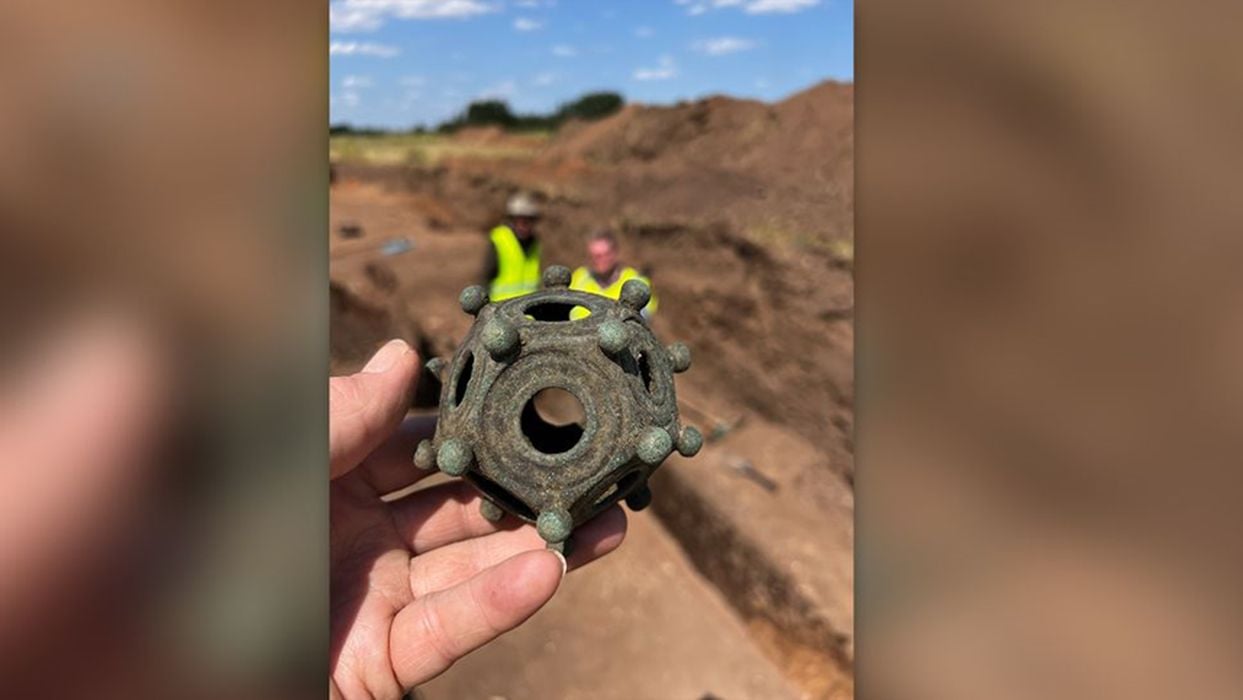
Charles R. Goulding and Preeti Sulibhavi discuss the discovery of Roman dodecahedrons in the UK, their enigmatic purpose and the subsequent surge in interest and replication through 3D printing.
āI came, I saw, I conquered.ā For those of you who remember your high school history and/or literature classes, you will recognize these words as first spoken by Julius Caesar, Emperor of Rome. Caeserās name quite easily conjures up images of immense battles, grand palaces and great drama.
That is why a group of amateur archaeologists in the UK were confused after discovering bronze, Roman dodecahedrons (about 1,700 years old) with various-sized holes in each face (and each hole surrounded by concentric rings imprinted on the metal with studs adjoining where each of the 12 faces connect).
There are some theories as to what they were meant for (i.e., toys, dice, heads of maces, sling stones, astrological instruments, knitting patterns for Roman gloves, or range-finding devices for Roman artillery). With no description of any kind on the dodecahedrons and no mention of such objects in Roman documents and artifacts, their use currently remains a mystery.
3D Printing and Replicas
People are seizing this discovery as an economic opportunity. Replicas are being sold in honor of this archaeological find. This is not uncommon. In fact, it is not surprising either. Dinosaur replicas, toys and paraphernalia are all based on archaeological discoveries and so are many Egyptian commemorative items such as mummies, tombs and pyramids. Why not Roman dodecahedrons?
