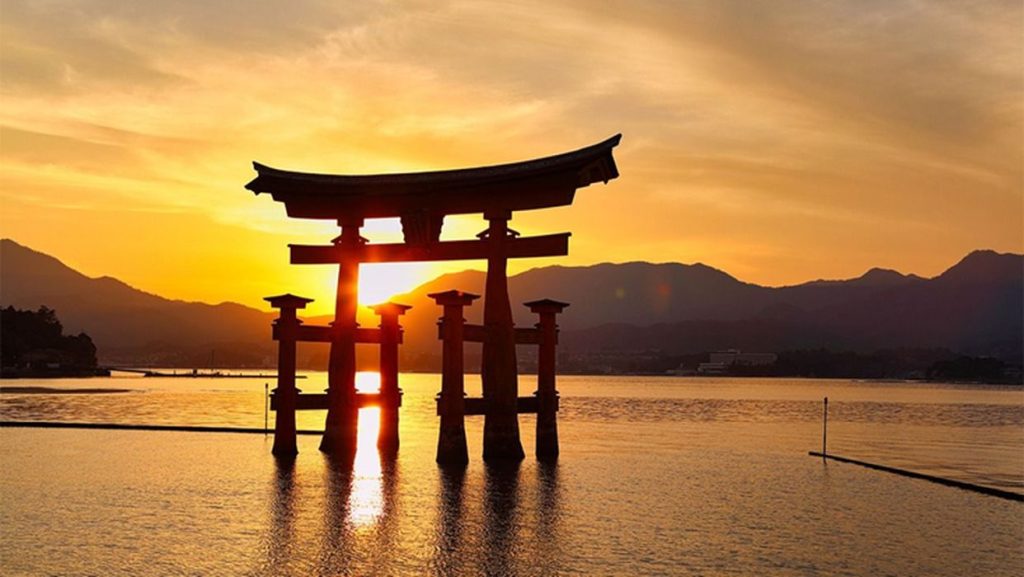
Charles R. Goulding and Preeti Sulibhavi look at the incredible developments in 3D printing and robotics that have taken place in Japan.
Japan is a highly developed free-market economy. It is the third largest in the world by nominal GDP and the fourth largest by purchasing power. Japan’s nominal GDP for the 2020 calendar year was US$37B. We have previously written about Sony and Toshiba in previous articles. But Japan’s influence on 3D printing goes much deeper.
The incorporation of 3D printing in manufacturing has created some new challenges including the need to additivity build large objects and the need for increased productivity. Manufacturers are turning to robotics as a cost-effective solution for these issues. Japan is a leading robotics manufacturer.
NIKON
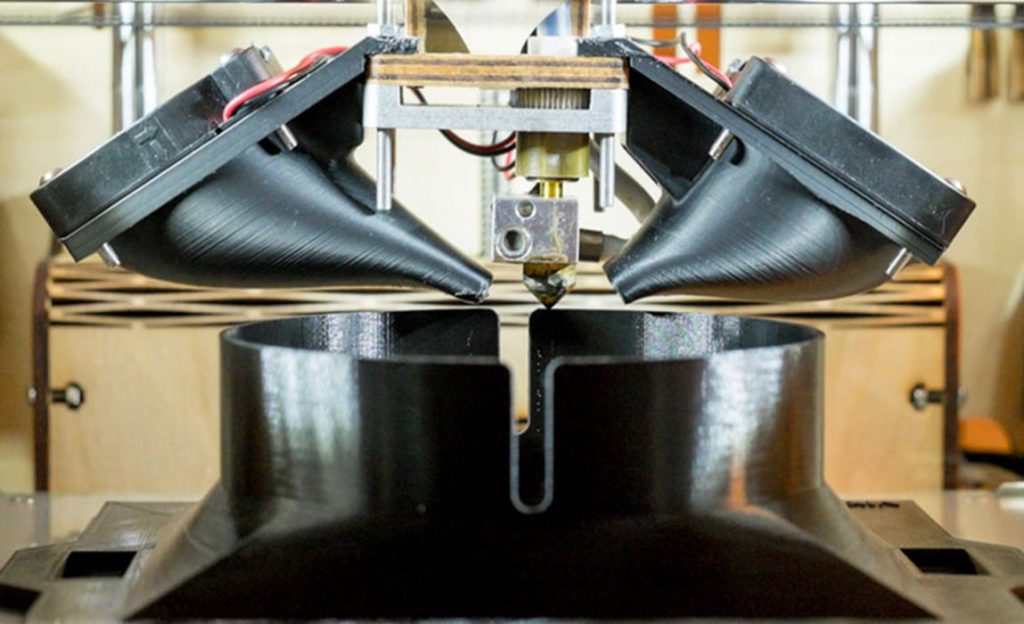
Nikon, the Japanese electronics giant, has just announced that it has acquired California’s Morf3D Inc for an undisclosed amount. The 3D printing design and engineering services company, which has received investments from companies such as Boeing, is known for its expertise in metal 3D printing of structures and build processes. With the limited demand for stand-alone camera products, Nikon is looking to expand into 3D printing. Nikon has also invested in Carbon, for research into regenerative medicine and equipment used for quality control of 3D printed components. And as recently as September 2022, Nikon launched a public offer to acquire SLM, a pioneer in metal 3D printing.
