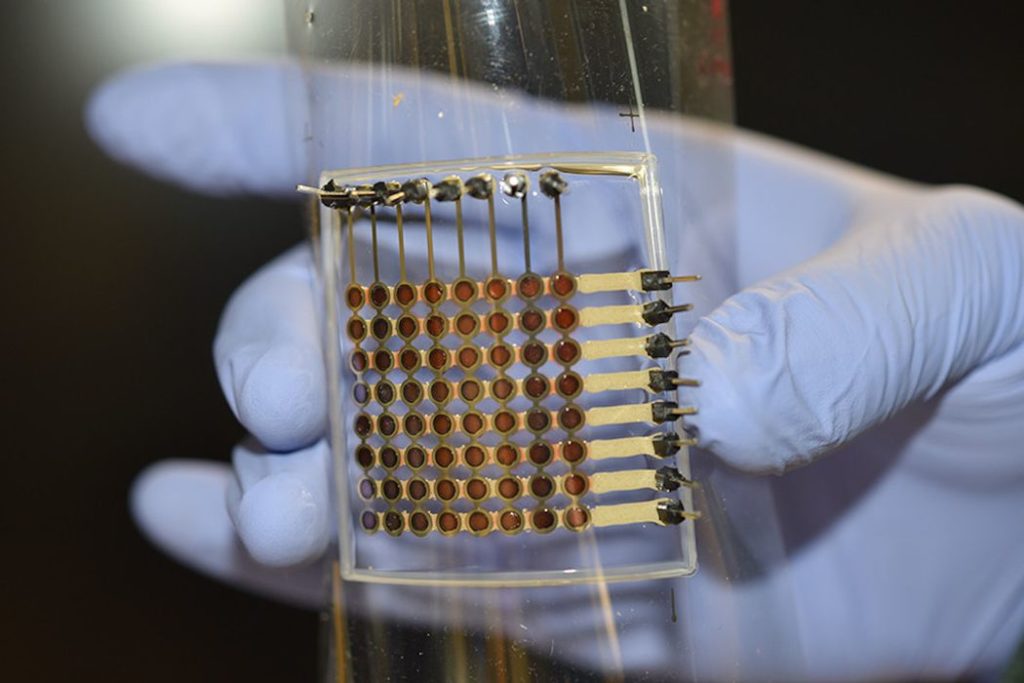
Researchers at the University of Minnesota have developed an unusual process to 3D print a prototype OLED display that’s actually flexible.
OLED display technology has been used in many smartphones and display monitors for the last few years. It differs from standard LCD panels in that instead of pixels selectively shading light from a background source, the pixels themselves emit light or do not, depending on their state. This allows OLED panels to provide extremely high contrast, as there is no light leakage.
Some electronics manufacturers have produced flexible OLED screens that have resulted in twistable displays, but now the University of Minnesota researchers have found a way to 3D print these structures.
It’s best to watch this video to see how it’s done in their multi-step process:
Note that there are several different materials being deposited throughout the process, and that the depositions take place on top of a flexible surface. After printing, the print surface flexes, providing the ability to mold the display for non-flat applications.
University of Minnesota Department of Mechanical Engineering’s Michael McAlpine, an author of the paper, explained the motivation to develop this technology:
“OLED displays are usually produced in big, expensive, ultra-clean fabrication facilities. We wanted to see if we could basically condense all of that down and print an OLED display on our table-top 3D printer, which was custom built and costs about the same as a Tesla Model S.”
As of this writing, a Model S would cost between US$88K all the way up to US$124K, so in other words, a bit more expensive than typical desktop 3D printers. However, far less than the cost of the standard fabrication plant for OLED panels.
The prototype OLED panel, as you can see in the video works reasonably well, but has terrible resolution. That’s because they’re demonstrating the technology, not developing a commercial product. This is a step necessary before commercialization could be contemplated.
Evidently the group’s next stage is to find ways to make the pixels shine more brightly, and to increase the resolution of the OLED array. Eventually it may be possible for the process to be used to produce commercially viable OLED panels.
The first commercial target would not be massive TVs or even smartphones, but more likely would be small utility panels to be affixed to structures or even wearable fashions where extreme resolution and color accuracy may not be as important.
It would seem feasible for this technology to be parallelized to the extreme. Imagine instead of a single printhead depositing material we had a line of deposition heads that operate in parallel. As the printhead sweeps across a deposition surface, tens or perhaps even hundreds of pixels could be built simultaneously. This approach could certainly speed up throughput on a future hypothetical OLED display 3D printer.
Another possibility for this technology is to incorporate it into existing 3D print technology. Imagine a device that can not only print a mechanical structure, but also electronics and OLED displays or lighting. That’s getting dangerously close to being able to 3D print completely functional electronic objects.