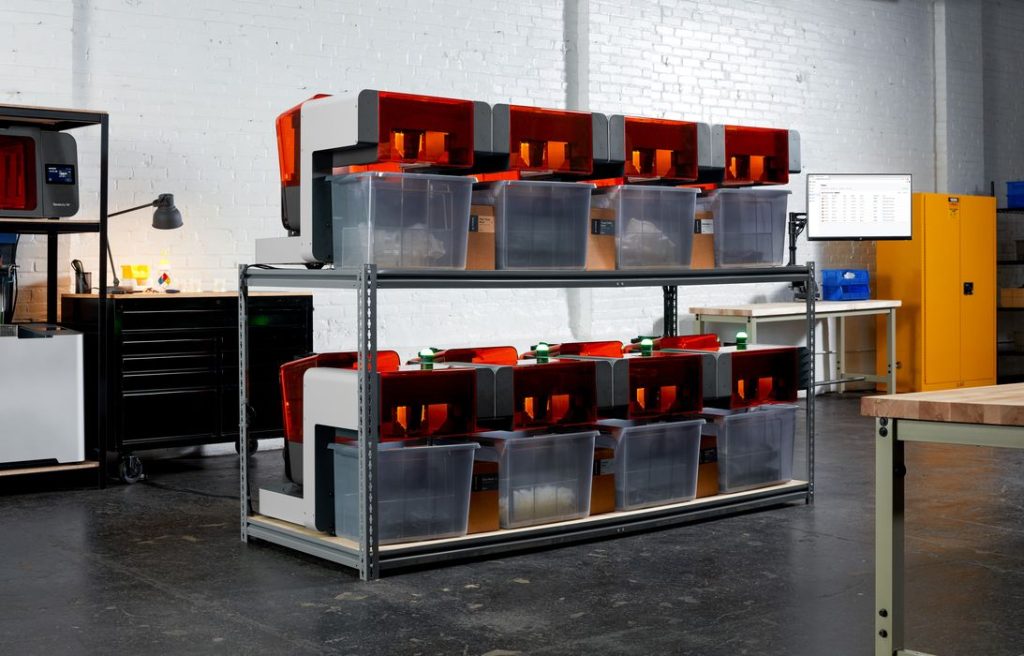
Formlabs today announced an automated manufacturing system that leverages their 3D print technology.
Formlabs began by developing a desktop 3D printer that used the SLA process to print high resolution objects. Over the years they’ve continued to refine this technology — and the associated materials — to result in today’s exceptional Form 3 system.
To use their resin systems, 3D printer operators must proceed through a bit of a workflow to obtain completed parts. Parts must be physically removed from the build plates, washed of loose resin, have support structures removed, and finally, cured to perfect solidity with UV light.
These steps require the use of accessory equipment, which Formlabs just happens to sell alongside the 3D printers themselves. But the point here is that it’s actually a lot of manual work required to move the parts between all these stations.
While single-machine owners might scoff at that effort, the picture changes when you have a workshop with, say, 100 Formlabs 3D printers. Then you’ll need a staff of operators that will be continually unloading parts and moving them between the printers and through the post processing steps.
That’s literally what happens today when a company uses an array of Form 3 machines to implement a production environment. These factories are limited by the manual effort involved. And worse, manual effort often means unpredictable and inconsistent results.

To solve this dilemma, Formlabs has been working on automation systems for a while. Back in 2017, for example, they announced the “Form Cell”, which was a kind of robotic system that would shuffle print plates in and out of the Form 2 machines of the day. But we haven’t heard much about that system since.
Today Formlabs announced what seems to be an evolution of the concept, and implemented with the more recent and powerful Form 3 systems.