Leading Robotic Sector
Japan is a world leader in robotics. There are a few major Japanese robotics companies. Fifty years ago, the Kawasaki-Unimate 2000 was the first Japanese-manufactured industrial robot that was initially based on American design. It evolved to meet the needs of Japanese car manufacturers.
FANUC
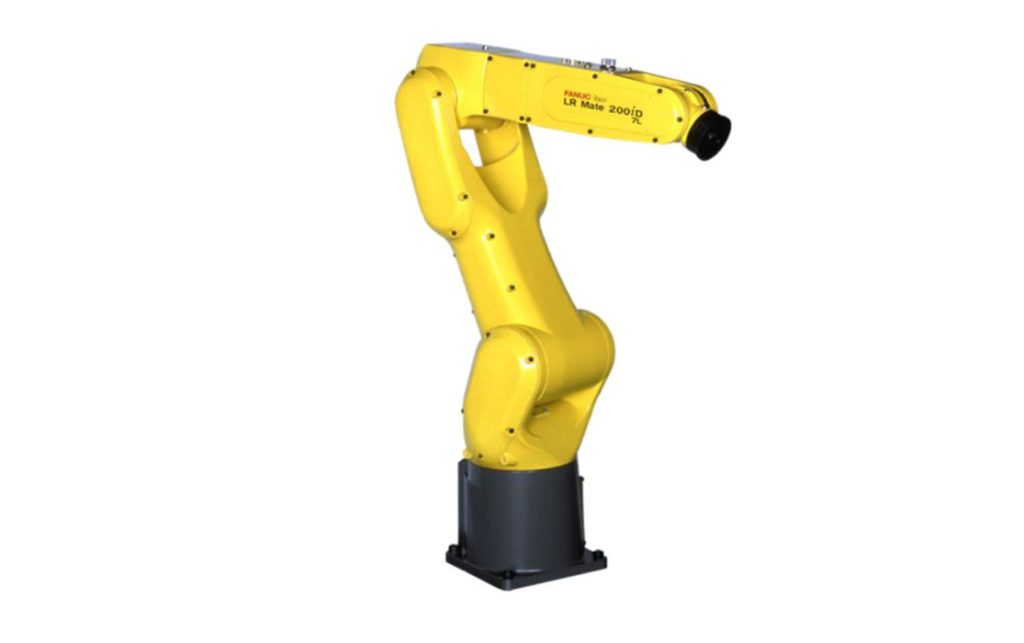
Top robotic manufacturer, FANUC, is producing various robotic models to accommodate automation in a myriad of industries. Their line of articulated robots can be used in numerous applications in industries such as automotive, medical, electric and welding. Fanuc Delta robots can achieve high speeds and offer pick-and-place applications. Fanuc Scara robots handle different assembly types and sorting applications. Fanuc also has six-axis robots with a work envelope of over 10 ft and small tabletop robots that can assemble electronics.
Fanuc robots are used for post-printing processes including washing, curing and finishing of 3D printed parts.
