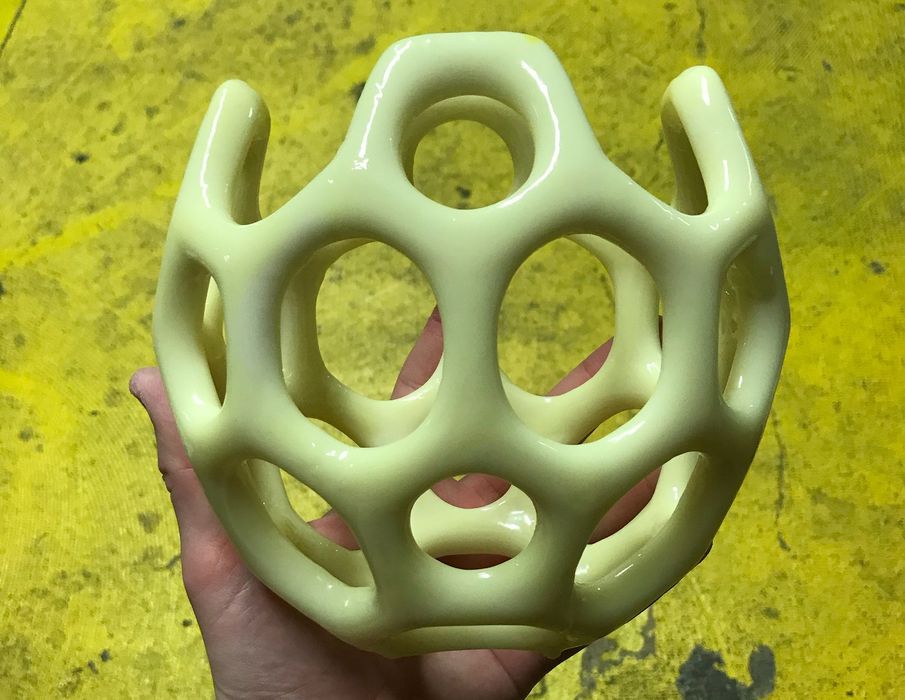
Essentium has signed a letter of intent to acquire 3D print startup Collider.
Essentium has been gaining steam in recent years with their focus on high-speed filament 3D printing and use of engineering materials. It now seems they’ve been sufficiently successful to enable the purchase of another company, Collider.
But who is Collider and what do they do? We first encountered them back in 2017 where their unique 3D printing process was described.
In a few words, Collider’s technology is a resin/DLP system that instead of 3D printing a complete part, prints a hollow shell of the part. Then standard — and strong — injection molding material is injected into the hollow.
Here’s a video of their process:
As you can see, the sacrificial mold is soluble. This is easily removed after the injection mold material has solidified. The result is a part that is effectively an injected molded part with all the benefits of that process. Yet it was made (partly) with 3D printing technology.
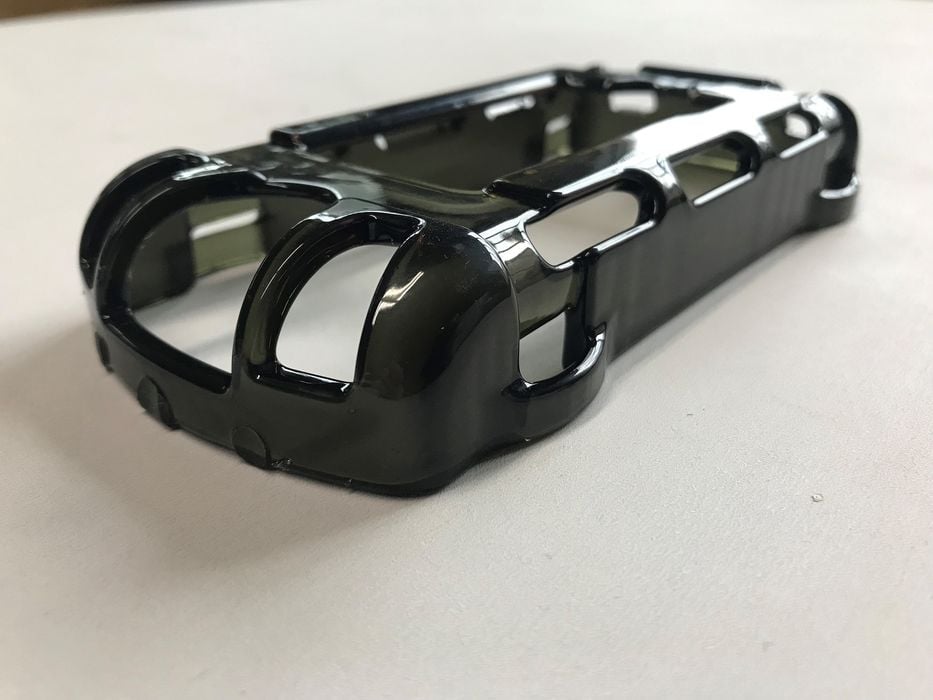
The Collider process enables production of smaller volumes of injection molded parts. Consider that a typical injection mold application involves the creation of a metal injection mold. This is a time-consuming step, and one that is often quite expensive, with tens of thousands of dollars being typical for such metal molds.
