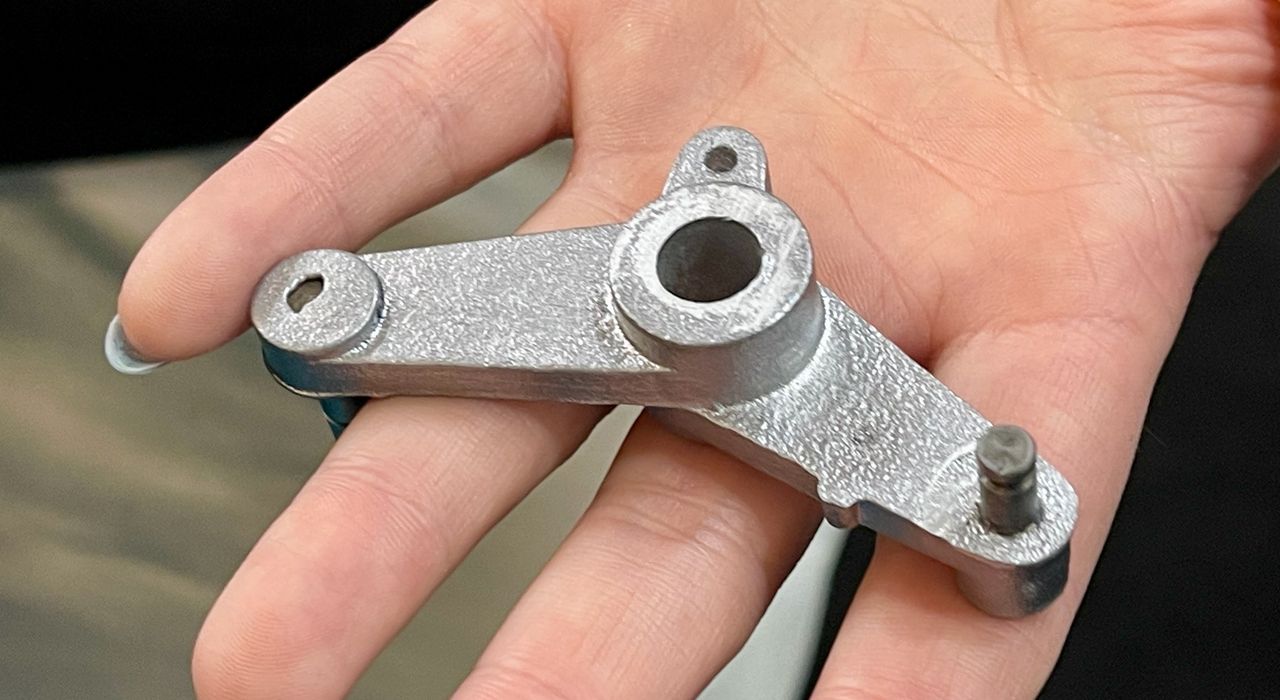
We spoke with Foundry Lab about their latest progress.
The New Zealand company offers a unique sort-of 3D printing process to quickly create metal objects. I say āsort ofā because they donāt actually 3D print the metal parts. Instead they have developed a digital casting process. It works like this:
- A design for a metal part is conceived and the corresponding mold is crafted, consisting of two separable halves.
- These molds are 3D printed utilizing a binder jet process with ceramic powder, resulting in what are called āgreenā parts.
- These green molds are then placed into a microwave device for curing. Though they are brittle post-cure, they can handle high temperatures.
- Designed to bolt together, these molds form a void inside that corresponds to the original part.
- After bolting, the mold is positioned upright with metal ingots placed on top where the sprue is expected.
- The entire assembly is put back into the microwave for a high-temperature treatment that melts the ingots. This molten metal then flows into the void via gravity.
- A vacuum aids in eliminating any trapped air bubbles.
- Post-melting, a gas is used to quench the mold, bringing it back to room temperature in a mere 30 minutes.
- Finally, the part is extracted from the mold, the sprue is trimmed, and voila! You have a fully solid metal part in as little as five hours.
Itās quite a different approach, and should be applicable to a variety of manufacturing operations. However, because itās a new process many will require persuasion to ensure their understanding ā and eventual sale.
To that end, Foundry Labs now operates a demonstration center in Fremont, California, where interested parties can drop by for live demonstrations of the digital casting process. Because the process is so rapid, itās almost possible to get parts while you wait.
I asked why Fremont, and was told that the American market is less conservative than the European market, and thus are more willing to adopt a strange, new technology.
Because of this the company is now selling products to early adopters. Thatās the right step at this stage in the companyās progress, but it will get tougher as they grow.
Foundry Lab related one customer scenario to us that they had recently serviced. The customer required a particular metal part and had been told it would take most of a year to build molds and cast the parts.
The company then consulted with Foundry Labs to determine if their digital casting process would be a better way forward. When given the 3D model for the metal part, Foundry Lab was able to produce five metal parts meeting the design in only one week. Thatās 50X faster turnaround time for this customer.
That customer was happy with the results, as you can well imagine. But this is the process that Foundry Lab will have to follow for future sales: a demonstration to prove the technology for the application, and then possibly a sale.
Demonstration centers work.
Via Foundry Lab