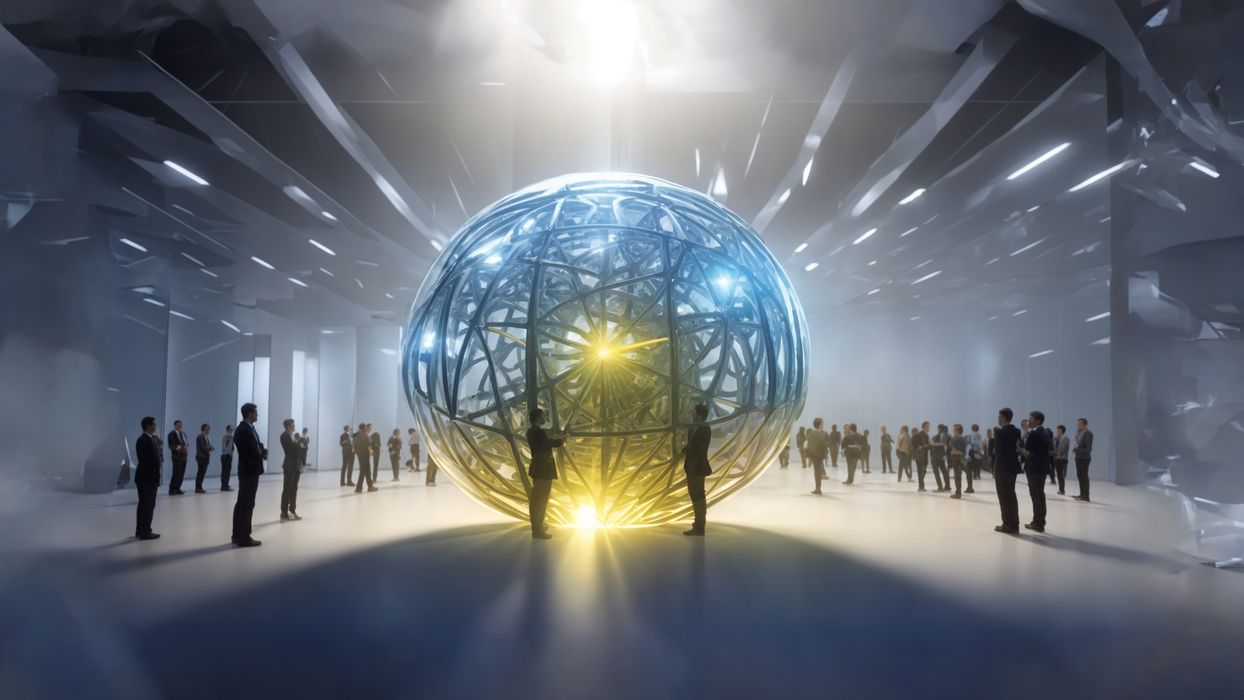
Modern organizations focus on Key Performance Indicators (KPIs) and maximizing an individual’s short-term output.
The apparent objective is to squeeze employees dry. What if, instead of a mentality of extraction it was one of addition? What if an employee was viewed like a renewable energy resource? Viewed renewably, the source is beyond plentiful. Generating more energy at the source (individual contributor) doesn’t create more usable power. Increasing power occurs via the receiving end (leadership and management) through more effective collection, conversion and distribution.
Another apt analogy for an additive management approach is additive manufacturing. 3D printing (additive) “grows” the form up from a blank slate every time. The form possibilities are comparatively limitless. New possibilities, previously blocked by external constraints, open and can allow for boundless creativity and potential. The freer that design decisions are from processes, the more they can flourish organically.
Constraints will always exist to varying degrees. Constraints impose limits, some limits are useful, even necessary, and others are simply disadvantages. Successful creators do the best they can with what they have. They don’t use limits as an excuse and don’t allow limits to deter forward progress. Beautiful works of art can be created with a simple charcoal pencil. But what could the same artist have created with depth of color?
Growth is limited to the confines of its enclosure. In the parlance of 3D printing this is called the build envelope. A container can serve as an incubator until its limits are reached. When maximum expansion has been reached, the container dictates the shape. It has become a mold.
It’s a Goldilocks problem, too little space for growth is constricting but too much allows for Parkinson’s Law, where expansion to fit the allocated space becomes the ultimate goal. The goal, of course, is the goal — and to achieve it as efficiently as possible to allow for the acquisition and preservation of as many resources for the completion of future goals.
