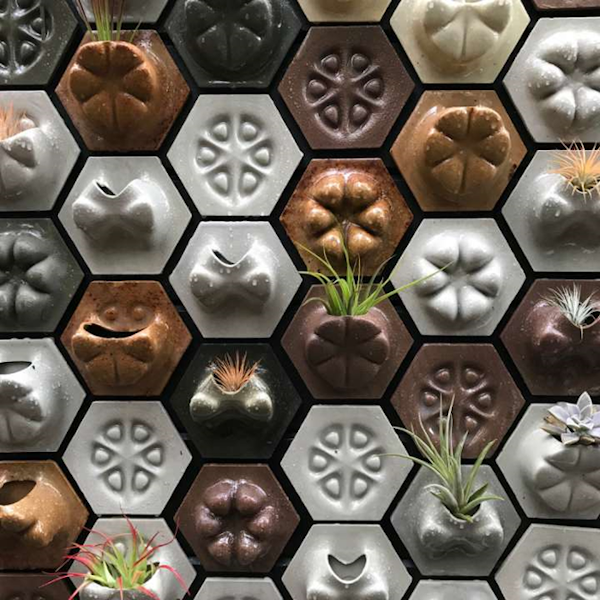
Charles R. Goulding and Joseph Castine consider how advances in 3D printing with wood materials might impact the overall future of forestry.
As the 3D printing revolution continues, so too do the materials with which 3D printers can operate. Desktop Metal is among the manufacturers of 3D printing machines that continue to push the boundaries of what is possible via 3D printing. Recently Desktop Metal partnered with an emerging sustainable 3D printing company, Forust. Forust leverages Desktop Metalâs binder jet technology to print with wood using a modified RAM 336 Desktop machine. Previously there have been attempts to 3D print with wood however, in reality, the parts were only 30-40% comprised of wood fibers. These results also lacked the traditional grain and feel of wooden parts. Utilizing Desktop Metal technology, Forust can produce parts that have the aesthetic and the feel of traditionally manufactured wooden parts.
The thought of leveraging 3D printing techniques with wooden fibers may at first seem to conflict with global green future initiatives. However, this could not be further from the truth. In an article from 2015, the global forest survey estimated there were roughly 3 trillion trees on the planet, with roughly 15 billion being cut down each year, with an estimated 46% decrease in the number of trees since the outset of human civilization.
Forust has leveraged additive manufacturing with their own proprietary wood-based solution that utilizes waste products from wood and paper products. More specifically the proprietary formulation makes use of the primary waste products from woods and papers, those being lignin and cellulose dust (sawdust). This technology works by deposition of binding agents over a powder layer (in this case sawdust and lignin) of material in a repeated fashion until the part is completed. Using this technology Forust is capable of reproducing the grain structure of any number of exotic woods while also being capable of producing grainless wood pieces.
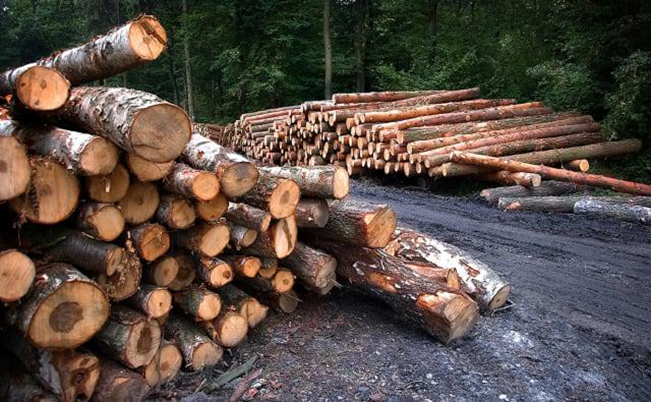
The development of 3D printing processes which use waste products from any industry, especially the wood industry, can prove extremely vital in the move towards circular processes. A circular process aims to eliminate the waste products of various industries by eliminating waste through the continual use of resources by utilizing reuse, sharing, remanufacturing, and recycling to name a few. Several companies in various industries are setting their sights on circular economies to cut out the waste products of their industrial practices.
Circular economies could prove to be extremely fruitful, especially for the wood industry in the wake of the COVID-19 pandemic and the ongoing trade wars. Throughout 2020 the forestry sector saw losses estimated at $1.1 billion of which a majority can be attributed to landowners, logging companies, and sawmills. Typically the wood industry works by the U.S. selling raw timber to China where furniture and other wood parts are fabricated for sale in the global economy, a large portion of which will end up back in the United States. This trade between the U.S. and China has been hampered in recent years, raising the question of why doesnât the U.S. make its own furniture and flooring. The answer to that question is somewhat complicated as it is a combination of both wages and a growing reluctance for U.S. workers to return to work post-COVID-19.
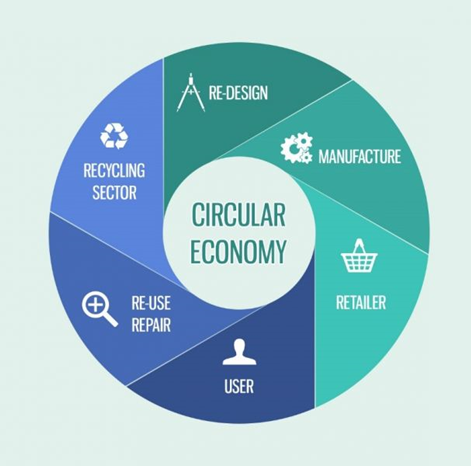
Companies investing and conducting research into furthering their 3D printing capabilities or furthering the 3D printing industry may qualify for an R&D Tax Credit.
The Research & Development Tax Credit
Whether itâs used for creating and testing prototypes or for final production, 3D printing is a great indicator that R&D Credit eligible activities are taking place. Companies implementing this technology at any point should consider taking advantage of R&D Tax Credits.
Enacted in 1981, the now permanent Federal Research and Development (R&D) Tax Credit allows a credit that typically ranges from 4%-7% of eligible spending for new and improved products and processes. Qualified research must meet the following four criteria:
- Must be technological in nature
- Must be a component of the taxpayerâs business
- Must represent R&D in the experimental sense and generally includes all such costs related to the development or improvement of a product or process
- Must eliminate uncertainty through a process of experimentation that considers one or more alternatives
Eligible costs include US employee wages, cost of supplies consumed in the R&D process, cost of pre-production testing, US contract research expenses, and certain costs associated with developing a patent.
On December 18, 2015, President Obama signed the PATH Act, making the R&D Tax Credit permanent. Beginning in 2016, the R&D credit can be used to offset Alternative Minimum tax for companies with revenue below $50MM and, startup businesses can obtain up to $250,000 per year in payroll tax cash rebates.
Conclusion
Continued development into this field by Forust may propel the company into the mainstream and bring the furniture and wood products industry into the 21st century.