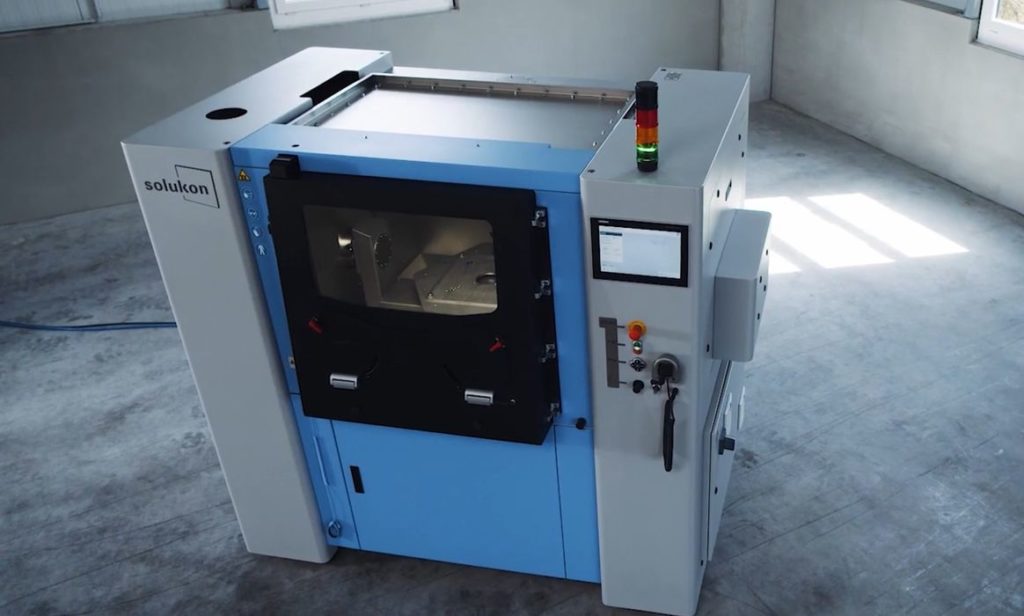
Authentise announced yet another system integration, this time with Solukon equipment.
Authentise is the provider of a cloud-based 3D print management execution service (MES) that is able to track jobs and equipment from start to finish. Without such a capability, 3D printer operators must manually track all activities, and that quickly gets difficult as the number of machines and jobs increases.
But what is Solukon?
Itās a German manufacturer of automated depowdering equipment, specifically for metal 3D printing.
Depowdering is an essential post-processing step in the production of metal parts using AM. You might think this is a straightforward task: just brush off the bits and continue. That might work on parts with simple geometries, but those parts are increasingly rarer these days. Manufacturers now tend to make advanced part designs with complex geometries, and that style inevitably results in lots of nooks and crannies that might hold loose powder.
Removing powder is absolutely critical because it is a requirement for many industrial certifications. Consider the case where youāre 3D printing a metal knee implant. You wouldnāt want to accidentally implant the part into a human body with loose powder that might migrate around the body, would you? Thatās why healthcare certifications require absolutely perfect powder removal.
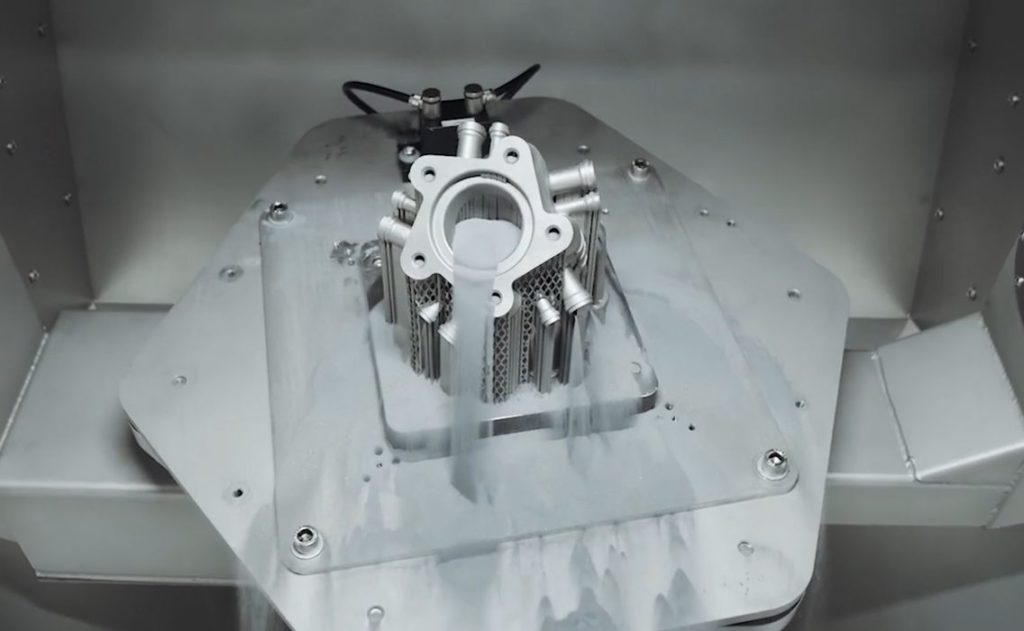
Even more challenging is the ability to do this at scale. That must be done through automation to handle a larger volume of parts. However, how do you guarantee that a machine will remove each and every loose particle for arbitrary part geometries you havenāt even seen yet?
Thatās the puzzle that Solukon seem to have solved.
Solukon manages their equipment through their Solukon Digital Factory, which again is necessary for volume production. This system is comprised of a combination of both software and a series of sensors on the depowdering equipment.
The new arrangement integrates Solukon Digital Factory into Authentiseās aMES (Advanced MES), providing users with even more capability. Authentise explains:
āThe integration of the Solukon powder removal environment will enable users to continue the powder to part genealogy using Authentiseās leading material traceability module. This will increase opportunities for improved post-process inspection recording and recycling of recovered materials. In addition, real-time alerts generated by the Solukon system inside aMES will help the user address any deviations during the process and improve powder recovery. Since aMES already captures data from AM machines and manages the printable geometry, the system passes this information on to Solukon automatically, saving the user from locating and uploading this information separately. The insight generated is appended to the existing aMES part report to ensure end-to-end traceability.ā
CEO and CTO of Solukon Andreas Hartmann said:
“By partnering with Authentise, we are taking the next logical step after the introduction of the Solukon Digital Factory Tool. Seamless data collection and interpretation throughout the entire production and post-process is the only way to achieve a true production line in additive manufacturing. Together with Authentise, we are closing a gap in data transparency and open the way for real Industry 4.0 projects.ā
Itās steps like these that will really drive AM into much larger scale manufacturing operations. Todayās massive manufacturers use integrated systems to manage and make efficient their throughput, and someone showing up with a disconnected 3D printer is simply unwelcome. By showing ways to directly manage the workflow ā which includes 3D printing as well as related processes ā the technology of 3D printing will become that much more valuable.
Via Authentise and Solukon