Daifuku
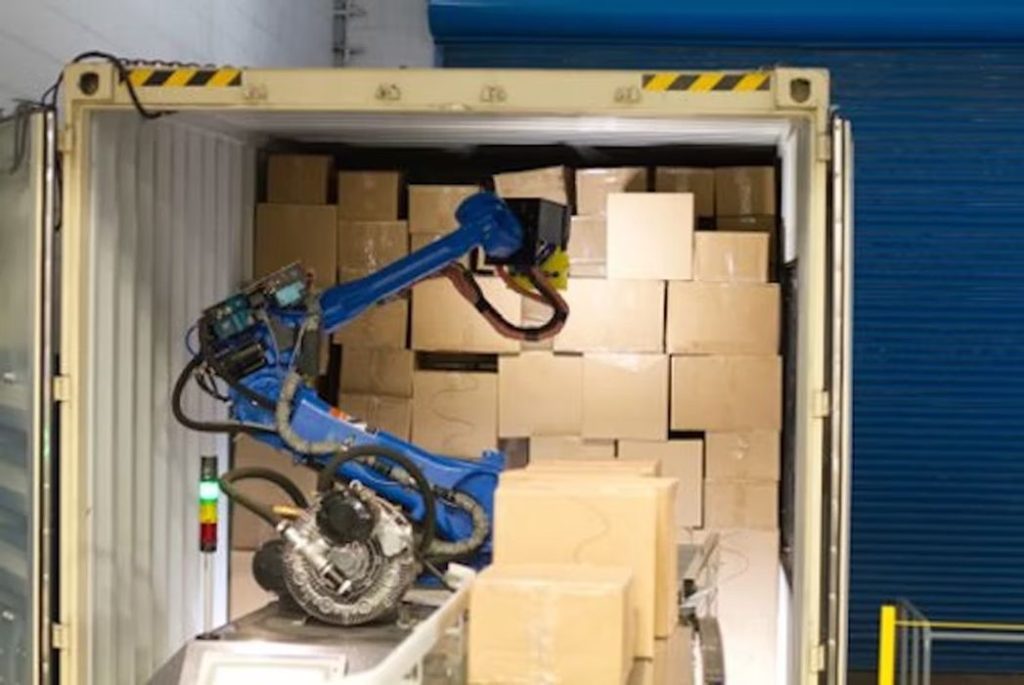
Daifuku is a leader in the field of factory automation, particularly intra-factory logistics. Most of Daifuku’s sales are derived from storage and transportation systems for factories, production lines for cleanrooms and automobile plants, and automated systems for airports. Daifuku’s subsidiary, Winright, is heavily invested in robotics and automation as it won the NextGen Game Changer Award for its robotic truck unloader (RTU).
TCT Japan (Formally 3D Printing Japan) is an influential 3D printing and additive manufacturing event that draws industry professionals to Tokyo to address the challenges of incorporating the adoption of these technologies into the Japanese manufacturing industry.
With recent aggressive actions taken by South Korea, Japan could be looking to increase its defense budget. With the war in Ukraine, many NATO countries such as the UK, Sweden, Denmark, Norway, and Germany have increased their recent defense budgets as well. We see Japan following suit. 3D printing can help Japan in achieving a better defense arsenal.
Major hurdles to wider acceptance of additive manufacturing in Japan include the traditional Japanese business culture, which is generally hesitant to try out new technology.
Additionally, most of the Japanese industry still believes that 3D printing is cutting-edge technology but is unaware of U.S. companies that can help them take 3D printing to mass production. Therefore, the key to success for U.S. additive manufacturing is brand awareness and value proposition among Japanese vendors.
The current use of industrial 3D printing machines is mostly for R&D purposes, but it’s projected that the market will be open for mass production by additive manufacturing (AM) soon.
The Research & Development Tax Credit
The now permanent Research and Development (R&D) Tax Credit is available for companies developing new or improved products, processes and/or software.
3D printing can help boost a company’s R&D Tax Credits. Wages for technical employees creating, testing and revising 3D printed prototypes can be included as a percentage of eligible time spent for the R&D Tax Credit. Similarly, when used as a method of improving a process, time spent integrating 3D printing hardware and software counts as an eligible activity. Lastly, when used for modeling and preproduction, the costs of filaments consumed during the development process may also be recovered.
Whether it is used for creating and testing prototypes or for final production, 3D printing is a great indicator that R&D Credit eligible activities are taking place. Companies implementing this technology at any point should consider taking advantage of R&D Tax Credits.
Conclusion
Japan is a land of ancient wisdom and modern technology. Striking that balance in today’s world can be difficult. With the help of 3D printing, Japan can maintain its stance as the global leader in robotic automation.