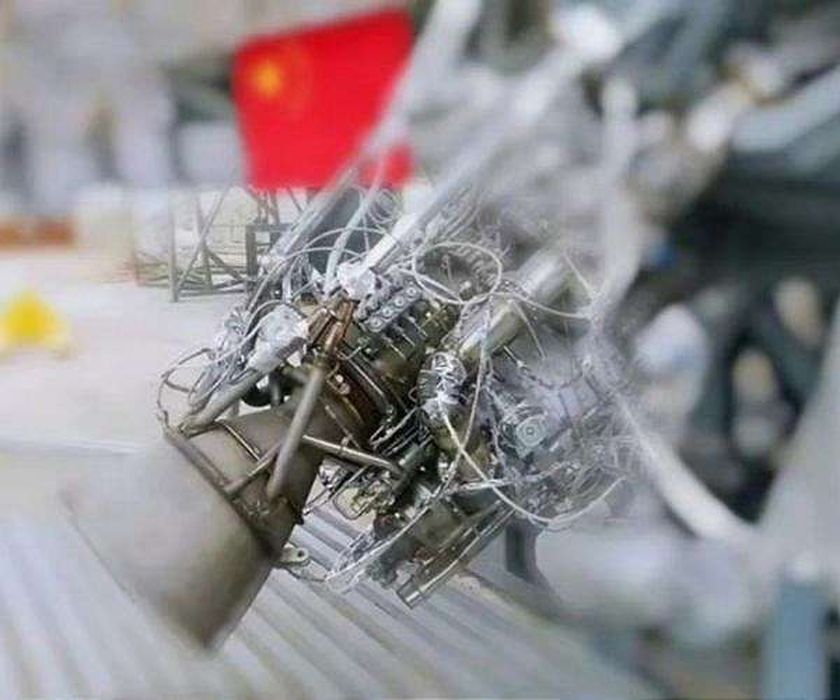
Two key developments in additively manufactured rockets occurred this week, one positive, and the other seemingly negative.
A Breakthrough in 3D Printed Rocket Engines
Let’s start with the good news.
China’s Tianbing Technology, a rocket manufacturer, successfully launched a new vehicle, the Tianlong-2. For us, the important aspect was that this rocket’s engine was entirely 3D printed.
Hold on, haven’t there been 3D printed rockets already produced? Yes, but there’s a big difference here: this is a closed-cycle engine.
A “closed-cycle” rocket engine refers to the method of powering the pumps. In most rocket engines, a small portion of the fuel and/or oxidizer is bled off to run separate motors that drive the pumps that feed the main engine. Those are “open cycle” engines. A closed-cycle engine uses a complex series of channels to burn all of the fuel and oxidizer in the engine while still running the pumps. This style of engine is much more efficient, and that is critically important for rocketry.
It turns out that Tianbing Technology’s TH-11V engine is the world’s first closed-cycle supplementary combustion engine made by additive manufacturing.
Space Daily reports that the company was able to reduce the number of parts in the engine by 80%, and the weight by almost half, all while decreasing the manufacturing cycle by around 75%.
Relativity Space’s Change in Direction
That was the good news. Now for the (possibly) bad news.
We previously reported on Relativity Space’s attempts at launching their entirely 3D printed rocket, Terran-1. The vehicle did launch and easily survived the most challenging portions of the flight, but ultimately failed because their second stage engine did not behave.
Now the company made several announcements. First, they are discontinuing the Terran-1 rocket entirely, even though they have still not made a successful orbital flight. Their sole flight was sufficient to definitively prove the concept of 3D printing a rocket in its entirety, in spite of the subsequent failure.
Secondly, their previously-announced next generation vehicle, the fully reusable and entirely 3D printed Terran-R, is no longer to be completely 3D printed.
They’ve changed the Terran-R design to be somewhat larger, and using more engines to increase the payload weight capacity. This is apparently due to high customer demand. The size of the new Terran-R will be approximately the same as Blue Origin’s flagship (but still in development) New Glenn system, and somewhat larger than SpaceX’s popular Falcon 9 system.
But more importantly, they are no longer 3D printing the entire rocket. The rocket body will now be made from standard aluminum barrel sections, and not 3D printed.
This is quite disappointing, as we all had visions of complex rocket designs emerging from their previous vision.
However, it seems that it could be less expensive to simply use sheet metal than 3D printing, and cash is king in a startup business like Relativity Space. I get the impression they were swamped with orders after their initial launch attempts, and they reorganized the economic model for their system.
I guess this shows that achieving the business goal is the most important objective, and the methods to get there must use the most efficient tools for the job. In some cases, that’s not 3D printing.
Via Space Daily and Ars Technica