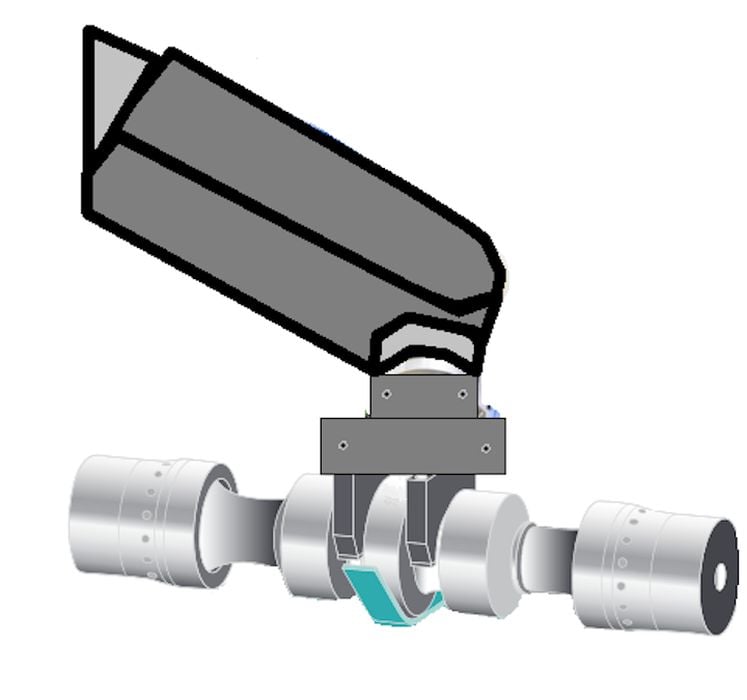
Another company announced intentions to produce a space-based 3D printer: Fabrisonic.
You may not have heard of Fabrisonic, as they use a highly unusual 3D printing process known as UAM ā or Ultrasonic Additive Manufacturing.
UAM involves vibrating adjacent materials at an ultrasonic frequency. This vibration eventually causes the molecules to bond together. This ultrasonic welding occurs because the oxides that normally coat the surfaces of metals are abraded away, allowing the metal molecules to contact and bond.
To 3D print with UAM thin sheets of metal are placed together and the toolhead is swept along them to create the bonding. The unusual process even allows bonding of unlike materials. Iāve personally held parts in my hand made from both copper and aluminum made by Fabrisonic.
The process is quite unusual in that it doesnāt involve any heat, unlike most other metal 3D printing processes. It also consumes little energy because thereās no need for heat generation.
Their system is usually mounted on a CNC platform, where cartesian movements take the ultrasonic toolhead over the materials. That technique was used on a project Fabrisonic undertook with NASA a few years ago.
The project was successful, but apparently it has led to further cooperation with the space agency.
Fabrisonic announced theyāre partnering with TGV Rockets on a NASA SBIR project to adapt UAM technology for use in the vacuum of space.
Fabrisonic CEO Mark Norfolk wrote:
āThe most obvious reason for welding or 3D printing in space is for repair. There are currently 27,000 pieces of space debris in orbit that are large enough to be tracked. Moving at 17,000+ miles per hour, any one of these can lance a hole in space structures. Even tiny flecks of paint are known to cause serious damage on impact. A small piece of debris can puncture a hole in a spacecraft. Immediate repair techniques are needed to stabilize the situation and hopefully allow for the mission to continue.
Long term though, the real focus for welding and 3D printing in space is construction. Currently we build spacecraft mainly to support the loads experienced in launch. Once in space, most space craft experience almost no real structural loading. If engineers can figure out ways to manufacture in space, then our material efficiency can shoot to the stars. An additional benefit is that we can build far larger structures than will fit in launch vehicles. By launching raw materials and then welding in space, we can create the exact structures we need without having compromise designs just for launch.ā
Norfolk believes, and I agree, that UAM is actually quite a good candidate for space-based welding and construction. There are several reasons, such as the low power requirements and inherent vacuum capability, but also safety concern relief from the lack of heat in the UAM process.
Is that really a concern? Decades ago welding experiments in space almost caused a catastrophe. Wikipedia describes the action on Soyuz 6 by Soviet Cosmonauts:
āThe crew was made up of Shonin and Kubasov, who carried out experiments in space welding. They tested three methods: using an electron beam, a low-pressure plasma arc and a consumable electrode. While welding, Kubasov almost burned through the hull of the vehicle’s Living Compartment, which in the absence of spacesuits could have resulted in a catastrophic situation.ā
Yikes. Thatās sufficient reason to look very hard for low heat welding solutions.
Norfolk believes the best approach could be to place the UAM toolhead on a robotic arm system, which would provide tremendous freedom of movement and thus allow a wide variety of construction scenarios.
It should be noted that in space there is no gravity, and so the normal constraints of robotic arms donāt necessarily apply. Consider that the Canadarm on the International Space Station can be extended to 17.6m in length. Thatās a lot of reach for any 3D printer, implying that an object of width 35m could be attempted.
This is a very worthwhile experiment for Fabrisonic, as their last NASA project resulted in a new and popular product for the company. Should the space-based UAM system be developed, there could be a large market for the device in the future as nations move outward into our Solar System.
Via Fabrisonic