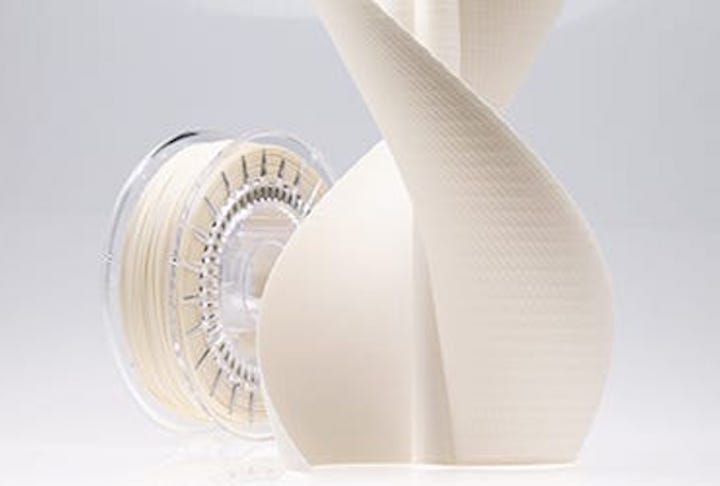
colorFabb has introduced a new ASA material that is extremely lightweight.
ASA is a 3D print material that’s been growing in popularity over the past few years. It offers properties very similar to ABS, the original FFF filament material, but has a significant advantage: it is impervious to UV light exposure, meaning it can be used for outdoor applications.
However, like ABS, ASA also has a strong tendency to warp and as such it can be challenging to 3D print unless a series of precautions are taken. Usually, a heated chamber is required to reliably 3D print larger items ABS and ASA.
colorFabb’s ASA comes in two styles: standard ASA, and their very special LW-ASA. The “LW” stands for “lightweight”, and they’re not kidding: this material is up to 2.5X less weight than standard ASA.
How can they do this, if it’s still chemically ASA? The trick is that they are using a special additive that colorFabb calls, “Active Foaming”.
We covered another material with this additive, LW-PLA, in 2019 when first introduced. Then in 2020 the company delivered a flexible foamy filament, Varioshore.
Now there’s a third entry in the Active Foaming line, LW-ASA.
The foaming process is truly ingenious: the additive in the filament essentially “boils” during extrusion, introducing bubbles in the extrusion line. The bubbles don’t weigh much, and that’s where the weight savings come from.
colorFabb explains how this property can be used:
“LW-ASA is the first ASA filament to use active foaming technology to achieve lightweight, low density ASA parts. At around 240C this material will start foaming, increasing its volume by nearly 2,5 times.
Users can decrease material flow by 40% to achieve lightweight parts, or use the expanding properties to effectively reduce print time by using big layer heights or single extra thick perimeters.”
That last point is quite interesting: you can literally speed up your print jobs because the extrusion line expands as you push it out of the hot end. That’s quite different from normal FFF 3D printing.
Apparently the degree of expansion is somewhat controllable through the extrusion temperature. Thus it’s important to determine the appropriate temperature and flow rate for a given print job. colorFabb suggests a four-step process to figure out the maximum possible foaming level:
- Print cubes at a set speed in temperatures varying from 230°C up to 260°C
- Measure perimeter thickness of each cube, note temperature with highest expansion.
- Print cubes with decreasing steps of flow, using temperature found in step 2.
- Find the cube at which perimeter thickness equals nozzle size.
Once you know these factors, you can play with them on 3D prints to vary the density by controlling the level of foaming. You could, for example, 3D print one part at a specific density, and another part at a lower density by raising the extrusion temperature. It is even possible to vary the density within a part by playing with these factors over subsections of the 3D print.
The combination of UV-resistance and lightweight suggests that drone makers might take advantage of this material to produce strong, lightweight parts that can survive outdoors.
colorFabb sells LW-ASA in either black or white (which they curiously call “Naturel”) on 650g spools at a price of €45 (US$55).
Via colorFabb