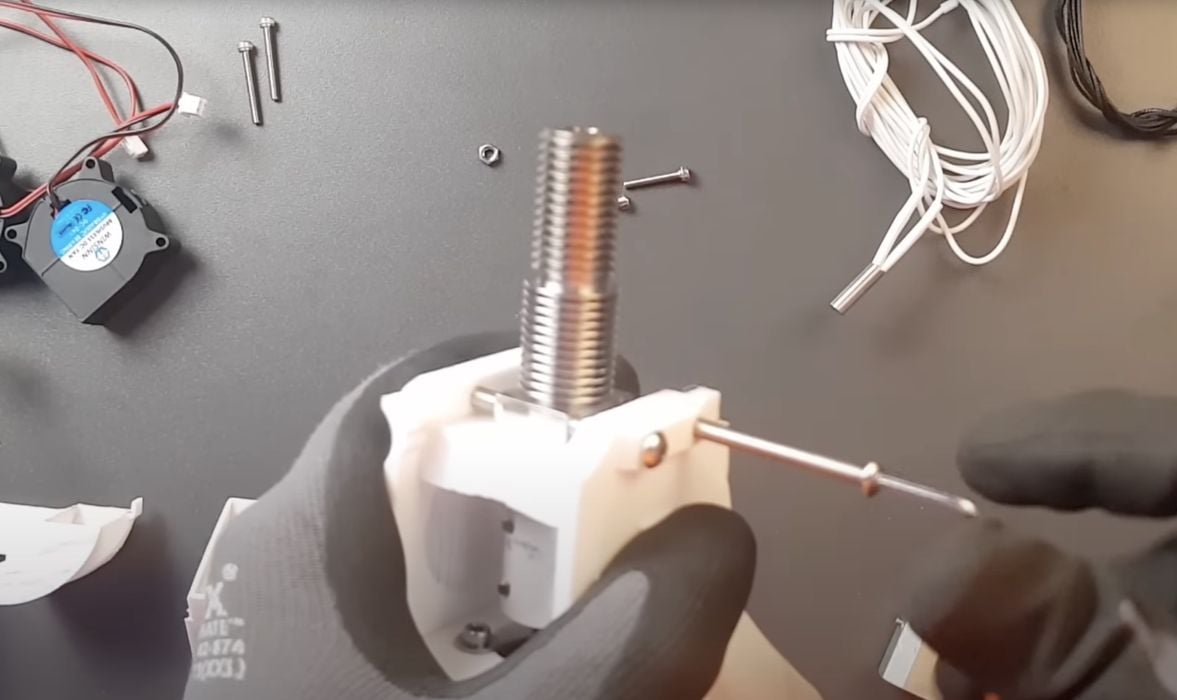
A 3D print enthusiast is developing a low-cost pellet toolhead replacement for FFF 3D printers.
Germany-based Kristian Friesen, a.k.a. āGreenBoy3Dā, is developing the low cost extruder replacement system.
Why do so? Itās all about cost.
FFF 3D printers by definition use filament as their input material. Filament is made by heating and extruding raw plastic pellets, much like a 3D printer toolhead does, except that the extrusion is wound up on a spool. Thereās a step required to make the filament between the pellets and printing.
That step, making the filament, adds cost to the process. Typically pellet plastic can be 4-10X less expensive than filament. This makes the printing of objects with FFF devices somewhat expensive.
If only you could use pellets directly on the FFF 3D printer instead to save costs. Thatās just not done. Iāve seen only one desktop pellet 3D printer: the PIOCREAT PRO FGF. (Note that
āFGFā means āFused Granular Fabricationā, as opposed to āFFFā, which stands for āFused Filament Fabricationā.)
Unfortunately this device lists for something over US$5,000, putting it out of the price range for many 3D printer operators. Other pellet 3D printers are far more expensive than the PIOCREAT.
There are many reasons for the cost difference, and a major one is the delivery of pellets. Typically these systems use air pumps to blow pellets through pipes towards the extrusion screw. That adds to the cost.
