applied to print surfaces to provide additional adhesion — or release, depending on the materials and surfaces involved.
I asked why an adhesive company would suddenly begin development of a hardware solution like the Drywise. The answer was that “the future is hardware, not glue”, suggesting that the evolution of 3D print plates will eventually not require the use of separately provided adhesives. Thus began their shift towards alternative products like the Drywise.
It looks like they’ve made a good move with their first hardware product.
Via Magigoo