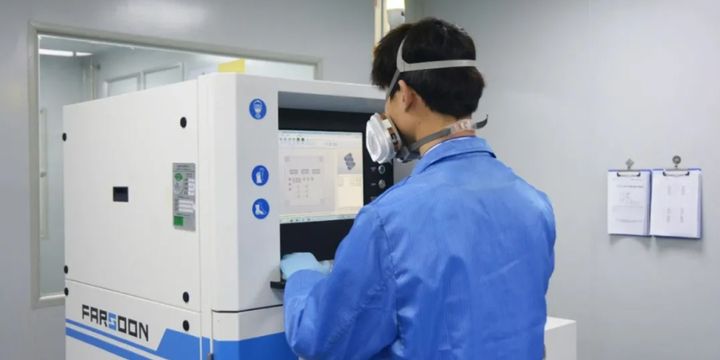
Farsoon’s metal 3D printers have been used to produce an officially approved medical implant in China.
Medical implants could be one of the best use cases for metal 3D printing: they require personalized designs and are in a market that is accustomed to high prices. Those are prime characteristics for additive manufacturing.
However, it’s not like you can simply design and 3D print implants if you happen to have the equipment. Instead you must receive approval from the appropriate regulatory authorities, and the process of doing so can be extremely challenging.
A long list of items must be verified by auditors to ensure the certification is valid. A great part of the certification is to ensure that with the same equipment, materials and process, parts of near-identical quality can be reliably produced.
For medical applications many aspects are considered. To give you an idea of the difficulties, one is to ensure that the completed parts are free from stray metal particles. For example, parts produced using the PBF process will be literally buried in fine metal powder. The parts must be extricated from the powder, and all the loose powder must be completely removed from every crevice on the part.
This is quite challenging given the highly complex 3D designs often used to produce medical implants.
Certified producers must be able to prove conclusively that they can do this, along with countless other steps.
But if they do so, they can obtain certification. And with that they will be able to officially produce medical implants.
The process is so arduous that few 3D print services have obtained authority to do so, and those that do can charge premium prices for their known-quality products.
Farsoon Medical Implants

Now I’ve learned that one of Farsoon’s clients, Huaxiang Group, a provider in China, has obtained category 3 medical device clearance from the Chinese authority, the National Medical Products Administration (NMPA), after performing no fewer than 108 tests across China. Huaxiang Group is now officially cleared to produce medical implants using Farsoon’s metal 3D printers and materials.
Their first product made under the new certification is a spinal fusion cage. This is a medical implant that is intended to be bolted around a couple of vertebrae in a patient’s spine. The cage stabilizes the two vertebrae, and ensures proper distancing if discs are deteriorating.
As you can see in these images, the design of the spinal fusion cage is quite intricate. Typical of advanced 3D printable designs, it minimizes use of materials while maintaining the required mechanical strengths.

Huaxiang Group has developed not only the design for this type of spinal fusion cage, but also a process for making them in larger batches. While each is customized to the patient, they can run a job on the Farsoon FS121M 3D printer to produce many in one operation.
Farsoon explains what might happen next:
“With the advanced capabilities of metal additive manufacturing, Dr. Wang’s team together with medical additive expert Huaxiang Group, are able to create a unique lattice design similar to the trabecular micro surface structure featuring customizable pore size, porosity and elastic modulus that are close to that of human bones. It helps to reduce the tension of stress, promote bone in growth rate and long-term stability. With substantial input from surgical design and metal 3D printing, unique geometries structures with fully customized anatomical endplates which feature curved angles and expanded contact surface topology are able to deliver the perfect anatomical match for a wide range of complex surgical conditions. The surgeons also benefit from significantly faster ‘on-demand’ development to production cycle for a high-quality, precise product by using Farsoon laser powder bed fusion systems, whereas the conventional multiple-use device usually takes months to manufacture.”
Clearly there are more products that could be made using the same process, and no doubt Huaxiang Group will be developing them.
While this is apparently the first such certification in China, it demonstrates that companies with similar Farsoon equipment and materials could potentially obtain analogous certifications in other regions.
With slowly-increasing numbers of certified providers, it seems that access to these advanced medical implants will also increase, bringing 3D print technology to many more people.
Via Farsoon