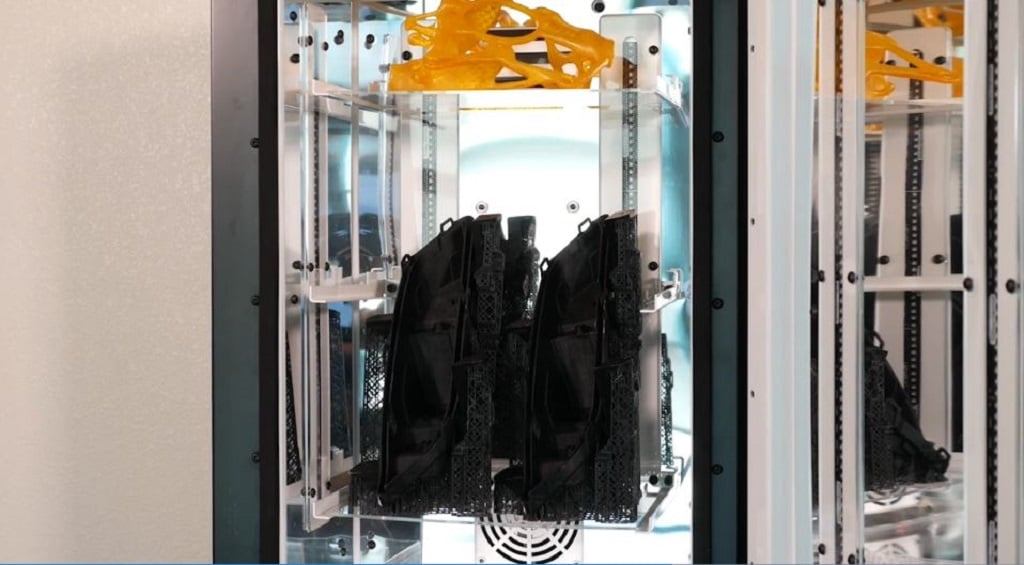
Nexa3D recently launched an intelligent post-processing system that will greatly help businesses improve their efficiency in both the design and supply chain stages.
Nexa3D
Nexa3D is one company that we’ve heard loads about before, from the acquisition of NXT factory to exciting announcements and future plans.
The company makes “ultrafast industrial grade polymer 3D printers affordable for professionals and businesses of all sizes”. Their NXE 400 3D printers are powered by Lubricant Sublayer Photo-curing (LSPC) and Quantum Laser Sintering (QLSS) technologies which aim to increase print speed and hence productivity. Finally, their end-to-end validated workflows aim to reduce 3D printing cycles from hours to minutes, while simultaneously reducing waste, energy consumption, and their overall carbon footprint. The goal is to enable customers to “strengthen their design agility and supply chain resiliency by compressing their design and manufacturing cycle, effectively reducing the time required to produce functional prototypes and production parts from hours to minutes”.
xCure
In October, Nexa3D announced the commercial availability of their new intelligent post-processing curing system, called xCure.
The system cures all of its photoplastic-based parts and is designed to “rapidly unlock the full potential of 3D printed parts at production scale ensuring the delivery of desired mechanical properties, part to part and printer to printer”. xCure is described by Nexa3D as “simple and intuitive to operate with its single click, rotate, and push operation”, which is yet another attribute that makes it valuable to any size business.
This precise curing system designed specifically for the NXE 400 3D printer allows for the implementation of a consistent production workflow to finish prints from the NXE 400 while maintaining “dimensional accuracy, robust structural integrity and stronger molecular structures”. Its large chamber size easily accommodates parts with a volume of as large as 16 litres alongside three build plates, enabling parts to be cured individually. In addition to these capabilities, the xCure also features dual 365 + 405 nanometer wavelength LEDs and optional thermal curing, delivering the full spectrum of Nexa3D’s resin curing coverage with “validated resin specific pre-sets that ensure consistent part curing results print after print”. Uniformity and functionality of this system is optimized with “360 degrees of light and thermal coverage with a reflective interior”.
Avi Reichental, Co-Founder and CEO of Nexa3D, explains:
“Our work with key manufacturing companies and leading material suppliers reveals that only through the rigorous development, simulation and testing of predictive and prescriptive end-to-end workflows can we unlock the full range and consistency of mechanical performance.”
Applications
The xCure system enables 3D printed parts to maximize the properties of their materials and simultaneously increases the accessibility of the entire process. I think that there are a couple major advantages offered uniquely by this system. Its user-friendly menus and proprietary software provide the user with more control over things like structural and molecular integrity, while not sacrificing the quality in terms of factors such as dimensional accuracy. Its large accommodating capacity allows for individual and simultaneous curing of parts based on specific properties and needs. Users can also choose the best curing mode for their purpose between UV only, heat-only, and UV + heat modes to enhance the properties of their chosen materials and maintain part performance.
Overall, my favorite part of this new system is the accessibility and power it offers the user, allowing them to make decisions based on their individual needs.
Via Nexa3D