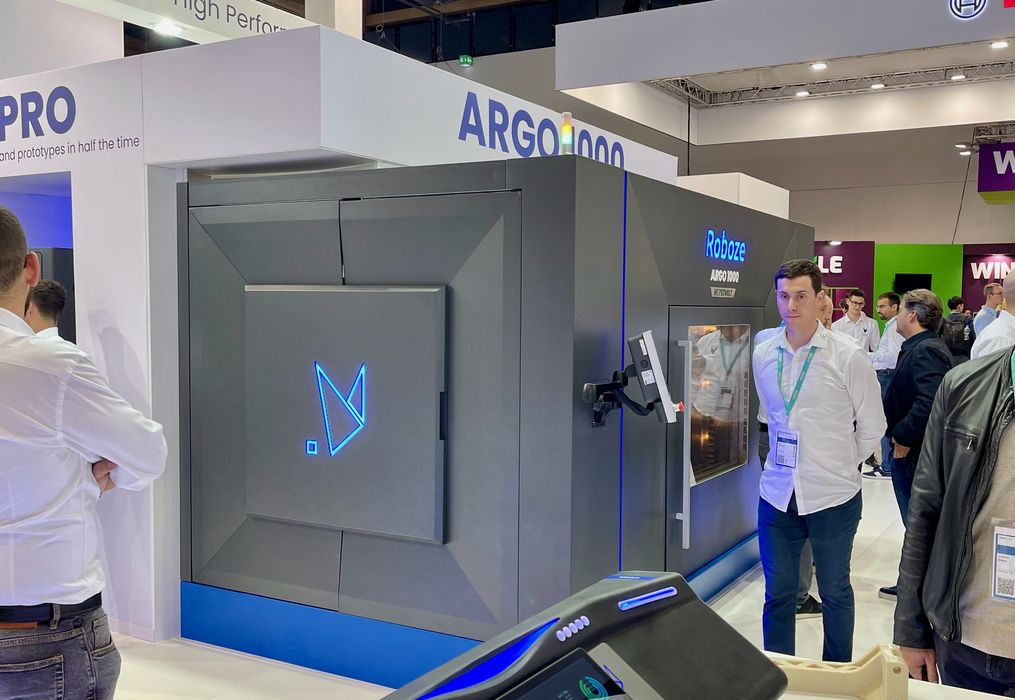
Roboze’s Hypermelt technology should open many doors for the Italian company.
Roboze has been producing high temperature 3D printers for quite a few years now, with gradually increasing build volumes. I recall some years ago seeing their first machines, which were slightly bigger than a typical desktop device.
As you can see in the image at top, things have changed significantly. They’re focusing on larger format 3D printing, something several companies have chosen as their strategy.
However, “printing big” isn’t the same as normal-sized 3D printing. The issue is time: larger prints take proportionately more time to complete, and prints made at the largest build volumes might take literally days to complete.
Roboze recognized this and developed something they call “Hypermelt”. It’s a new extrusion approach that seems quite suitable for large format printing.
The key to Hypermelt is that it uses pellets instead of standard filaments. Filaments are quite expensive compared to pellet material, simply because filaments are made from pellets. By using pellets the cost of materials is substantially less expensive. Roboze estimates cost savings at around 60% less when using Hypermelt.
However, there’s another advantage: speed. The Hypermelt technology involves both rapid motion and advanced nozzles (ranging from 0.8mm to 3.0mm), leading to dramatic print speedups.
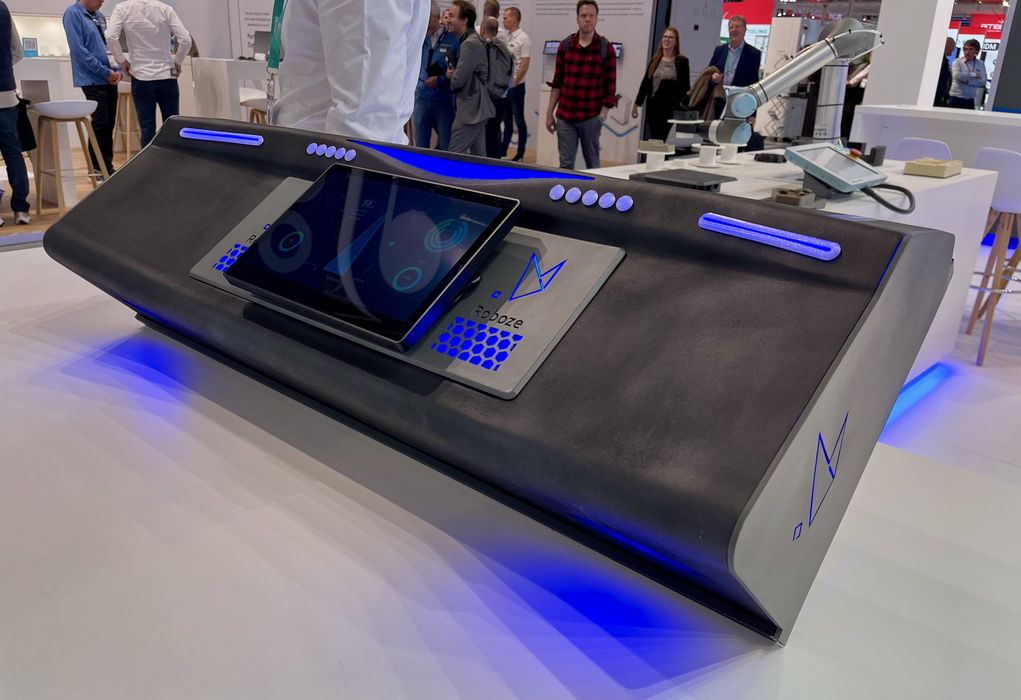
We were told that Hypermelt can deliver up to 2kg of polymer material per hour, which is quite significant. Imagine printing your standard roll of filament in only 30 minutes, and you’ll get an idea of how fast Hypermelt can be.
