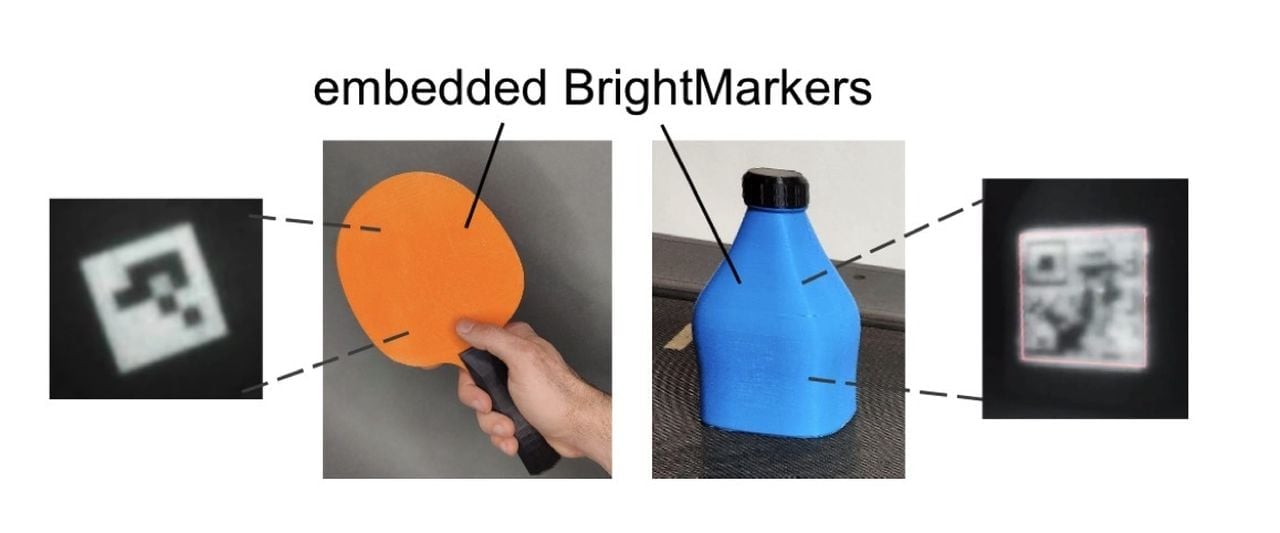
A new technique might make it possible to more easily track 3D printed objects.
Plenty of objects are simply printed and used, but sometimes they require tracking. This could be due to regulatory environments, or perhaps because the part requires an identity during the process it’s used within. For example, variants of a part might be tested, and when one fails, you have to know which one failed.
This has been done by adapting the 3D model to include a visible tracking number or identifying field. Sometimes a QR code could be used. There have also been more sophisticated techniques developed to embed an invisible tracking code in the 3D model that could be traced afterwards.
However, a new method that’s recently been developed by researchers could be quite interesting for this purpose.
The new approach is called “BrightMarker”, and it works with 3D printers.
The concept is to use multimaterial 3D printing to use a secondary filament that reflects light in a different way than the normal filaments.
These special filaments can shift the reflected light frequency to an infrared fluorescent level. In other words, they are quite bright — but invisible to the human eye.
However, these extrusions ARE visible to infrared sensors, which are easy and cheap to obtain.
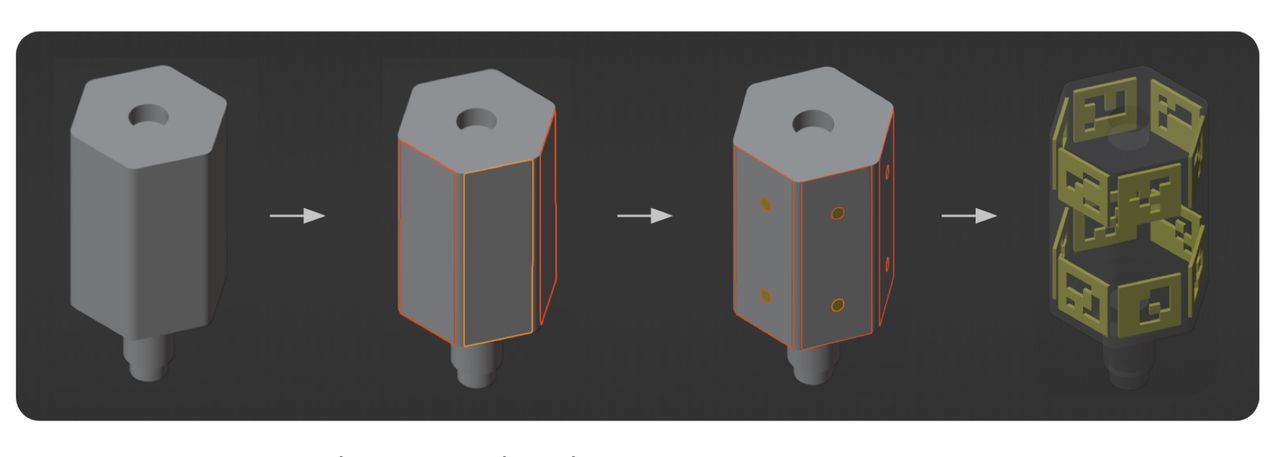
The researchers then developed software that could alter a given 3D model to include geometry for the infrared material. They explain:
“We built a software interface for automatically embedding these markers for the input object geometry, and hardware modules that can be attached to existing mobile devices and AR/VR headsets. Our image processing pipeline robustly localizes the markers in real time from the captured images.”
