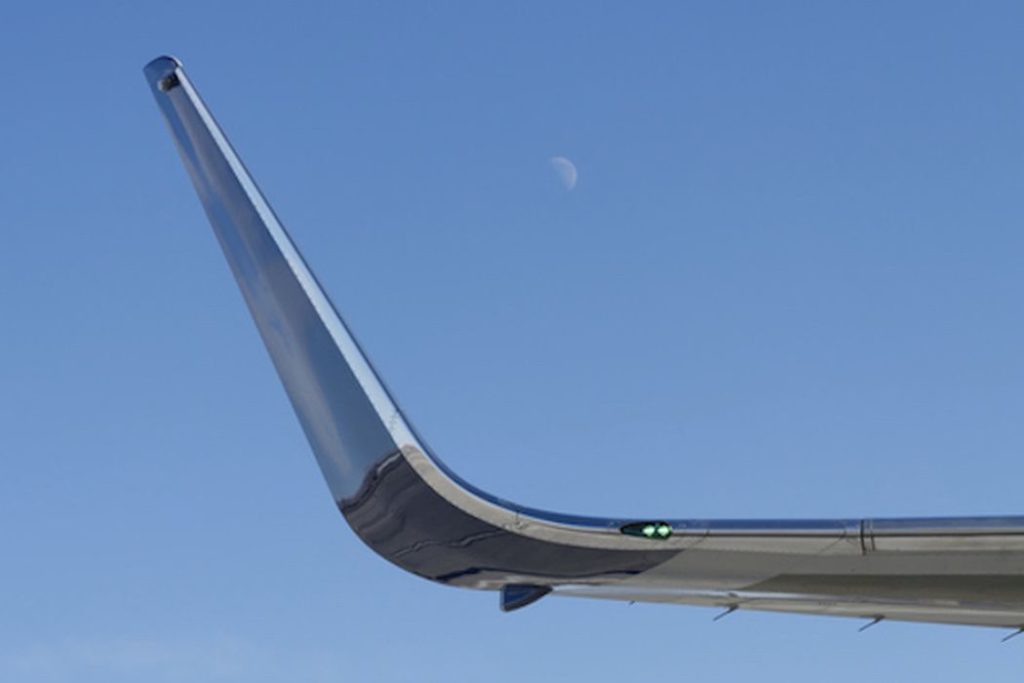
Vartega employs a patented chemical-based process to rescue carbon fiber waste from an eternity in the landfill.
As the demand for composite materials like carbon fiber continues to grow, the manufacturing industry is faced with the possibility of surpassing production capacity. At the same time, carbon fiber waste is an alarming problem. Carbon fiber reinforced polymer (CFRP) is utilized in massive applications such as wind turbinesāthousands of which are removed from service annually. The aerospace industry has an estimated scrap rate of 30 percent. Over 24,000 tons of carbon fiber waste ends up in landfills or is incinerated every year, despite being worth as much as $630 million.
It would make sense for companies to reclaim the valuable materialāexcept that carbon fiber is notoriously difficult to recycle due to its fibers being bound by an extremely stable epoxy thermoset resin matrix. (Background: Carbon fibers are woven into fabrics and impregnated with plastic to form prepreg. This prepreg is formed into different shapes and cured into solid composite parts, which donāt melt down like steel or aluminum would.) Since carbon fiber is non-biodegradable, any waste sent to landfills will stay there forever.
Fortunately, a Colorado-based company called Vartega has patented a low-energy solvolysis process for recovering carbon fiber from high-grade, pre-impregnated scrap and dry fiber fabrics. The recycled carbon fiberāwhich has been found to exhibit the same mechanical properties as virgin carbon fiberācan be incorporated into intermediate materials including non-woven fabrics, thermoplastic pellets, and 3D printing filaments.
Engineering.com caught up with Vartegaās CEO, Andrew Maxey, to learn more about the technology and its applications.
Vartegaās Origin Story
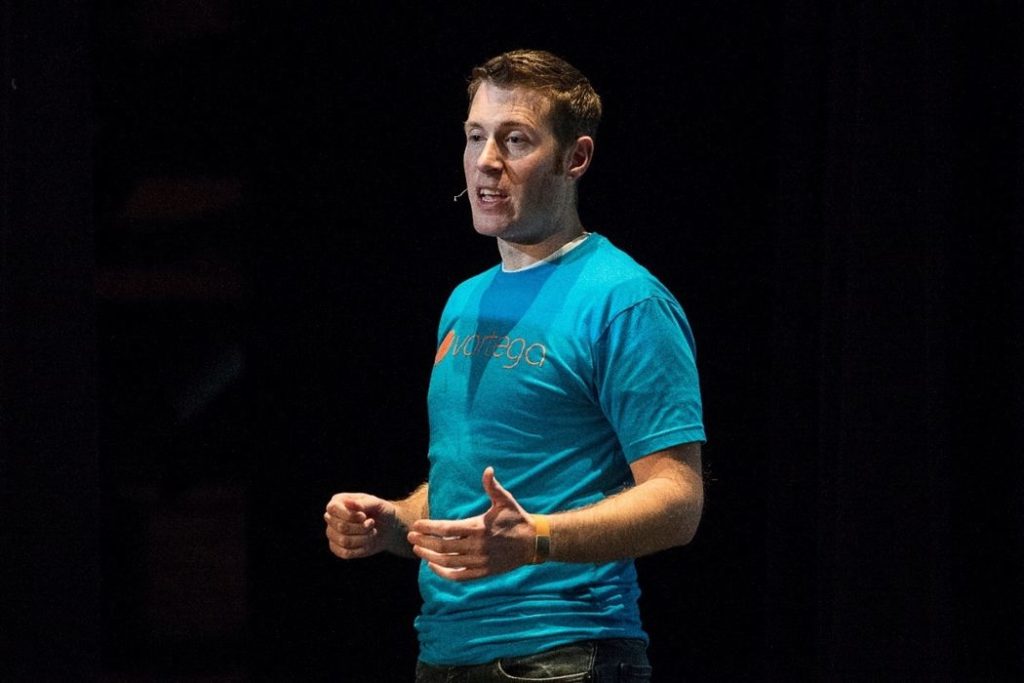
Maxeyās interest in carbon fiber stemmed from his love for cycling, having worked in a bike and ski shop in Northern Michigan where he grew up. One day, when a customer had accidentally destroyed their new carbon fiber bikeās frame (by driving their car into the garage with the bike on the roof rack), a fascinated Maxey took the opportunity to cut through the frame to see what carbon fiber was all about.
A decade later, Maxey completed his mechanical engineering degree and worked in high efficiency building systems, where he learned about sustainability and green design. As his career evolved, he became exposed to textiles and recognized carbon fiber as a high value textile. When going on to oil and gas processing, Maxey thought of leveraging carbon fiber technology in the petroleum world.
āI decided to try a proof of concept in my garage with some of the background I had in textiles and oil and gas,ā recounted Maxey. āI had several epic failuresājust zero success for a long timeābut finally stumbled upon the foundation for our chemical-based recycling process for uncured carbon fiber composites. I figured if the dots could be connected from the captive supply in the waste stream to the unmet demand for low-cost carbon fiber, that would be pretty profound.ā
Maxey and three other co-founders started Vartega in 2014 as a side hustle while working in other jobs. In 2016, they raised capital, received grant funding, and proceeded to scale up their technology full-time.
Read more at ENGINEERING.com