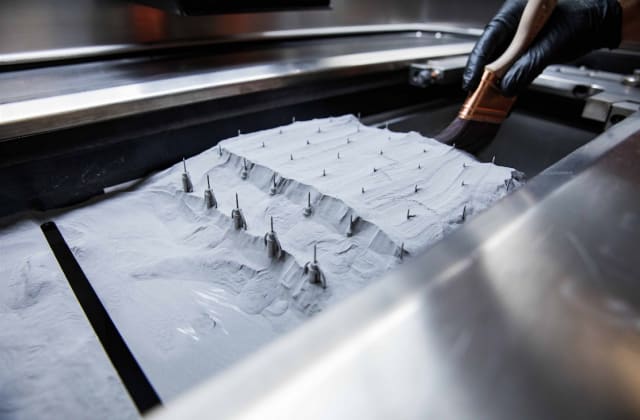
A Protolabs engineer’s perspective on the right DfAM approach.
Success in 3D printing is about more than just materials and hardware. While those are crucial factors, the whole process begins with creating designs that lay the foundation for the desired end product.
Design for Additive Manufacturing (DfAM) is the set of principles that serves as a reality check for the notion that 3D printing can create any part or product imaginable. The design process must consider the laws of physics when applying the multitude of materials used in various additive techniques.
While in theory the possibilities of 3D printing are endless, the design often has to counteract gravity to make some of the complex detail possible. For example, a highly detailed 3D-printed oak tree using stereolithography (SLA) will require supports for every branch during the printing process to make the final product hold up.
DfAM helps guide the 3D printing process through its inherent limitations, so that the technology can effectively yield some of the complex geometries for which it’s known. Beyond this, DfAM can help optimize the cost, speed and efficiency of 3D printing.
Some of the main guiding principles of DfAM include the following:
- Thinking from an additive vantage point instead of a subtractive one
- Taking the printing orientation into account
- Harnessing fewer extrusion lines
- Bonding separate parts into a whole
- Adding hardware within parts to adjust specs
- Minimizing complications
- Considering the final surface treatment
As more industries flock to 3D printing for production and not merely prototyping, more parts and products are being designed specifically for additive manufacturing using specialized software. The key is to use DfAM to achieve parts that hold up under use and over time.
“Particularly for the aerospace industry, you have to know how to design around the limitations of the technology,” says Eric Utley, technical sales engineer at Protolabs. “It’s simply not true that we can make anything. There are plenty of parts where we push back and say, ‘This hole is too large—it’s going to need supports; or this hole is too small and it needs to be sealed; or this part has too much material in the cross-section and it’s going to crack or warp.’ It’s very useful for engineers to have that skillset where they can spot those issues and know how to design for additive.”
According to Utley, one of the biggest challenges in achieving good design for additive manufacturing is making sure that there’s a consistent, seamless flow throughout the part. Unlike other manufacturing processes, with 3D printing, the layer-by-layer nature of the procedure has to result in a final product that seems natural, not choppy and disjointed.
Utley gives the visual example of a flip book. When you’re flipping through the individual pages of animation, they’re cohesive and flow seamlessly from one page to the next. The final 3D-printed part should be the same way.
“You don’t want material to be blinking in and out and for there to be really drastic changes occurring during the print,” Utley says. “When you look at the cross-section of a part, it should look like when you see a CT scan of a human being—there’s a really consistent flow. That will make for a more accurate part.”
One way to achieve this is to reduce the amount of excess material on the part that will later need to be removed. Not only does this cut down on waste, but it can also result in a smoother and more accurate final product.
Although generative design software can help with the 3D printing process, it’s not always accessible or reliable for additive manufacturing—though it’s getting better, says Utley. For example, a software program might recommend removing 30 percent of material from a part to maximize strength within certain dimensions. However, the software might not consider the best print orientations or suggest where material could be added to provide supports. That’s why it’s helpful to have product developers who are using the software trained in DfAM.
One of the main principles of DfAM is that different 3D printing methods require different design optimization. For example, a part printed through fused deposition modeling (FDM) or SLA can result in material and time savings if the bottom angle of the cuff feature is changed by 5 or 10 degrees. When using SLA or selective laser sintering (SLS), providing escape holes in a hollow model can reduce material waste, but a similar benefit doesn’t apply with FDM.
However, engineers can expect some core concepts to be true across 3D printing processes. For example, Utley says that the 45-degree rule—in which a wall at 45 degrees or steeper is typically going to be self-supporting—applies to a range of technologies.
“There’s a little bit of variance, but if you’re 45 degrees and steeper, you’re going to get by with the vast majority of 3D printing processing and get a self-supporting wall,” says Utley. “I always advocate adding radii to interior hard corners and edges to help relieve stress or material shrink.”
The question of whether a part requires a support structure or not is a central design question because it can be a limiting factor for other features. Utley says that as 3D printing processes go, Direct Metal Laser Sintering (DMLS) probably has the most design restrictions due to the necessity of support requirements. The process has a very low allowance or tolerance for overhangs. If you have anything shallower than 45 degrees, it increases the risk of a build crash occurring when printing with DMLS. Yet, Utley often sees well-designed parts with DMLS that emerge organically and require little to no support structures during the print because solid DfAM practices were deployed that are specific to DMLS.
Making circular-shaped holes with DMLS can also be challenging, so many opt for other shapes like the teardrop instead. In the aerospace industry, for example, it’s not uncommon to see rocket booster fuel channel parts that contain a teardrop cross-section for this reason. It’s a notable aberration as thousands of years of subtractive manufacturing processes have tended to opt only for circular holes that are drilled. With additive manufacturing, the circle isn’t always the most ideal shape for negative space.
Read the rest at ENGINEERING.com