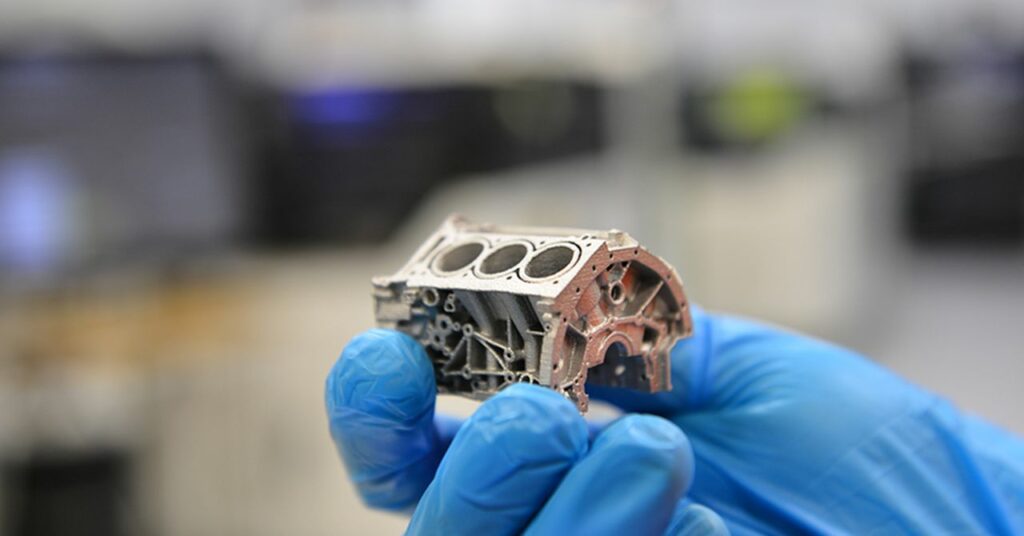
Charles Goulding and Andressa Bonafé look at recent additive applications using aluminum metal.
Offering a unique combination of valuable properties, aluminum is among the most important engineering materials of our time. It is present virtually everywhere, from our homes and cars to packaged foods and mobile phones.
With low density, aluminum is one of the lightest metals in the world (almost three times lighter than iron). It has high thermal conductivity, excellent corrosion resistance, and remarkable flexibility (it is the second most malleable metal). Easily cast, machined, and formed, aluminum is capable of forming alloys with numerous other chemical elements, a characteristic that expands its potential applications. It is also non-magnetic, non-sparking, and non-toxic.
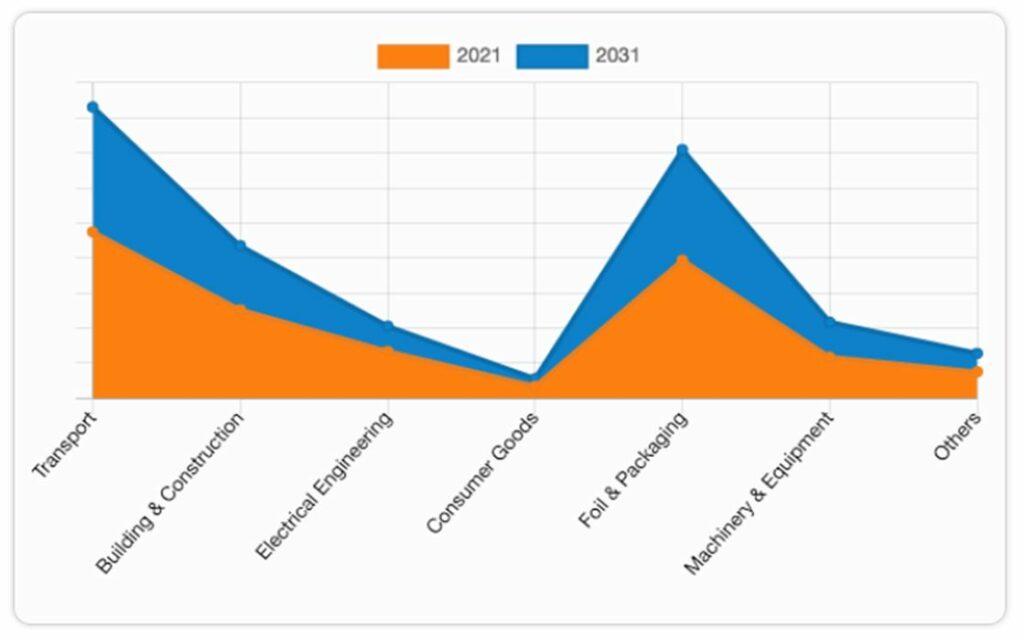
It’s no wonder that aluminum has become indispensable to a wide range of industries, including construction, automotive, aviation, energy, food, etc. Valued at US$148.1B in 2021, the global aluminum market is expected to grow at a CAGR of 5.82% over the next decade, reaching US$258.3B in 2031.