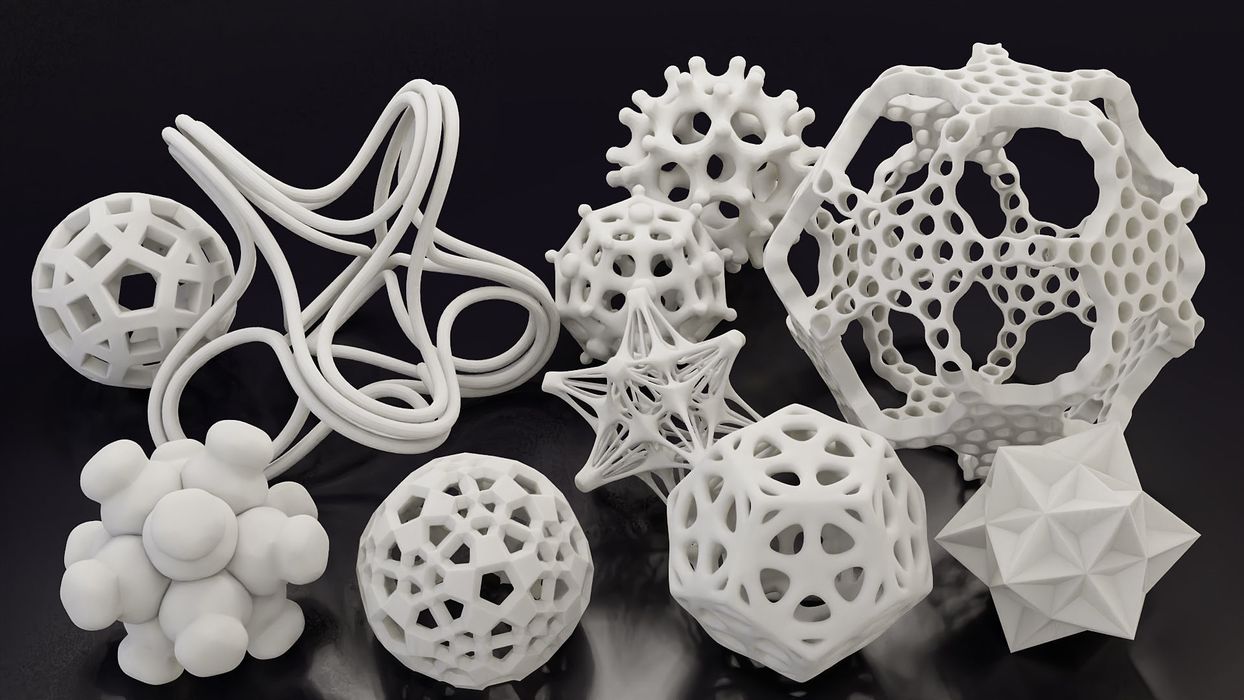
Metal 3D printers are revolutionizing the production of metal parts and products. In particular, there has been significant advancement in recent years (since 2021) regarding the 3D printing of bronze.
One method of 3D printing bronze involves using a powder bed fusion technique. This entails spreading a thin layer of fine bronze powder across the printer bed and then utilizing a high-powered laser or electron beam to selectively melt and fuse the powder in the pattern of the desired 3D object. Layer by layer, the object takes shape until completion. For example, Sculpteo, a major 3D printing service, added bronze infusing to their laser powder bed fusion printers in 2021. This technique can create highly complex and detailed bronze pieces for art, jewelry, hardware, and more.
Another approach is bound metal deposition, offered commercially since 2022. This extrudes bronze wire combined with a binding polymer through a print nozzle. The nozzle precisely places each layer while the polymer binds the bronze material together. The object gets sintered in a furnace to burn off the polymer and fuse the final bronze structure. The advantages are good dimensional accuracy and smooth surfaces. The Bound Metal Deposition Research Group at the University of Toronto is a key pioneer in progressing this method.
A third method uses bronze-infused filaments in material extrusion printers. The bronze powder gets mixed into a polymer filament, which then gets melted and extruded from the print nozzle to form the parts. After printing, the object goes through sintering and infiltration to achieve a high bronze content. The finished products can contain 60-90% bronze with properties rivaling cast bronze. Companies like Desktop Metal and Matterhackers offer bronze filaments ideal for more accessible and affordable 3D printing.
In summary, powder bed fusion, bound metal deposition, and bronze-infused filaments are current, key technologies enabling more widespread and advanced 3D printing of bronze for artistic and functional metal pieces over the last 3 years. The finishes, material properties, detail resolution, and accessibility are improving rapidly.
The Research & Development Tax Credit
The now permanent Research and Development (R&D) Tax Credit is available for companies developing new or improved products, processes and/or software.
3D printing can help boost a companyās R&D Tax Credits. Wages for technical employees creating, testing and revising 3D printed prototypes can be included as a percentage of eligible time spent for the R&D Tax Credit. Similarly, when used as a method of improving a process, time spent integrating 3D printing hardware and software counts as an eligible activity. Lastly, when used for modeling and preproduction, the costs of filaments consumed during the development process may also be recovered.
Whether it is used for creating and testing prototypes or for final production, 3D printing is a great indicator that R&D Credit eligible activities are taking place. Companies implementing this technology at any point should consider taking advantage of R&D Tax Credits.
When in āEnglandāā¦
It appears that the English are taking this discovery to heart as this find appears to be gaining traction on social media there and replicas are being sold. We see this trend as an opportunity for the 3D printing industry to benefit from this discovery and to advance metal 3D printing technology as well. While this find was not in Rome, it reflects the vast history of the Roman empire and its far reach across Europe at one time. For now, the English are doing as the Romans do.