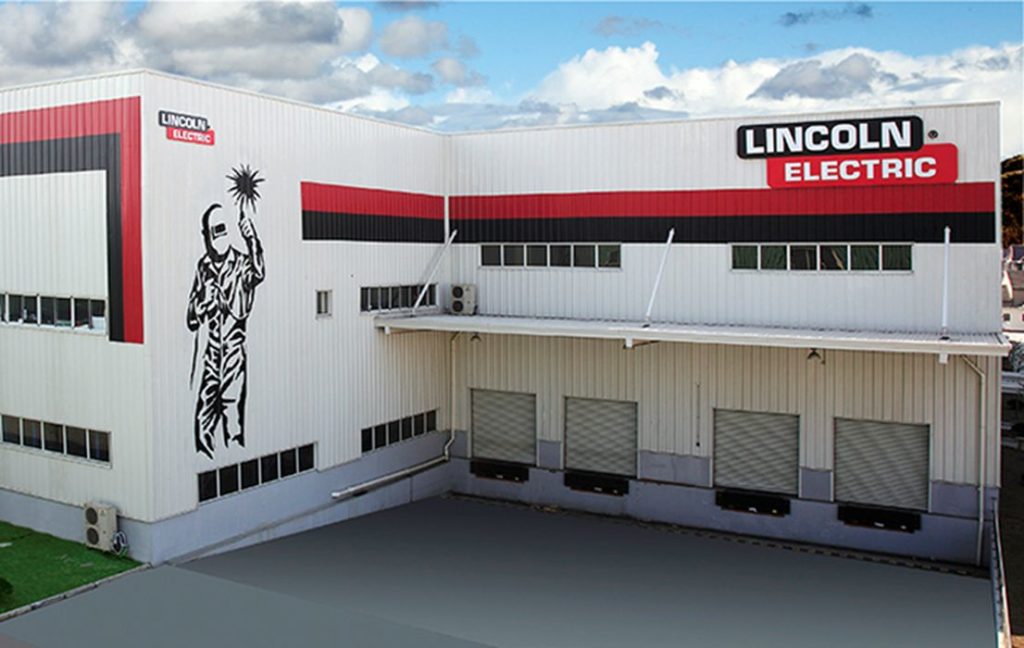
Charles R. Goulding and Ryan Donley examine how a welding company has adopted 3D printing technology.
Started in 1895, Cleveland, Ohio-based Lincoln Electric (Lincoln) is the world’s largest welding and welding supplies company with 2021 sales of US$3.2B. A company doesn’t last over 125 years without being innovative, and Lincoln has developed a separate additive business segment. Lincoln made its commitment to 3D printing clear when it bought Baker Industries in 2019. The combination of welding and 3D printing makes Lincoln a key player for automation projects in metal fabrication including but not limited to the automotive, aerospace and oil and gas industry.
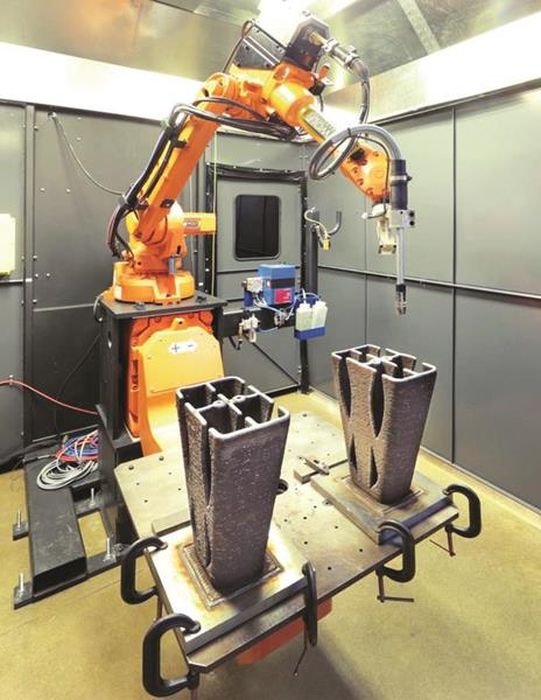
Lincoln delivers unique CAD and Path Planning with their large format wire-based metal additive manufacturing to take on complex projects, large or small. The additive solutions encompass a wide range of materials from steel, stainless steel, invar, nickel alloys, and nickel-aluminum bronze where Lincoln can develop functional large-form metal part prototypes as well as quick replacement parts. Through additive manufacturing, Lincoln seeks unique designs that can reduce weight, increase strength, combine materials, and merge additive and subtractive processes to provide unique part functionality features not seen with traditional manufacturing processes.
The past several years, Lincoln has been investing significantly in 3D printing as well as research and development expenses as shown in the table below:
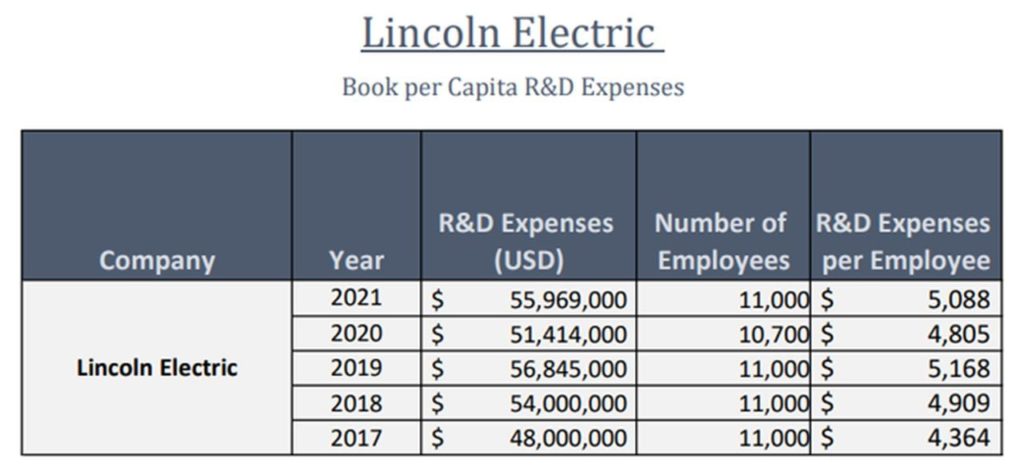
3D printing ability has become a powerful asset across many industries. Companies such as Lincoln that are integrating and utilizing 3D printing for product development including prototyping and testing should consider the Research and Development (R&D) Tax Credit. Wages for technical employees engaged in these activities are the largest drivers of eligible R&D Tax Credit expenses.
The Research & Development Tax Credit
The now permanent Research and Development Tax Credit is available for companies developing new or improved products, processes and/or software.
3D printing can help boost a company’s R&D Tax Credits. Wages for technical employees creating, testing, and revising 3D printed prototypes can be included as a percentage of eligible time spent for the R&D Tax Credit. Similarly, when used as a method of improving a process, time spent integrating 3D printing hardware and software counts as an eligible activity. Lastly, when used for modeling and preproduction, the costs of filaments consumed during the development process may also be recovered.
Whether it is used for creating and testing prototypes or for final production, 3D printing is a great indicator that R&D Credit eligible activities are taking place. Companies implementing this technology at any point should consider taking advantage of R&D Tax Credits.
Conclusion
When an industry’s largest player partners with a leading 3D printing provider the combination is powerful. Lincoln should be well positioned for the ongoing increase in automation and on-shoring U.S. manufacturing.