Recent fluctuations
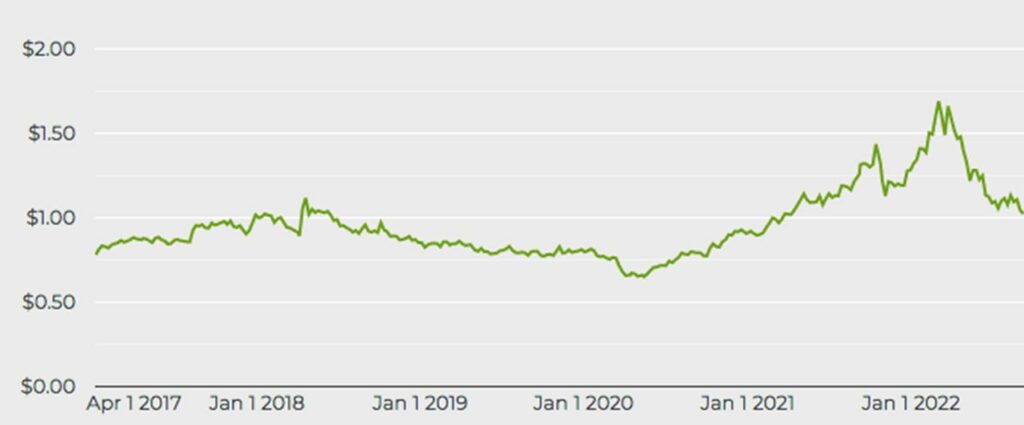
Aluminum prices have experienced considerable fluctuations over the past few months. The metal suffered a devaluation of over 40% after reaching its peak last March. Increasing energy prices have led to significant cutbacks in Europe, where production has reached its lowest point since the 1970s.
However, experts predict that prices should go up in the medium term due to limited smelter capacity additions and improving demand driven by global green investments, such as electric vehicles, solar panels, and renewable energy grids, most of which are aluminum-intensive.
Advancing sustainability
Current instability combined with its role in emerging green technologies underline the importance of rethinking aluminum production practices. Industry leader Alcoa has advanced sustainability, relying on renewable energy to power over 80% of smelting operations. Present in 10 countries, the company offers low-carbon aluminum products through the Sustana product line, which has a carbon footprint approximately 3.5 times better than the industry’s average.
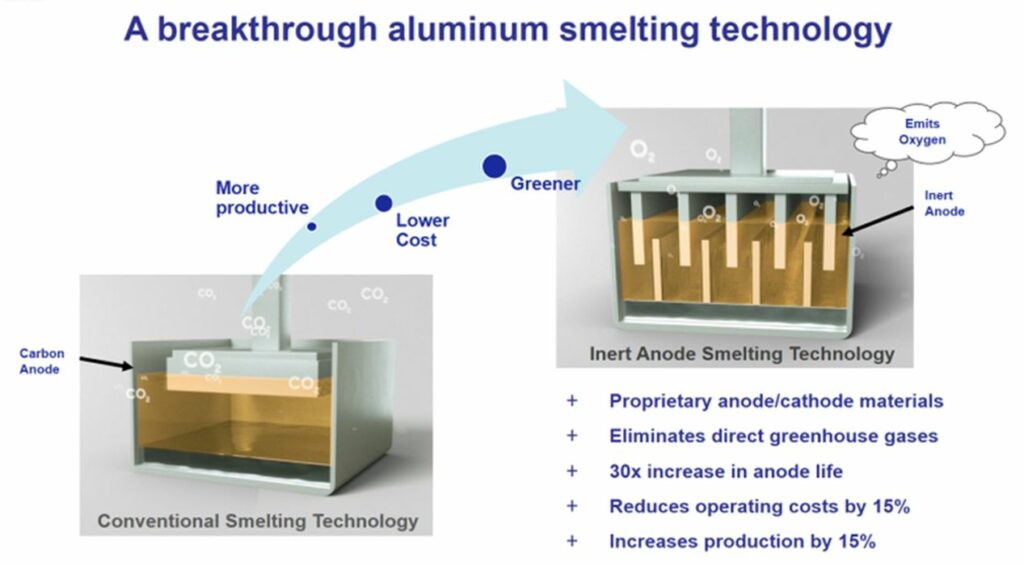
Aiming to reach net-zero greenhouse emissions by 2050, Alcoa invented the ELYSIS™ technology, which replaces the carbon anodes used in traditional aluminum smelting with inert, proprietary materials. The innovative process emits pure oxygen as a byproduct and eliminates all of the greenhouse gas emission.
