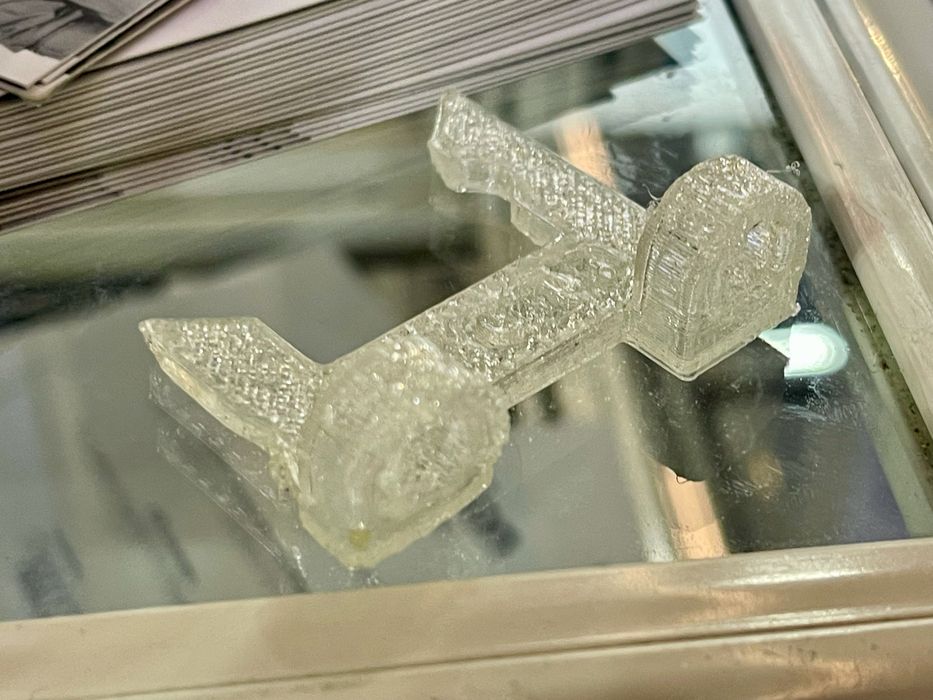
Create It REAL has developed an incredibly simple method of continuous 3D printing.
The Danish company produces advanced slicing software that is often used to optimize 3D print production in various ways. In the past, for example, they have partnered with a number of 3D printer manufacturers behind the scenes to improve part strength by providing powerful slicing algorithms.
The latest innovation is a method of continuous 3D printing, in which no operator is required to remove completed prints. This is a huge problem that really requires addressing: imagine if you couldnāt 2D print a document until you unloaded your printer. Thatās what todayās desktop 3D printer operators must deal with on every job.
Some attempts have been made to do so using unusual build plates, chemical adhesion release mechanisms, and even brute force pushing by the extruder to knock parts off the plate.
Create It REALās approach is a little different. They implemented the approach for a client that was printing flexible TPU midsoles for footwear. These must be peeled off the bed by the operator.
However, the new approach involves adding an āextractorā to the 3D model. This is an attachment that has a couple of holes, as you can see in the image at top.
