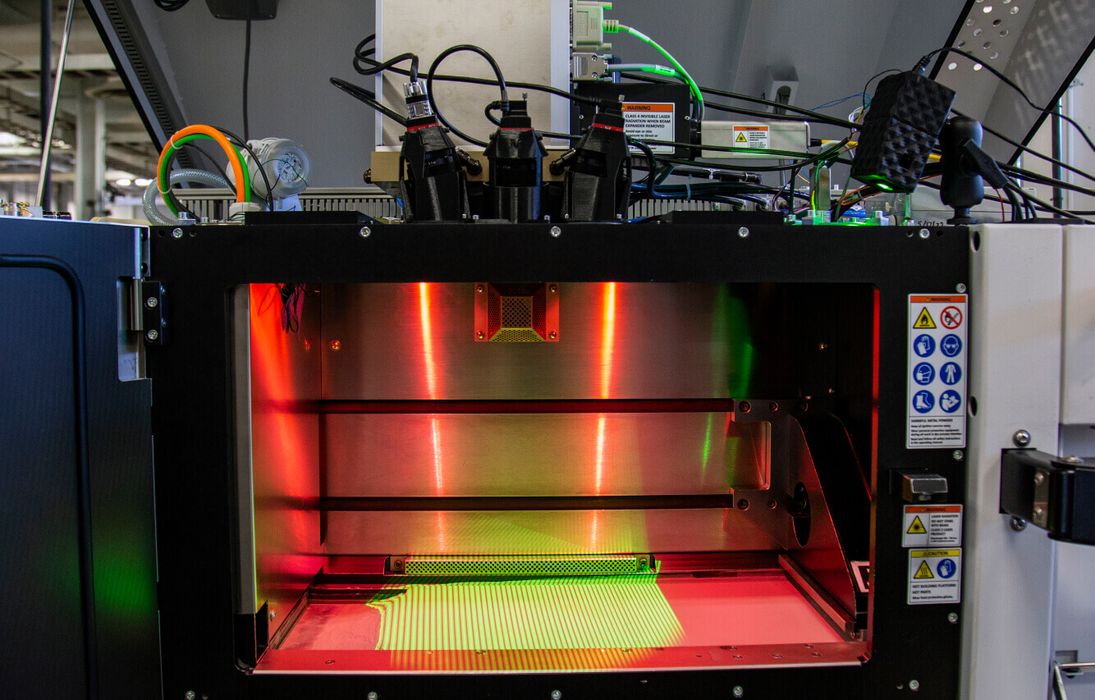
Phase3D’s “Project Fringe” delivers real-time 3D monitoring to 3D printers.
The Chicago company has developed a system involving a series of sensors that can be integrated into certain PBF 3D printers. The system is then able to generate a 3D representation of the ongoing print job.
This presents the opportunity for real-time monitoring: the 3D model generated by observation of the print job can be compared, layer-by-layer, with the intended design from the original CAD file.
If there is a deviation, Project Fringe will detect it instantly.
Project Fringe does two things:
- Detect and display defects in 3D form
- Quantifies actual results with real measurements
The first function is unique, as almost all PBF quality systems simply display a 2D image of a layer, and that’s where deviations could be detected. With Project Fringe, however, an actual 3D view of the print progress is produced. This can be compared to the CAD design to identify defects.
This provides a far better context for analyzing issues that occur during a print job. It may be that some issues noticed with 2D representations are actually OK if seen in a 3D context, for example.
The second function is quite important. Project Fringe provides numerical data for the print progress. When a deviation occurs, those numbers can be used to solve the issue directly, whereas systems with only “detection” have to guess at the degree of fixing required.
These two features combined should almost certainly increase print reliability and even reduce the number of failed print jobs.
Project Fringe is potentially installable on any PBF 3D printer, although some integration work is obviously required.
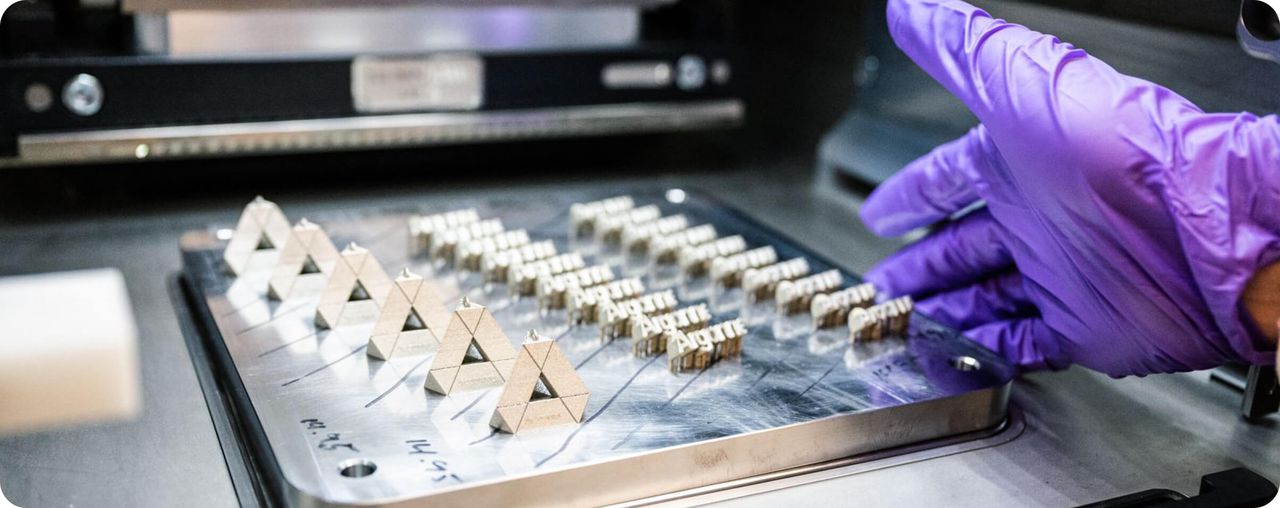
So far, the company has developed integrations for the Desktop Metal ExOne Innovent and EOS M 290, both popular machines. The company is also developing integrations for the GE M2, Renishaw AM400, and 3D Systems Pro X 200. It’s likely they will develop additional integrations, particularly so if approached by potential customers.
The sophisticated real-time monitoring system from Phase3D appears to be well-beyond the relatively basic monitoring solutions that are only beginning to appear on equipment from major providers.
In fact, most typical PBF systems do not include any monitoring features. This leaves the operator in difficult situations, as they start the job and then hope if finishes properly. If not, considerable time and materials would have been wasted.
With the Project Fringe solution it would be possible to not only detect a failure early on, the extra numerical data provided would allow for engineers to quickly adjust the print job to compensate for the problem and restart.
Less waste, more printing. That’s a good thing.
Via Phase3D