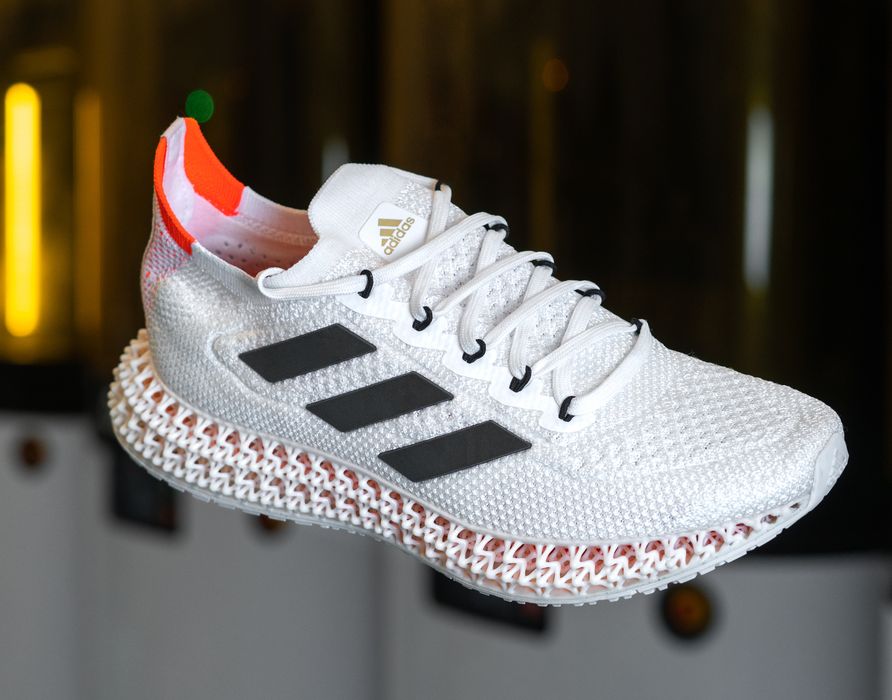
Adidas and Carbon announced a new collaboration to produce an updated 4DFWD shoe.
The two companies have long been working together on advanced athletic footwear, having first partnered on a 3D printed midsole back in 2017.
Back then the arrangement was essentially unprecedented: how could a mass market, end-use product be 3D printed? Why would a company even attempt such a thing?
The two companies realized it was possible to do, but only by fully leveraging the potential of 3D printing. To that end, the plan was to devise a complex midsole that provided unique function and would only be manufacturable with 3D printing.
The implication of that equation was the necessity for complex software: if a manufacturer required an unusual product, it would require a complex 3D model. That was, and still is for many companies, the root of the problem.
Carbon has worked diligently to create sophisticated software that can be used by manufacturers to generate the required complex 3D models, which of course would then be 3D printed on Carbon equipment.
In a way you can consider software to be the bridge between 3D printing technology and the advanced products weāre beginning to see in the 21st century. Thatās why Carbon has placed such a strong emphasis on their software development activities.
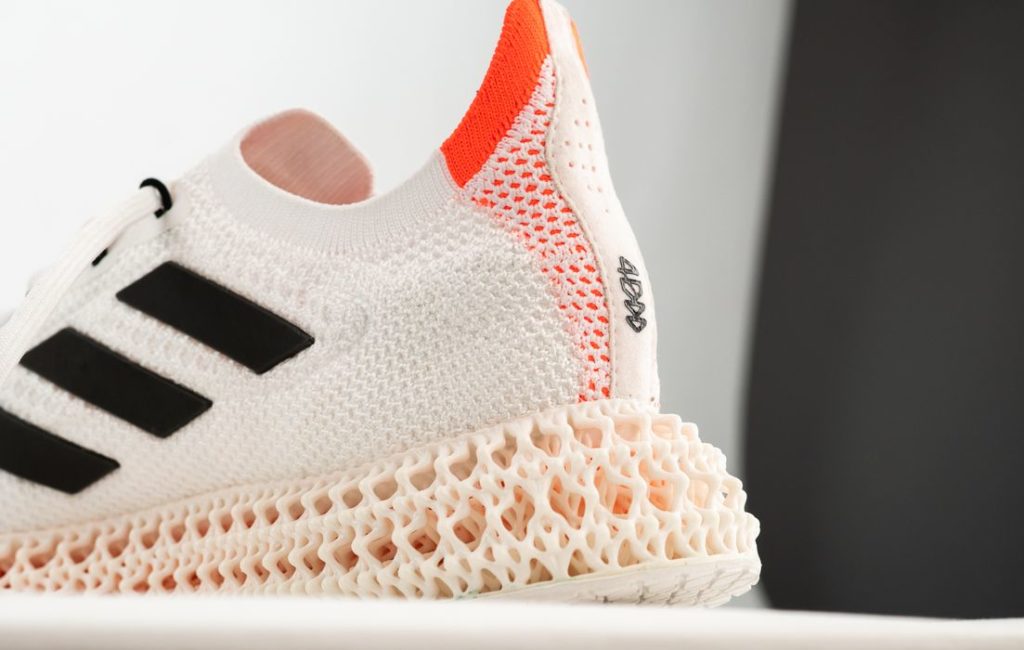
The latest iteration of the 4DFWD shoe by Adidas and Carbon involves both geometry and materials.
