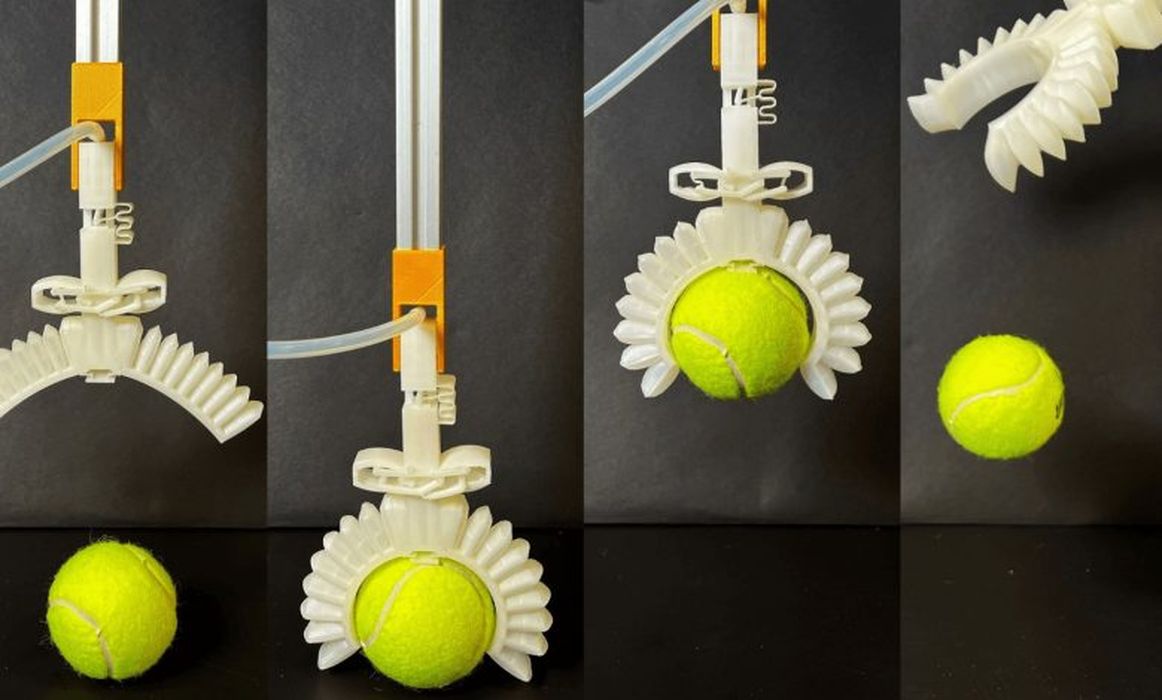
Using a FFF 3D printer embedded with fluidic control circuits, and UltraFuse TPU.
A collaborative effort led by BASF’s California Research Alliance (CARA) and the University of California (UC) San Diego has revolutionized soft robotics. Researchers Yichen Zhai, Albert de Boer, Martin Faber, Rohini Gupta, and Michael T. Tolley have succeeded in fabricating monolithic soft robotic devices on a desktop 3D printer embedded with fluidic control circuits. The project involved using Ultrafuse TPU in Fused Filament Fabrication (FFF) to construct innovative grippers, which brought about enhanced safety due to their material constitution when interacting closely with humans.
Contrasting with conventional soft robots, which rely on pneumatic actuation and fabrication methods involving manual molding and assembly, these new devices embrace 3D printing – reducing the need for manual work and allowing for the creation of more intricate structures.
A common challenge encountered in FFF-printed soft robots is their high effective stiffness and potential leaks, which can constrain their functionality. To address these problems, the researchers came up with an ingenious design to produce soft, leak-proof pneumatic robotic devices, embedding fluidic control components in the actuators during printing. They achieved softer actuators that can bend to form a complete circle, and printed pneumatic valves able to control high-pressure airflow.
The team further combined these actuators and valves to create an electronics-free autonomous gripper. The remarkable aspect of this device is that it was produced in a single, continuous 3D printing workflow, which lasted 16 hours and 19 minutes. The final product required no post-processing, assembly, or repair – ensuring a high degree of repeatability and accessibility.
The same fabrication strategy can be extended to other pneumatic devices with embedded sensing and control circuits. Key design rules include printing using a single continuous toolpath, known as an Eulerian path, and creating structures with ultra-thin walls. This results in low-stiffness structures, comparable to silicone-molded parts.
The produced gripper is ready for immediate use after printing, with the capacity to autonomously pick up and release objects. Its easy replication using a similar desktop 3D printer makes it an attractive tool for various industries such as manufacturing and farming.
Read the rest of this story at VoxelMatters