Once made, those metal molds can be used to rapidly produce mass quantities of parts because the metal mold will be effective for many, many runs. It’s also necessary to produce high volumes because the huge cost of the mold must be defrayed over large numbers of parts.
Lower-volume production with a metal mold doesn’t make sense because the per-unit cost allocation of the mold could make the end-part cost higher than the buyer would pay. Thus you often see a minimum number of parts required to justify the start of mass production.
But Collider’s tech negates that barrier because the mold produced in their system costs the same each time. Sure, it’s higher than the cost of a mold being allocated over a million mass produced parts, but it can be sufficiently inexpensive to allow for production at far lower volumes.
In other words, Collider tech can light up low-volume applications that would not otherwise be financially feasible.
Now (or at least soon) they’re working for Essentium.
Essentium explained:
“As manufacturers look to respond quickly to market changes, many are challenged with late-stage product development. Creating injection moldings or specific tooling for low-quantity parts production is a costly and time-consuming process. Instead of a permanent, hard tooling mold, Collider’s DLP 3D printing technology, creates a thin photopolymer shell which is then injected with a variety of materials and cured through a chemical process. After some post processing, a production-quality part or mold is left.”
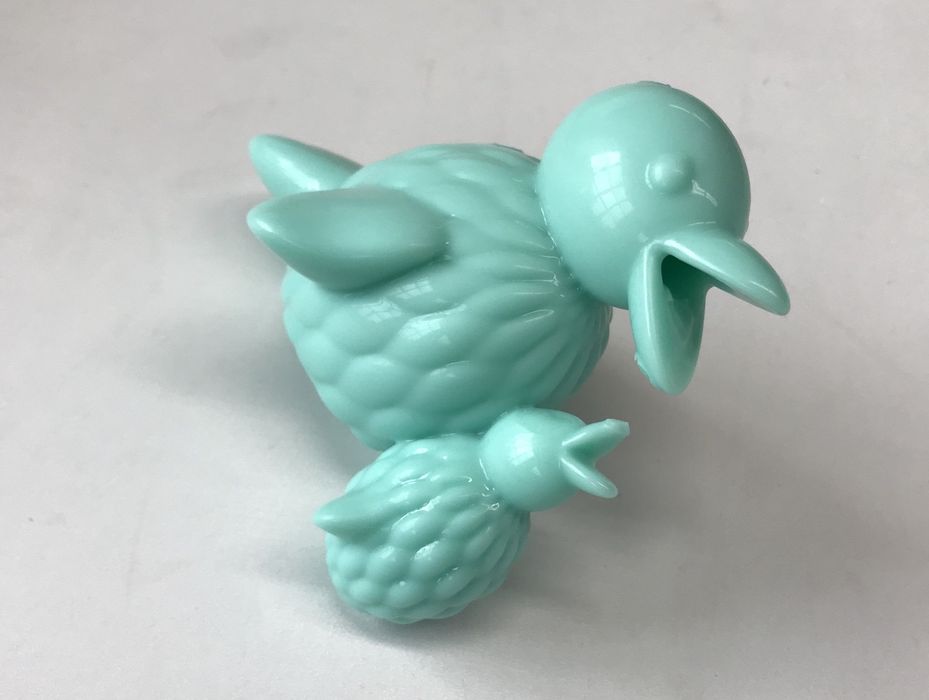
The most interesting aspect of Collider tech to me is that once the mold is 3D printed, almost any injection molding material can be used. This includes standards like ABS, but also unusual foams, flexibles, conductives and many more.
For Essentium clients, this opens up many new application possibilities well beyond their current slate of engineering materials.
Essentium’s CTO, Jeffrey Lumetta, said:
“Collider has a lot to bring to the table. Their innovative method of bringing together proven technologies to create high-value use cases has already proven their industry value. We see significant opportunities in tooling for low volumes of parts and the ability to manufacture geometrically complex, custom parts on-demand and quickly. In addition, this represents Essentium’s first entrance into photopolymer AM technologies and will expand product offerings in several areas—especially when combined with our unique material science capabilities.”
Essentium said that Collider’s former CEO, Graham Bredemeyer, will take over a brand new “Photopolymer Group” within Essentium.
We now have Essentium branching out to include different 3D printing processes, as have several other major 3D printer manufacturers in recent months.
Via Essentium