For geometry the shoeās new midsole design includes a tricky lattice design that provides a power boost to runners. Adidas explains:
āFor over four years, we have developed 4D lattice midsole technology in partnership with Carbon. Combining athlete data and Carbonās Digital Light Synthesis technology to produce precision tuned 3D printed midsoles. adidas 4D footwear is amongst the first in the world to use this cutting-edge technology which offers the ability to fine tune midsoles to specific patterns of movement, so that athletes can enjoy precision performance with every step.ā
And:
āAdidasās new lattice design incorporates a unique geometric element called, āFWD CELLā that transforms vertical pressure into forward motion.
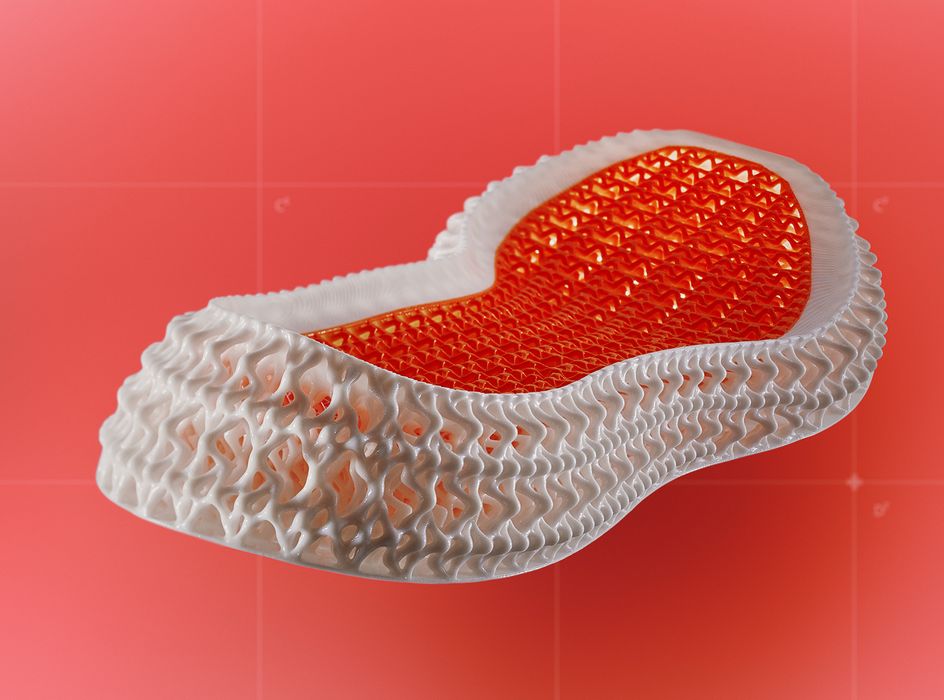
The development of the cell design apparently made use of 17 years of athlete data capture, combined with some five million potential cell designs. Like searching for a needle in a haystack, the optimal cell design was identified.
