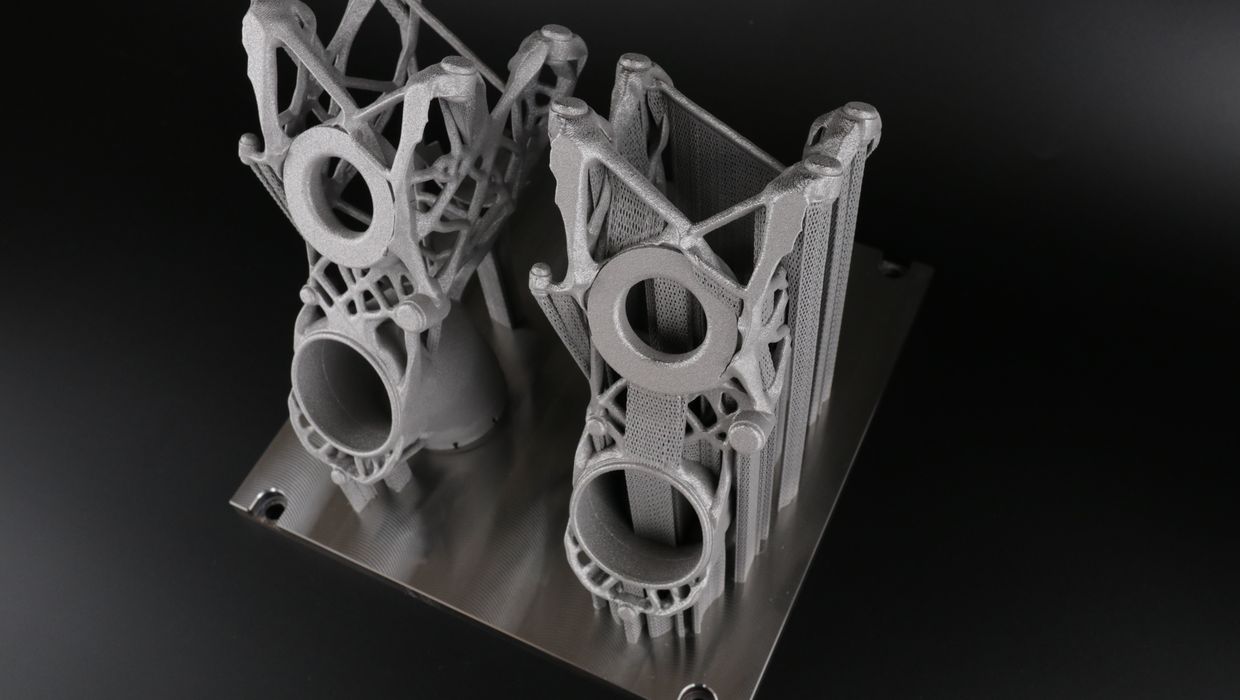
EOS announced a new real-time feature for their metal 3D printers called “Smart Fusion”.
The company produces a well-respected line of metal 3D printers that use the LPBF process. While this process can produce finely detailed metal parts, it can be challenging to tune the parameters to achieve optimal results. That seems to be the goal of Smart Fusion.
Tuning an LPBF 3D print job is difficult, as one must balance multiple factors, including temperature, speed, cooling, and power to ensure the meltpool properly fuses the fine metal particles together. The resulting solid metal has to take on a suitable microstructure to ensure it meets the engineering requirements.
If these factors are not optimally balanced, the job effectively fails because the part doesn’t meet specifications. This results in a second (or third, or more) runs with adjustments to compensate. Due to the high cost of operating LPBF equipment and the cost of metal powder, these iterations can dramatically raise the cost to produce the metal part.