3D Printing Applications
As prospects for aluminum brighten and more sustainable production alternatives emerge, it is interesting to consider its wide-ranging 3D printing applications. The following paragraphs exemplify how aluminum’s unique properties can be heightened by the design flexibility and cost efficiency of additive manufacturing.
In the aerospace industry, aluminum alloys are often a preferred material, required by engineering due to its corrosion-resistance properties and high-strength capabilities. A lightweight alternative to steel, it is an ideal material for a variety of aircraft components and aerospace applications. Adequacy for use in small, complex components makes aluminum a particularly interesting 3D printing alternative for aerospace.
Boeing is taking advantage of this strategic combination. The American multinational recently established a partnership with AML3D to develop and produce 3D printed aluminum structural test parts using the proprietary Wire Additive Manufacturing (WAM) process. According to AML3D, “these key components will involve extensive printing of high-strength aluminum, an intensive testing program which is comparative to testing of structural components and aligned with the requirements of AS9100D quality assurance for ‘fly’ parts”.
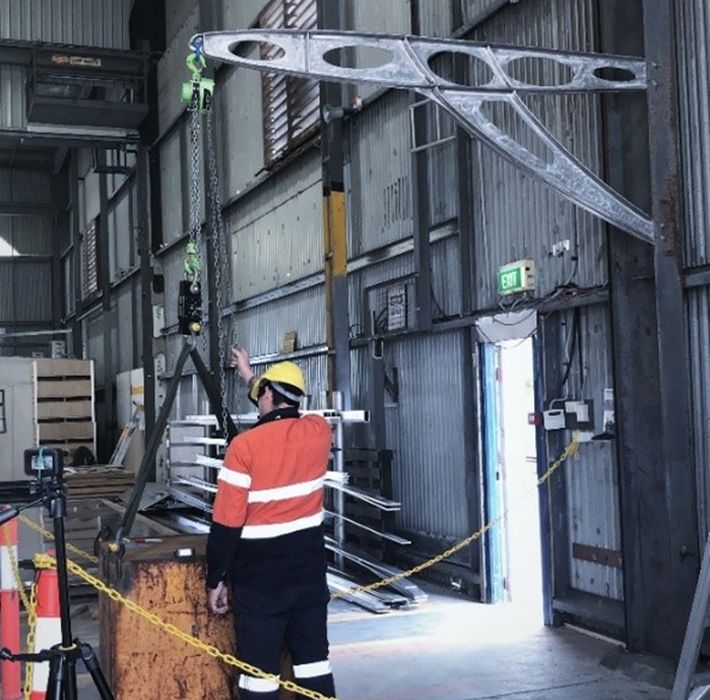
AML3D’s collaboration with Austal further demonstrates the use of aluminum 3D printing in the shipbuilding industry. Following extensive research, production, and testing, Austal Australia received verification for an additively manufactured personnel recovery davit from DNV, an independent expert in risk management and quality assurance. Made from aluminum, the nearly 10-foot structure meets all international and naval specification requirements, showing the potential for a productivity step change in shipbuilding.
The automotive sector has also taken advantage of 3D printed aluminum. In March 2021, ExOne, a leader in binder jet 3D printing technology, and Ford Motor Co unveiled a new patent-pending process for binder jetting aluminum 6061, one of the most commonly used aluminum alloys in the world, which delivers final parts with 99% density and material properties comparable to traditional manufacturing. The companies underline how “sintering precision parts in aluminum can unlock new benefits in manufacturing, such as new lightweight part designs that improve system design and performance”.
Going beyond the examples above, aluminum 3D printing can help advance innovation in many other industries, including packaging, wiring, and renewable energy. Companies involved in additive manufacturing applications should take advantage of the R&D tax credit opportunity described below.
The Research & Development Tax Credit
The now permanent Research and Development (R&D) Tax Credit is available for companies developing new or improved products, processes and/or software.
3D printing can help boost a company’s R&D Tax Credits. Wages for technical employees creating, testing and revising 3D printed prototypes can be included as a percentage of eligible time spent for the R&D Tax Credit. Similarly, when used as a method of improving a process, time spent integrating 3D printing hardware and software counts as an eligible activity. Lastly, when used for modeling and preproduction, the costs of filaments consumed during the development process may also be recovered.
Whether it is used for creating and testing prototypes or for final production, 3D printing is a great indicator that R&D Credit eligible activities are taking place. Companies implementing this technology at any point should consider taking advantage of R&D Tax Credits.
Conclusion
Aluminum’s unique combination of properties paired with the design flexibility and efficiency of 3D printing technology can help advance innovation and productivity in a variety of industries, from aerospace and shipbuilding to packaging and renewable energy.