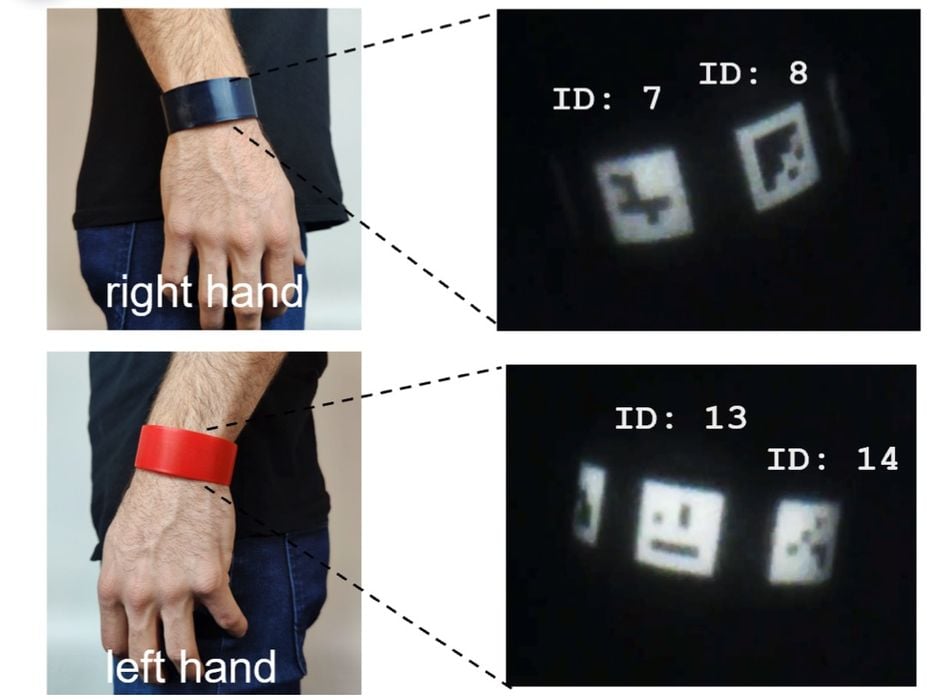
The resulting 3D prints are objects that, when observed through appropriate infrared-sensors, displays the embedded pattern easily. The team also developed software for detecting the patterns, which can be used with a variety of sensor hardware.
But how do these magic filaments work? They explain:
“Fluorescence is the physical phenomenon in which a material absorbs light at one wavelength and emits it at a longer wave- length. This occurs when a molecule absorbs the energy of light and temporarily enters an excited state, before releasing the energy as a lower-energy photon. The difference between these two wavelengths is called Stokes shift. By shifting the illumination from shorter wavelengths to longer ones, the fluorescent color can appear more saturated than it would by reflection alone, which en- hances its detectability. For this reason, fluorescent materials are particularly useful for imaging and sensing applications.”
In practical terms, they added a near-infrared fluorescent dye to standard ABS filament, and proceeded with the experiment. Evidently this approach is independent of the original filament color, making this quite a flexible solution.
Finally, they conclude:
“Our approach offers an easy-to-use solution for marker-based tracking without affecting the object’s look or shape. We showed that BrightMarkers can be embedded in vari- ous object colors, and can be easily localized using a light source and camera filter that match the fluorescence characteristics of the material. Our CAD tool allows users to add markers to their 3D models before printing, and our optical detection hardware can be attached to existing AR/VR headsets for marker tracking. Bright- Marker’s image processing pipeline uses the captured images to robustly localize the markers. Our code and tools can be found on our website5, which we hope will widen the toolkit for the fabrication community.”
I believe this could form a key sub-technology for FFF 3D printers. I could see this as an option easily added to any IDEX or dual extrusion FFF device.
Once that happens we will see plenty of very intriguing new applications leveraging this method of invisible part tagging.
Via MIT (PDF)