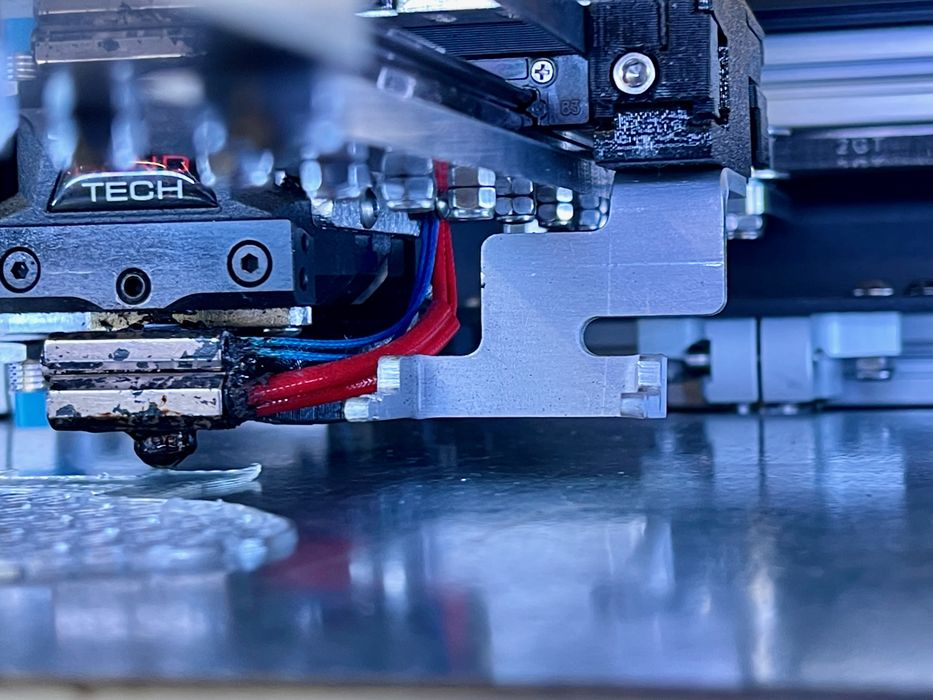
When the print completes, the print head moves into action. There is a special attachment to the print head that happens to have two pins that correspond to the holes in the extractor.
The software knows the 3D location of the extractor, and moves the printhead to slide the pins into the holes. Then the printhead rises slowly to peel the midsole off the plate.
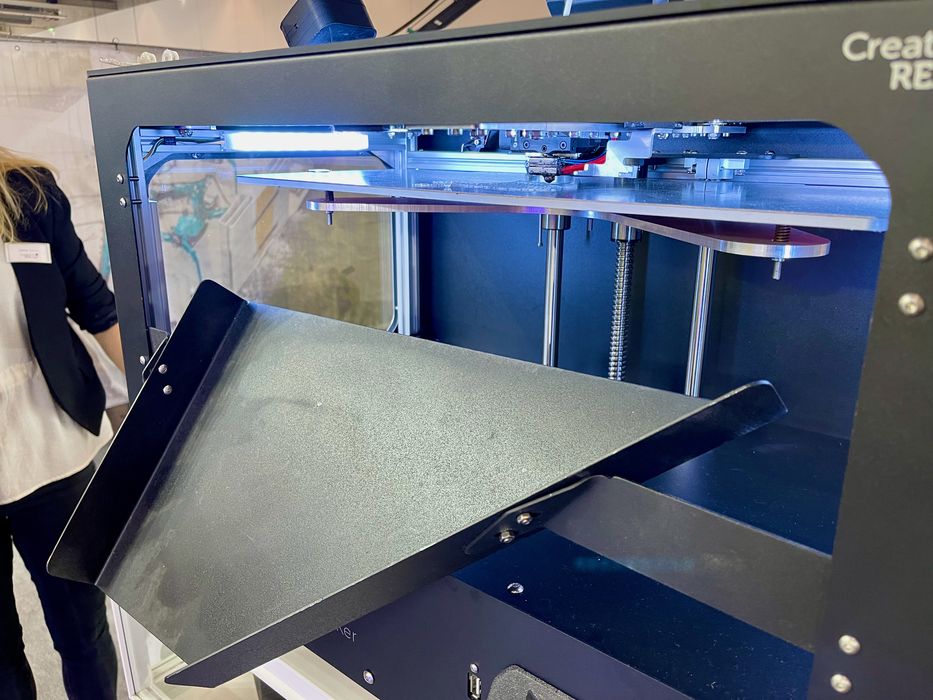
After pulling it off, the printhead moves forward, and the midsole is hanging in the air outside the plate. This is because the extractor was strategically located at the back of the midsole. The midsole then falls off into a slide and then into a bucket for collection. The extractors are then quickly snipped off, leaving the midsole complete.
In a nutshell: add a loop to a model and have the printhead pick it up.
Why didnāt anyone think of this before?
Could this approach work for non-flexible prints? I think it just might be possible, at least for certain 3D model geometries with the right adhesion surface on the printer.
Via Create It REAL