Design for manufacturing is a sub goal, one that can become so limiting and consuming that it obfuscates the real goal. The process becomes the driver instead of the outcome. It becomes the end instead of a means to an end.
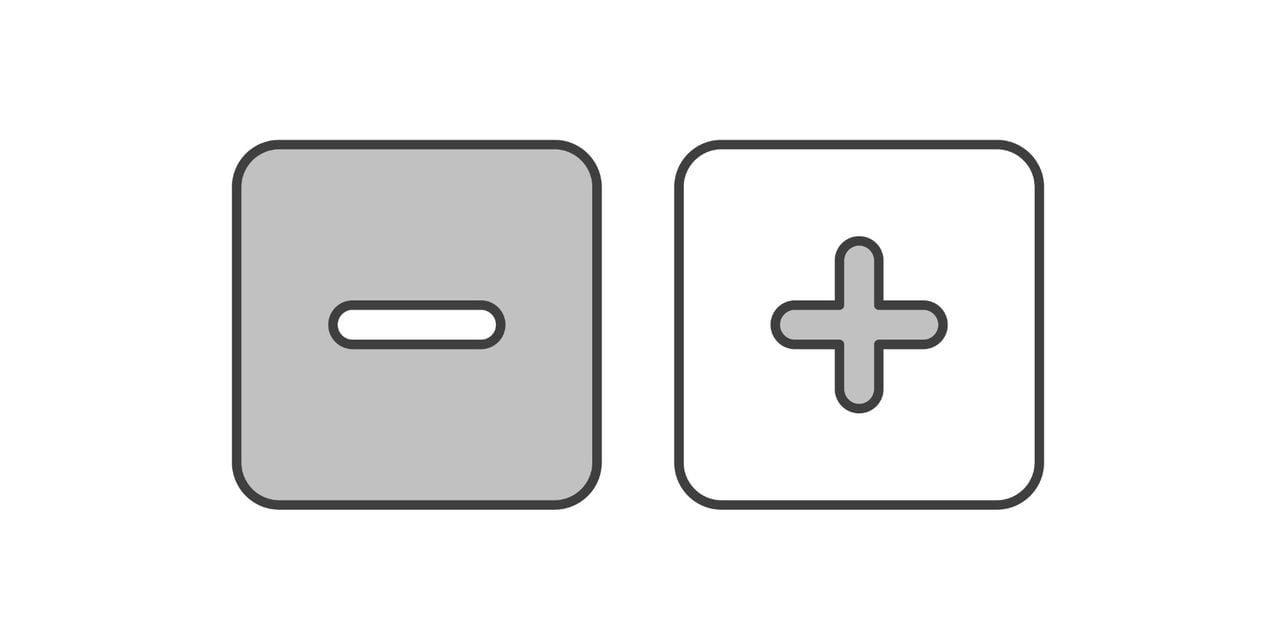
Subtractive manufacturing starts with a uniform shape of stock material and cuts away. Subtractive management also strives to remove the “unwanted” extra to reveal a uniform end product within. A preprogrammed subtraction toolpath is set up to properly run only on an inputted sample of specific dimensions and materials.
People, however, aren’t “stock” or uniformly consistent in any way. A program designed for just one specific scenario is not adaptive and therefore unforgiving to alternate cases. The inflexibility of the mechanics breaks instead of bending. When the program isn’t presented with something that fits within its limited instruction parameters, instead of cutting fluidly, the tool mashes, strains and fails. Instead of carving out a gleaming billet, there’s smoke and scraps and let’s just call them, undesirable results.
Subtractive is prescriptive. The rules of subtraction dictate a decision tree in an algorithmic manner. From a competitive business standpoint, those limiting themselves to the same rules of subtraction will be competing over the same undifferentiated subset market sector. Additive is creative. The freedom of additive unlocks the potential of thinking in novel and nonlinear ways.
People are the heart and soul of an organization. People can only thrive when viewed individualistically and not prescribed with unnatural mechanical “rules.” People must be given the appropriate space to grow without being expected to fill an endless vacuum.
People act like natural materials, with grains and imperfections. In one direction they are strong and flexible and in another they are prone to failure. The craftsmanship of management is to apply healthy and productive strain, while working with the grain.
Additive technologies, subtractive technologies and people all have their imperfections. Additive and subtractive machines produce, at their best, what is expected. People, at their best, produce the unexpected.