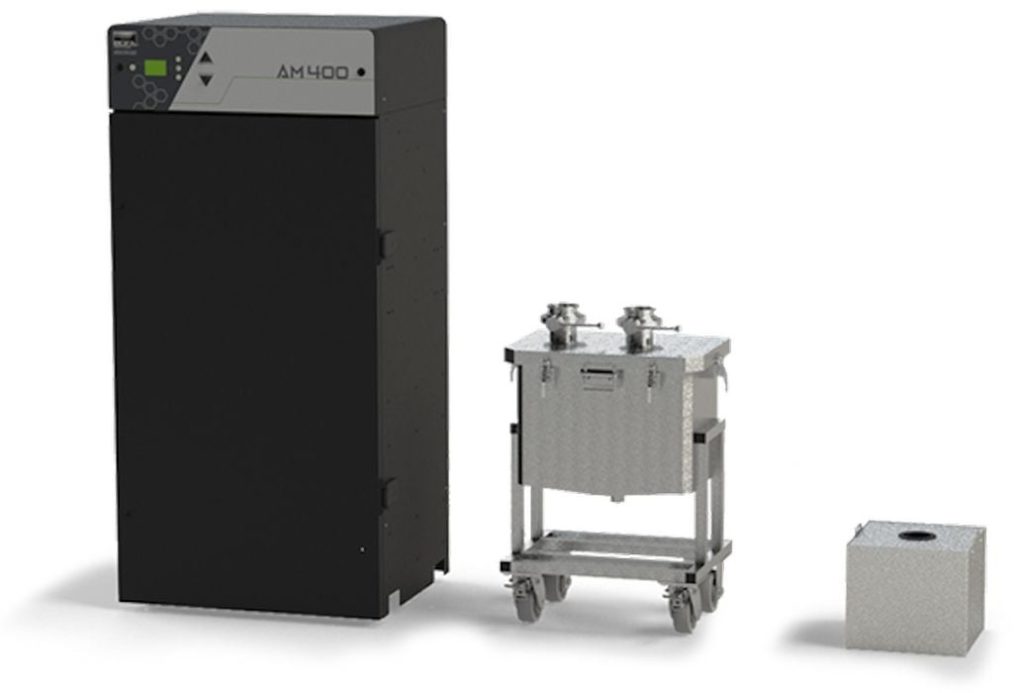
BOFA’s new AM 400 fume extraction device includes a new safety feature designed specifically for additive manufacturing operations.
The AM 400 targets the LPBF market, where there are a number of safety concerns. The primary issue relates to the use of fine metal powder in the 3D printing process. To achieve good part resolution, the metal particles must be extremely small and uniform in diameter.
However, these small particles can be reactive when exposed to oxygen. In some cases they can catch on fire or even explode, particularly if airborne. This is why LPBF 3D printers always have a sealed build chamber filled with inert gas: the oxygen is purged to prevent disasters.
But it doesn’t end with the build chamber: the powder must be secured through its entire lifecycle in the operation. That means it must be sealed during storage, during material loading, during material unloading and so on. It all makes for a very complex — and expensive — process to 3D print metal objects using LPBF. The results, however, are outstanding and usually justify the fuss required to make those parts.
There’s another issue that occurs along a similar line: corrupted filters.
BOFA International is one of the world’s leading producers of fume extraction gear, and their products are often used in 3D printing operations, particularly where external ventilation is not available. Instead, it’s possible to install a standalone fume extractor to clean 3D printer emissions before they are released into the ambient air.
This also occurs in LPBF operations, where filtration devices are attached to 3D printers. However, some of that fine powder will happen to travel through the airflow and end up in the filter.
You guessed it, those filters now have to be treated in the same way as any other point on the powder path.
To change these filters, the filtration unit would have to be disengaged, moved to a safe area and filters changed by a tech with full PPE. That’s a lot of effort to simply change a filter.
BOFA has solved this issue with the new AM 400 unit, which has specially designed filters that are sealable. They explain:
“With BOFA’s AM 400, filters are contained within a separate housing with a robust seal, enabling filter exchange to be completed quickly and safely without isolating the additive manufacturing equipment.”
BOFA suggests users will have workflow savings, and that’s certainly true. If a filtration unit is removed for filter changes, it means the 3D printer associated with it is also down for that time period. An inoperative 3D printer is one that isn’t making any money.
The goal for most LPBF operators is to maximize the utilization of the equipment. That’s because there has been a huge investment to put it on the floor and operate it, though the costs of equipment, materials, staff, facility and more. The machine should be running at maximum utilization to gain back that investment, and shutting it down for a filter change is a costly step.
The new AM 400 should dramatically reduce the time required for filter changes and consequently make more money for the operators.