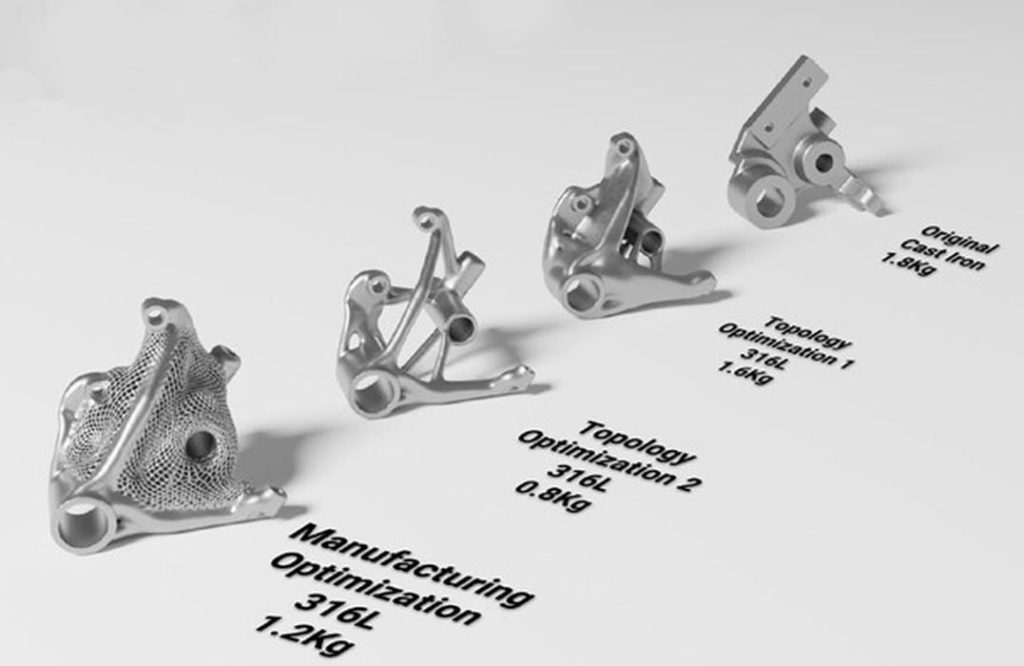
Cognitive Design Systems understands that lightest does not equal optimum and not all 3D prints are manufacturable.
Toulouse, France, produced mathematician Pierre de Fermat in the 17th century and post-Impressionist painter Henri de Toulouse-Lautrec in the 19th century. In the 21st century, being home to Airbus, the city is known for its production of aircraft. The aviation giant employs 28,000 people in the Toulouse area and its activity has created a hotbed of technology and startups. One of them, Cognitive Design Systems, or CDS, offers aviation and automotive generative design software and service.
CDS is certainly capable of producing the lightest possible partsāthe stringy, breakable shapes too often paraded before us as wonders of lightening technology. The least weight, if the only criteria, does that. However, these light parts will never see production because they canāt be manufactured (except with a 3D print) and are obviously prone to failure if their stringy bits are subject to compressive loads or just simply look too goofy. CDS, which seems to employ sound engineering principles (not just solve for a single variable) has taken the power feed bracket shown above and added a mesh. The mesh makes the bracket 50 percent heavier than the āoptimumā design, but the stringy members will not be crushed or buckle if they are subjected to a compressive load.
Look closely, and you can see that unlike other generative design software, which may use a lattice, the CDS mesh smartly adapts and flows with the optimized geometry.
Why has no one else thought of this?
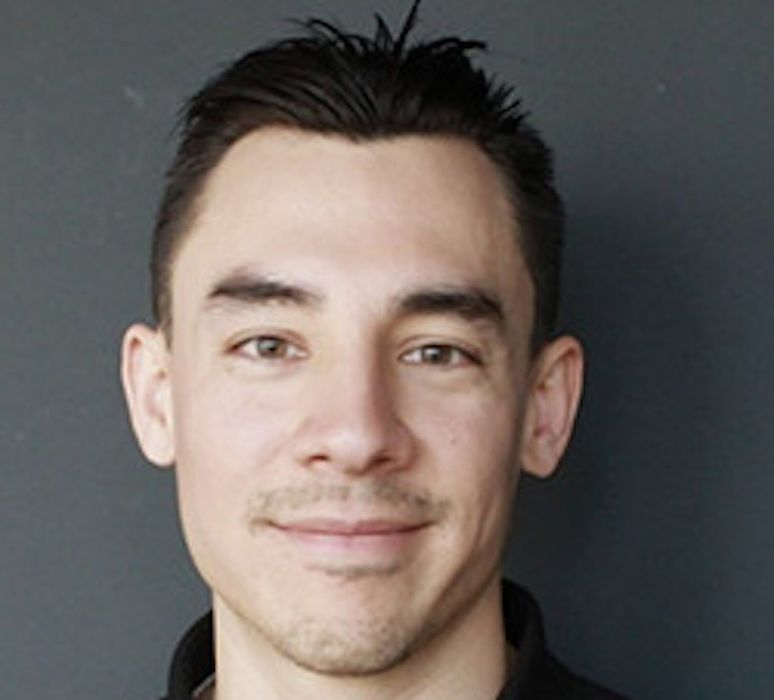
Intrigued, we spoke to Vincent Ung, COO and cofounder of CDS, to find out more about the company. Ung worked for several companies in Asia before settling in Toulouse, France, the country where he received his higher education. He has just returned from Formnext, the 3D printing tradeshow held in Frankfurt, Germany.
CDS took on its name in March 2021, but its software has been in development for four years. Today the company has 13 employees, most of whom are involved with writing software and consulting. Unlike most startups, CDS is bootstrappedāthe term investors use for companies they are not investing in. CDS will be looking for investors, says Ung, but for now, it is doing well on its own, having secured customers such as jet engine maker Safran and automakers such as Toyota, Nissan and Mitsubishi.
CDSā revenue model relies more on using generative design software than on selling it. The company will just as soon analyze your parts to see any lend themselves to optimize and 3D printing. If so, they will do it all, using their own generative design software in the process.
Currently, 80 percent% of the companyās business is from providing a generative design service, says Ung. The rest of the revenue comes from software licensing.
Itās a smart approach for a young generative design software company. With every design and simulation company offering generative design, as well as several companies specializing in generative design (such as nTopology), it would be hard for a small French firm to be heard above the din. It would take an immense marketing campaign and marketing is typically not on a startupās agenda or in its budget. Wisely, CDS takes on the work of generative design and creating 3D printable designs. Consulting fees, after all, can generate hundreds of euros an hour, while software licensing can generate about a hundred euros a month. The service-first approach generates more revenue up front, which is available for growing the company.
It is also easier for a company to offer its expertise to companies that have jumped into generative design and 3D printing sold on a push-button experience only to find themselves in over their heads. Kind of like the cocky engineer who took apart a washer trying to fix it, and then could not fix it or put it back together. But why bring that up?
More importantly, CDS gets to hone its application on real-world projectsāas opposed to big software companies whose applications are developed by software developers with little or no engineering experience and tested on simple partsāor at best, libraries of parts meant to be representative of various industries.
CDS offers Cognitive Additive, which currently does generative design for 3D printing but is on its way to offering generative design for molds and CNC machining.
The optimization used by CDS is part open source and part proprietary. What really sets CDS apart is the risk analysis of a part design that summarizes what could possibly go wrong with your 3D print, saving you from trial and error and the waste that is the bane of 3D printing.
Cognitive Additive will optimize the orientation of the part in the vat so you can pack the most parts per print run.
Read the rest at ENGINEERING.com