As for those materials, Roboze told us they offer a wide range of high performance materials for the Hypermelt system in pellet form, including PEKK, ULTEM and more.
One of their newest materials is a new PA-Carbon fiber formulation that will include a 40% ratio of chopped carbon fibers. That should make for some very strong parts.
Hypermelt can handle these extreme materials mostly due to its actively heated build chamber, which can be as hot as 180C. However, for most prints it needs to run at “only” 95C.
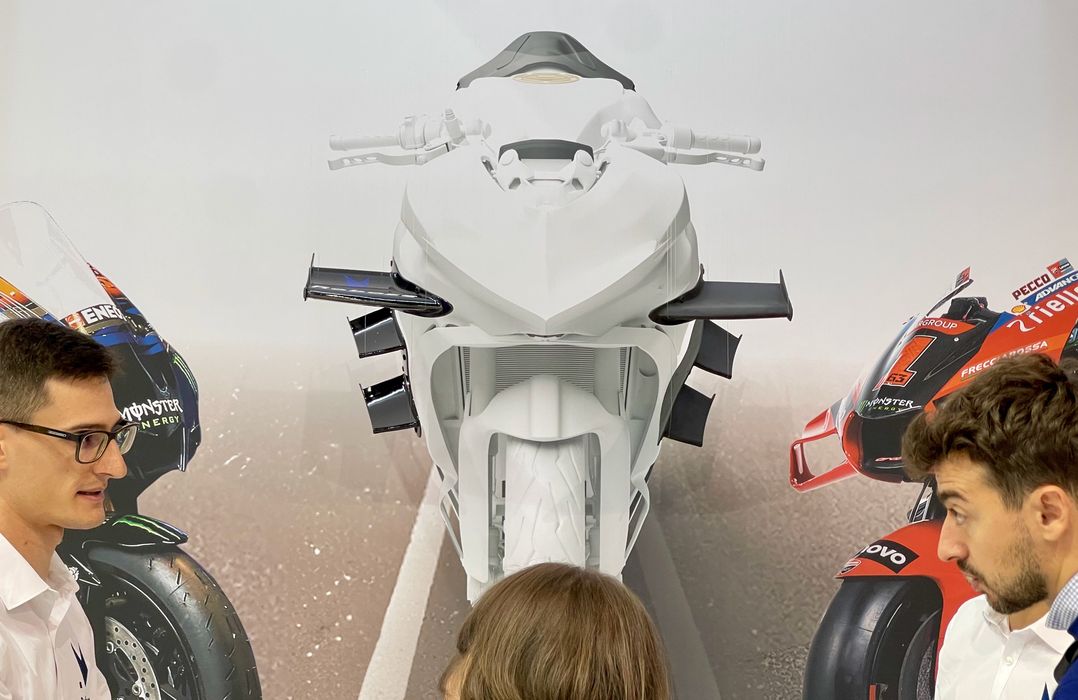
One of the other side benefits of Hypermelt’s pellet approach is the possibility of recycling. Scrap prints, when sorted properly, can be returned. There they are chopped up and reformed into pellets that can then be printed again in a circular fashion.
Hypermelt is implemented on the company’s flagship ARGO 1000 3D printer, which has a massive build volume of 1000 x 1000 x 1000 mm. That’s surely large enough to handle almost all parts, which can be made from very strong high performance materials.
Some years ago Roboze pointed out that parts made with high performance materials could actually substitute for metal parts in many low-temperature application scenarios, and that’s very true. Now with Hypermelt it seems that those parts can be made faster and for less cost.
Via Roboze