This is an animation of that cell design:
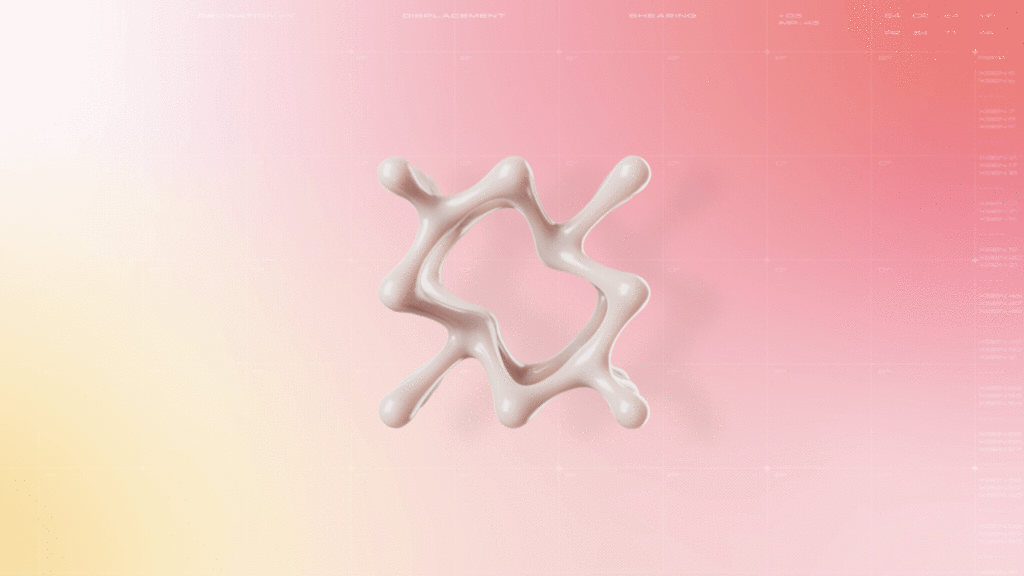
And this is an animation of how the cell works when under vertical pressure as the athlete presses their foot downwards:
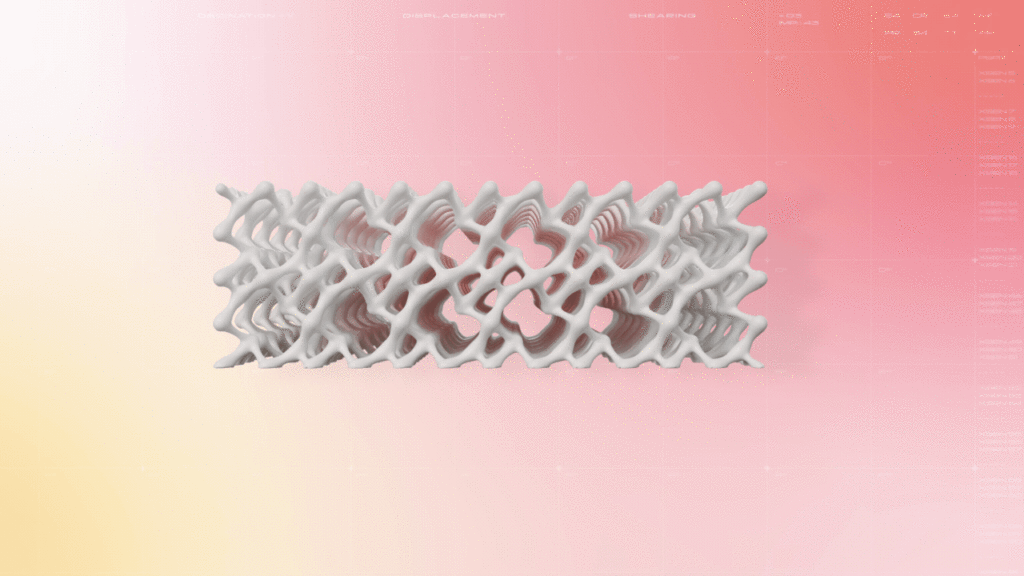
Notice that the entire structure shifts forward slightly. This movement is the transformation of vertical energy to horizontal energy through the ingenious cell design, and it provides a small boost to the runnerās performance.
The shoe has been used at the recent Olympics by multiple athletes, and is set to go on sale this week to the public. While earlier models of the shoe have occasionally been for sale by Adidas, this sale might be quite different.
Carbonās Chief Product and Business Development Officer, Philip DeSimone, apparently believes this could be the largest application of 3D printing ever produced. In other words, the most units 3D printed for a consumer product, as each midsole must be 3D printed individually.
If that is to happen, Adidas must have quite a farm of Carbon equipment in their factory somewhere.
While this is great news for Carbon and Adidas, I think it is also very good news for the industry in general. As complex 3D printed products become increasingly available, the public will gradually become more accustomed to seeing, buying and using advanced products. That can only lead towards more of the same, even in other industries.