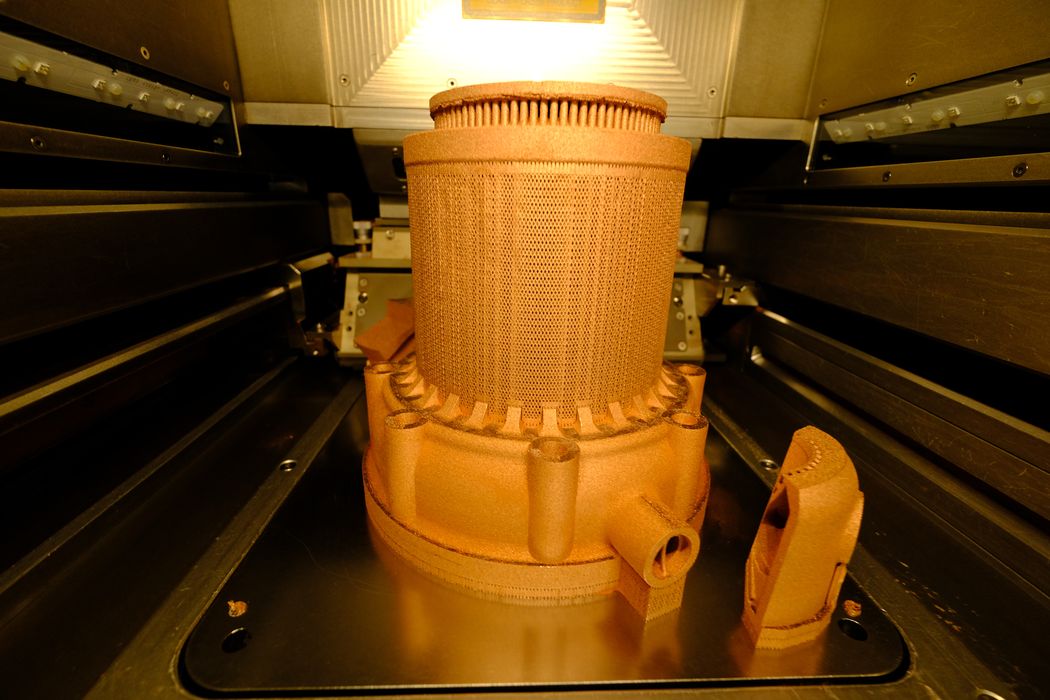
The German Institute of Materials Research at DLR has been working on ways to 3D print space propulsion systems.
In recent years there has been a bit of an explosion of interest in space-based business and exploration. That’s because SpaceX has very clearly demonstrated that reusability is the key to future access to space. In the past the entire rocket was considered disposable, making flights extraordinarily expensive and affordable only by major countries. Reusable rocketry tips the scale and enables many more parties to get involved, hence the increased interest.
As a result, aerospace companies around the world are quickly designing reusable rockets, some faster than others.
A key ingredient in the success formula for these ventures is additive manufacturing. There are a number of key advantages to 3D printing rocket engines, not the least of which is lower weight. The engine can be produced in one or a few parts instead of many. This eliminates the need for bolts and nuts holding the components together. Single prints also dramatically reduce the number of seams that can fail, increasing reliability.
However, while all that sounds promising, how exactly does one 3D print rocket engines?
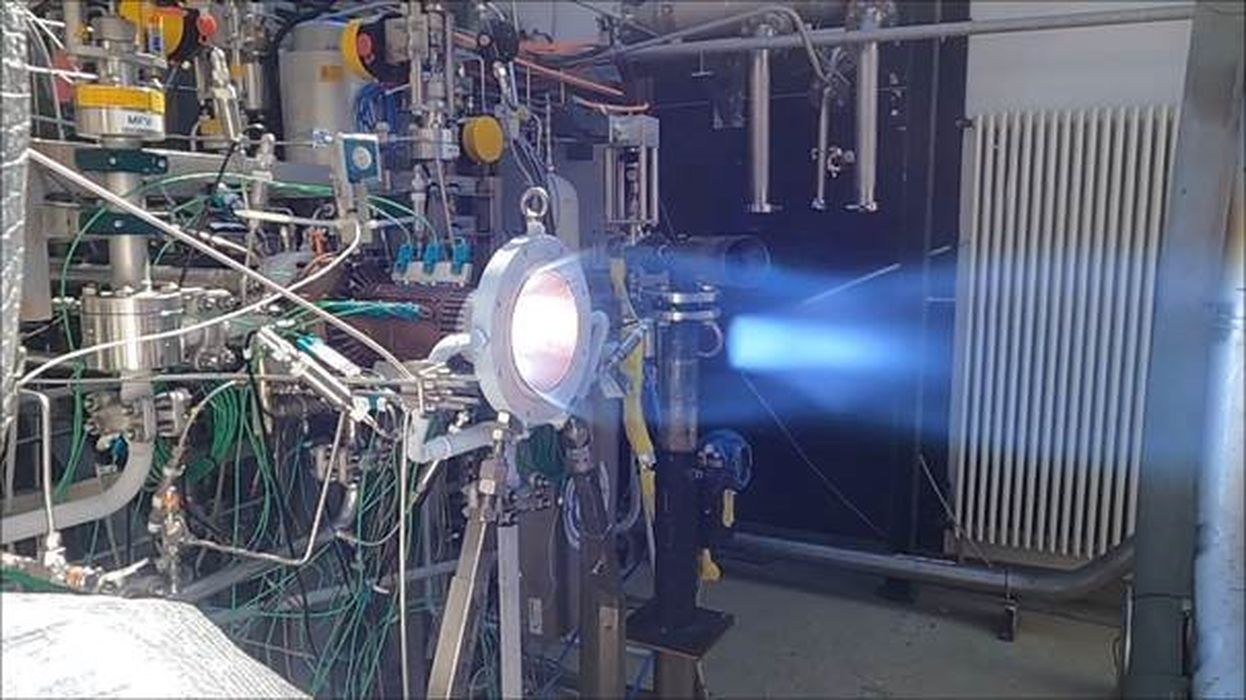
3D printing anything in metal is a complex affair, involving fine tuning of print parameters, temperatures, speeds and material chemistry. This is particularly important when producing rocket engines that not only are efficient, but also must be reused again and again.
Few outside of SpaceX know much about this, and that’s where DLR comes in. A recent release from the organization details some of their work in this area.
They’ve started a project called “3D-LoCoS”, meaning “3D Printing for Low Cost Space Components”, where they’re going to figure out exactly how to 3D print space components.
DLR Project Leader Jan Haubrich explains:
“New manufacturing processes are the key to increased performance, improved cost-effectiveness and pave the way for reusable launcher technologies.
Additive manufacturing processes enable an entirely different way of producing components and are a fairly young technology compared to most other processing methods. For complex designs in particular, it enables components to be printed more quickly and cost-effectively.”
For example, they’ve already designed and printed, using a LBPF process, a new design for a copper combustion chamber that includes a unique cooling system. They’ve managed to perform no less than six hot-fire tests of this design on their own rocket engine test stand, located in Lampoldshausen, Germany.
The tests will show whether the design is truly capable of reuse, and ultimately the techniques developed by DLR will make their way into commercial manufacturing. Future rockets will no doubt make use of this research.
Via DLR
Hi Kerry, FYI, the DLR stands for Deutsches Zentrum für Luft- und Raumfahrt, which essentially translates to the German Center for Air and Space Travel. They translate it as German Aerospace Center. It’s not exclusively a materials research institute.