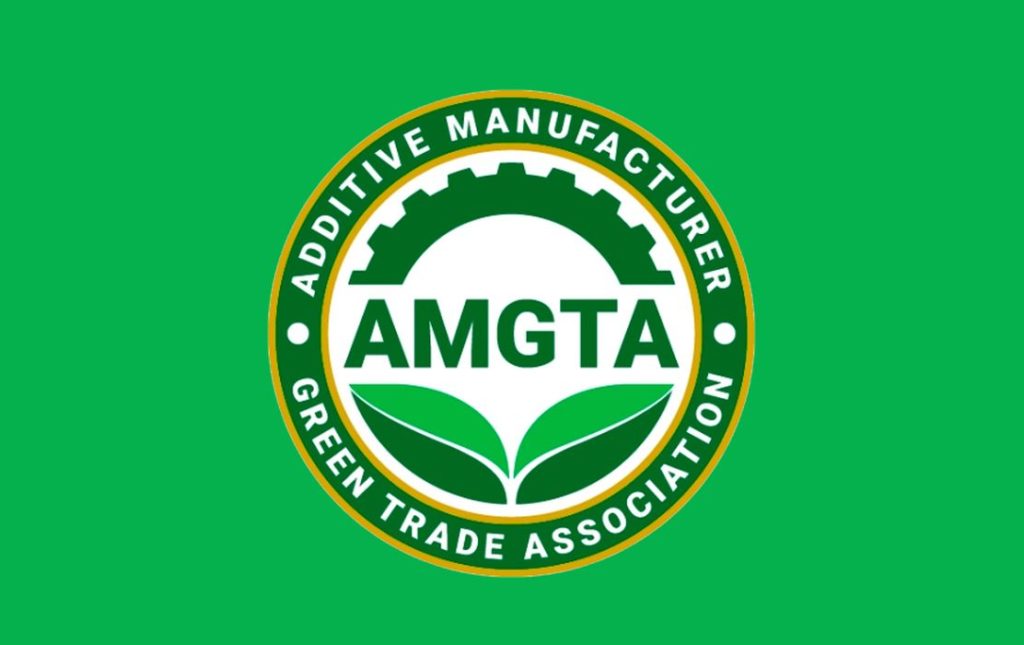
A new study is to determine precisely how sustainable 3D printing processes can be.
Sustainability has become an important factor in almost all activities, and will certainly become much more critical in coming years. It is slowly gaining attention in the additive world, as several companies have taken small steps towards more sustainable solutions.
Some companies produce products using recycled or biodegradable source material. Others offer waste recycling programs. Stratasys even appointed a sustainability officer recently, perhaps the first in the industry.
These are important steps to be clear, but the feeling I have is that we donāt know all the necessary specific details. For example, if you were to hold a 3D printed part in your hand, how do you know it was prepared in a sustainable manner? How much CO2 was generated to get that part made? How much energy was used? What supply chains were tickled in the workflow to achieve that part? How many trucks were used to haul materials and products to and fro?
We may soon know the answers to those questions.
The Additive Manufacturing Green Trade Association (AMGTA) has committed a study to perform a full lifecycle analysis of equivalent 3D printed and traditional aerospace parts using the ISO 14040 lifecycle standard methodology.
The nonprofit organizationās goal is to promote the use of āgreenā approaches to the additive manufacturing industry.
The part in question will be a jet engine low pressure turbine bracket, or āLPTā.
AMGTAās Executive Director Sherry Handel said:
āThis new study will include up to 18 different environmental indicators to quantify the environmental impacts that an optimized jet engine LPT bracket has throughout its entire life cycleāfrom material extraction, manufacturing, transportation, use, and its eventual end-of-life. This data will then be compared to a traditionally designed and manufactured LPT bracket to determine where exactly powder bed fusion AM technology results in lower environmental impacts.ā
The final report will be peer-reviewed and presented next year at the Rapid+TCT conference.
While Iām extremely interested to see the results of this study, there are a couple of thoughts.
Only one specific part is being analyzed here, and the number of possible aerospace parts is practically infinite. Each part may have different geometry, which could result in different results if the same comparison were to be made.
For example, a square flat sheet of metal could presumably be produced very easily with traditional manufacturing, while it would certainly consumer far more resources if one were to 3D print a metal sheet. On the other hand, there are parts with geometries so complex they cannot even be made using conventional approaches.
In other words, the result of the study cannot be literally applied to all parts being made. However, there will be plenty of learnings that, at a high level, will hint at the overall truth.
We will learn many things about energy use, for example, or the general structure of supply chains for both processes.
These learnings are what could be applied to analyze specific situations involving other parts.
In the not-too-distant future it is entirely possible that sustainability measures may be required on products to make sustainability more visible to part buyers and end-use consumers. This study might give us a glimpse into that future world.
Via AMGTA and BusinessWire