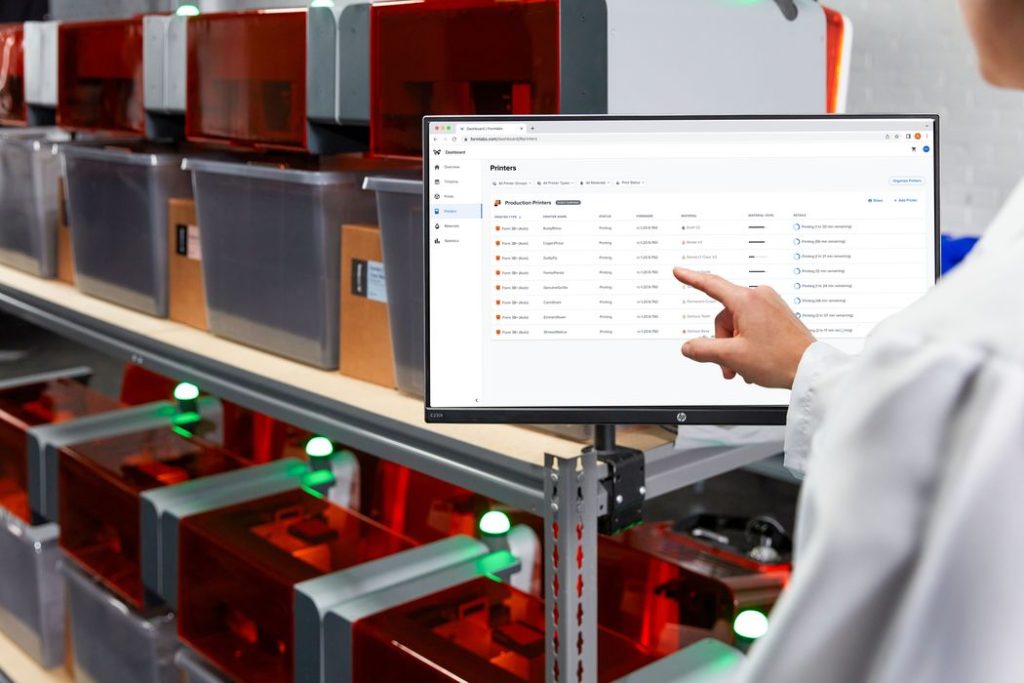
It’s called the “Automation Ecosystem”, and is comprised of several components, including:
- Form Auto: A hardware system that attaches to Form 3s and can automatically pull printed parts off the build plate. Apparently this mechanism makes use of Formlabs’ previous Quick Release print plate technology.
- Fleet Control: A software system that centralizes control of a fleet of Form 3 machines to efficiently dispatch jobs, which works from within the existing PreForm and Dashboard software.
- High Volume Resin: A new material capacity system that allows for cartridges of five liters, 5X more than the standard cartridges — and 5X fewer cartridge swaps. This should allow a printer to run for much longer durations, and significantly reduce materials packaging.
Here’s how it works:
The new ecosystem can be applied to existing Form 3 systems, and is a way for operations to very quickly scale up operations without the need to add new operations staff. In fact, it’s likely some workshops might have less need for operators.
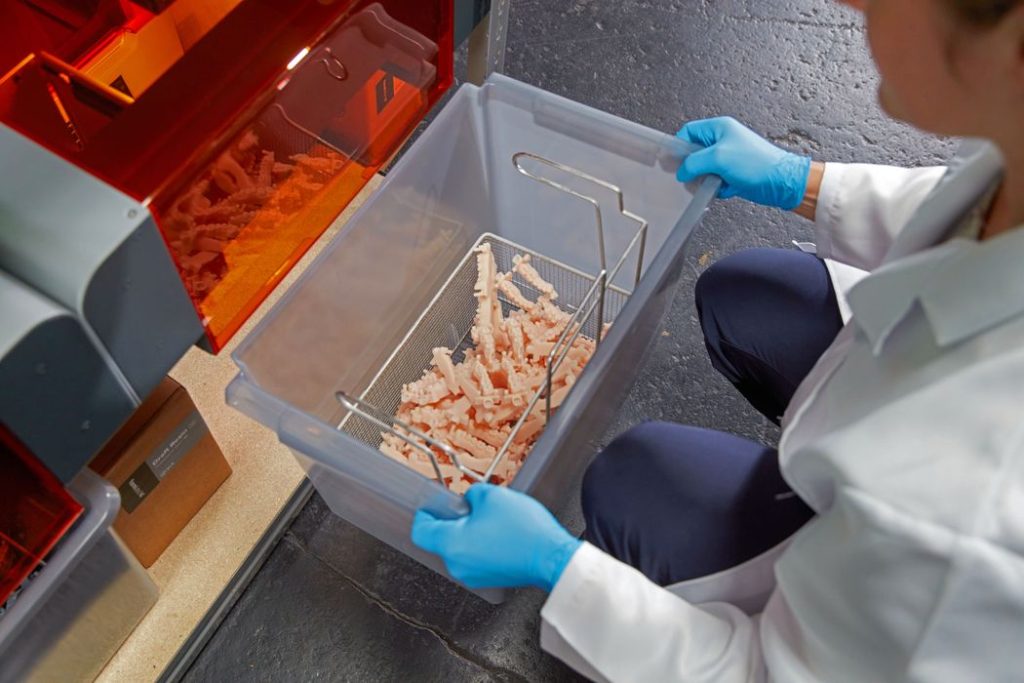
Unlike the Form Cell system that removed print plates, the new system works by automatically opening the lid of a printer that’s just finished a job, and then peeling off the completed prints. The print plate is not removed. These parts fall into bins where they can be collected en masse for movement to the next steps in post processing.
It seems that Formlabs has figured out an efficient way to unload 3D printers and get them instantly ready for succeeding jobs. That doesn’t quite automate the entire process, but it’s a huge step along the way, and perhaps the most difficult one.
Via Formlabs