How Smart Fusion Works
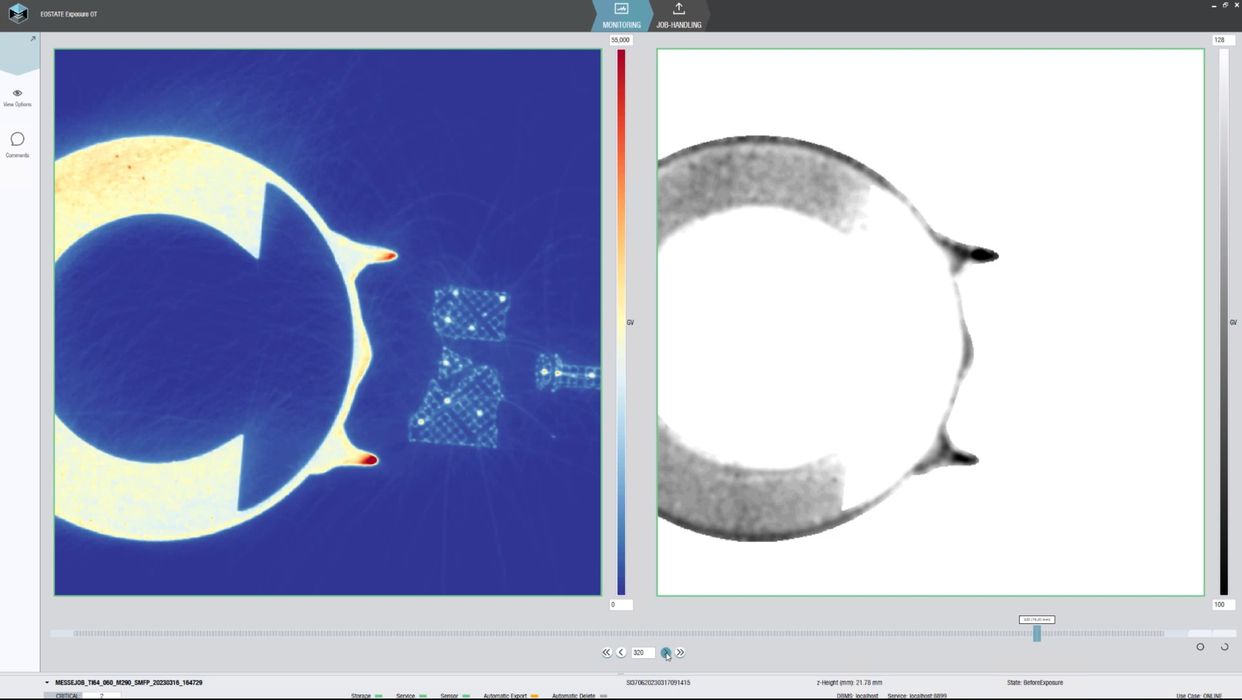
Smart Fusion is a real-time function that runs during metal 3D print jobs to manage this delicate balance, but it turns out it does a lot more. EOS said:
“The technology eliminates the need for most support structures, minimizes material use, reduces post-processing requirements, and lowers the cost-per-part for metal AM applications.”
That’s quite a list of benefits, but how does Smart Fusion do this?
In concept, it’s actually quite simple: the system monitors the current state of the meltpool generated by the moving laser, and dynamically adjusts the laser power. EOS explains:
“Smart Fusion measures the amount of laser power (energy) which is absorbed by the powder bed. A special high-resolution camera overlooking the build chamber monitors each layer’s meltpool emissions via proprietary technology, and data is fed back to the laser where it is adjusted. This results in homogeneous energy distribution across the whole build platform, thereby reducing stress in the parts and avoiding metal overheating and movement in undesired directions.”
The secret to the system is in the software. EOS uses “advanced algorithms” to analyze the collected images to derive the varying laser power settings as the job proceeds.
EOS said Smart Fusion enables faster results:
“Customer Beta testing of the Smart Fusion solution has consistently resulted in performance that is two to five times (2x-5x) faster than the leading competitors in the metal AM market.”
That’s impressive, and I suspect it has more to do with avoiding print iterations than actually increasing print speed. The goal is to produce a proper part, and all the effort and resources spent to get there is apparently significantly reduced with Smart Fusion.
Reduced Support Structures and Material Combinations
What’s quite interesting is that the system decreases the need for support structures. Support structures are often needed to compensate for thermal issues incurred during printing, and they can be quite complex. Even worse, they must be carefully removed after the print completes, often in a laborious manual process. Anything that can reduce the use of support material would be extremely beneficial.
As you might expect, Smart Fusion’s algorithms are tuned for specific machine-material combinations. EOS has made available implementations for their M 290, M 300-4, and M 400-4 machines for Inconel IN718, Titanium Ti64, and Aluminum AlSi10Mg. They have intentions of expanding these combinations in the future. Smart Fusion can be added to these systems at prices ranging from US$30K and up.
Via EOS