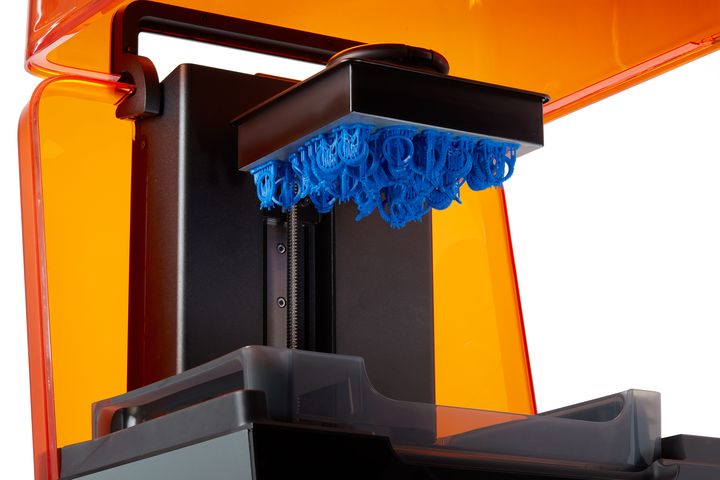
Formlabs announced a new castable resin today, marking yet another new material in their product catalog.
Castable Resin
The new resin is “Castable Wax 40”, which is intended for use by jewelers. Jewelers normally use the lost-wax process to produce jewelry. Here’s how that works: an object is sculpted in wax, and then surrounded with a plaster-like material. Then heat is applied, which melts the wax, leaving a perfectly formed void into which liquid metal is poured and cooled to a solid form.
For years now advanced jewelers have been using 3D printers in this same process, except that instead of sculpting the wax by hand they 3D print a wax object. The remainder of the lost wax process is the same.
But it’s not quite as simple as that. There’s no such thing as “3D printable wax”; instead it is a complex mix of materials that resemble the properties of actual wax. That’s because the resin must include photoinitators that cause solidification during 3D printing.
Those “extra” ingredients beyond just the wax make the process a little bit different for jewelers.
It now seems that Formlabs has spent considerable time working with jewelers to produce this new resin. They’ve tried to make the product as close as possible to true wax, explaining:
“With unmatched casting reliability, Castable Wax 40 Resin produces results similar to blue carving wax, the traditional material used in lost wax casting. They achieved this by developing a 40 percent wax-filled material that is capable of supporting traditional casting conditions. Castable Wax 40 Resin provides jewelers with greater versatility and design freedom than traditional processes all while digitizing their workflow to enable greater efficiency. Castable Wax 40 Resin provides extraordinary end results in a hybrid workflow such as lost wax casting.”
And:
“The latest material in Formlabs’ library, Castable Wax 40 Resin, demonstrates the company’s commitment to incorporating user feedback into the material development process. Formlabs worked with GIA, the world’s foremost authority on diamonds, colored stones, and pearls, and Rio Grande, one of the largest jewelry findings, tools, and equipment suppliers in the world, to develop the qualities of Castable Wax 40 Resin that make it ideally suited for end-use jewelry.”
This is clearly good news for jewelers operating Formlabs equipment, as the new resin can be directly used.
Formlabs Materials

What is perhaps even more interesting here is that Formlabs continues to develop in-house advanced resins for their clients. They say they’ve introduced more than a dozen specialized resins in recent months, and that’s quite interesting for a company that is supposedly a 3D printer manufacturer.
To be clear, a 3D printer doesn’t work without materials, and it makes sense to produce both. Here Formlabs is doing something a little different, however, by working directly with clients.
As anyone who’s used their slicing software, PreFrom, can attest, the company has a very strong focus on usability, and I think that’s what’s also happening with materials.
By working directly with users, they can compose resins that fit better into actual end-user workflows, making life a lot easier. Jewelers are not engineers; they simply want solutions that work best for them. And that includes both machine AND materials.
The usability will surely result in additional sales for Formlabs in the long run. I suspect the typical sequence of events will be a Formlabs jeweler explaining how easy the system is to use over beers at a jewelry conference, thus persuading their colleagues to buy Formlabs gear.
That is, if we had conferences.
Via Formlabs