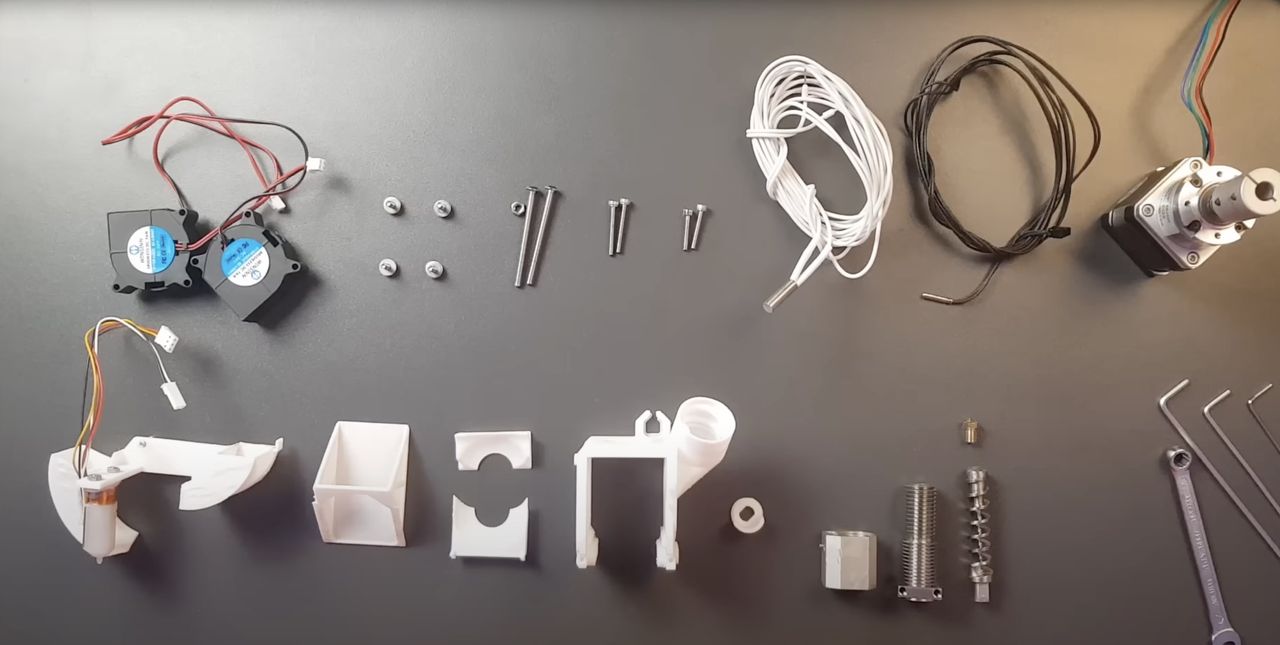
Here Friesen has developed through a couple of years of iteration a design for a pellet extruder. The design involves a gravity feed mechanism that eliminates most of the cost. However, it also reduces the amount of material that can be held at the printer: the commercial systems can have vast material capacities, even slurping pellets out of pallet-sized shipping boxes.
But thatās ok for small desktop 3D printers that donāt print large items.
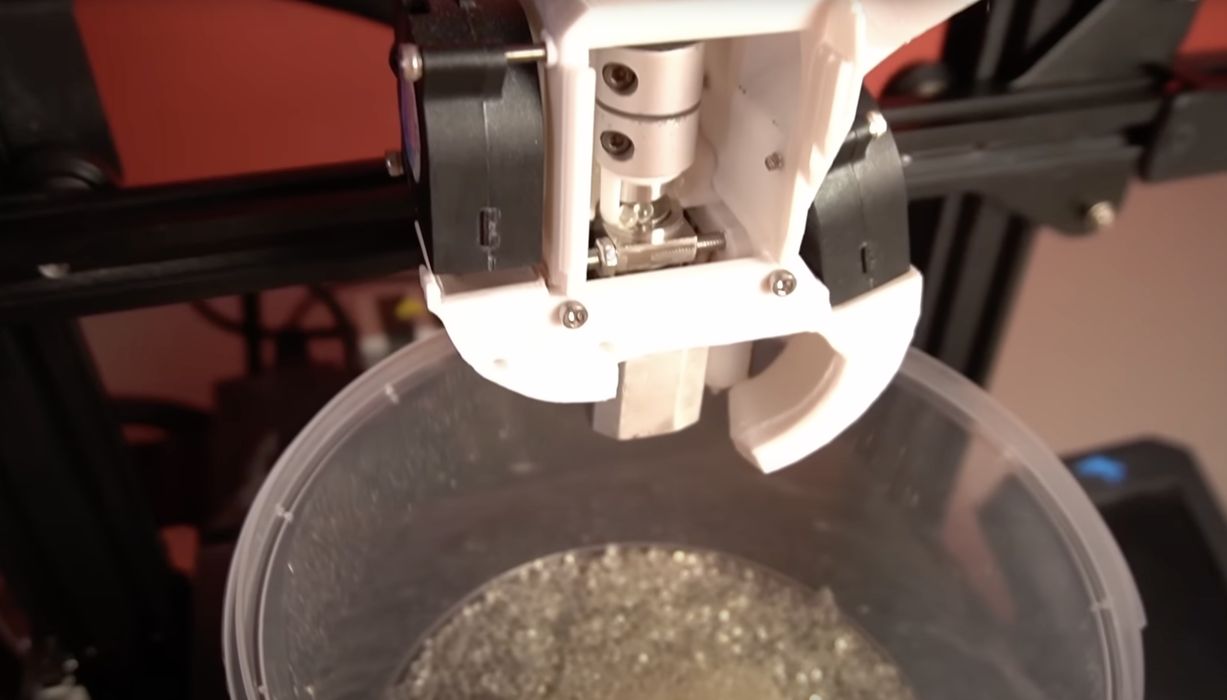
Friesenās design not only simplifies the pellet feeding, but also accounts for typical operational challenges. In particular, heās designed the system to allow for nearly instant material changes. The toolhead includes a kind of ātrap doorā to instantly release any current pellets in the system, allowing for a quick change.
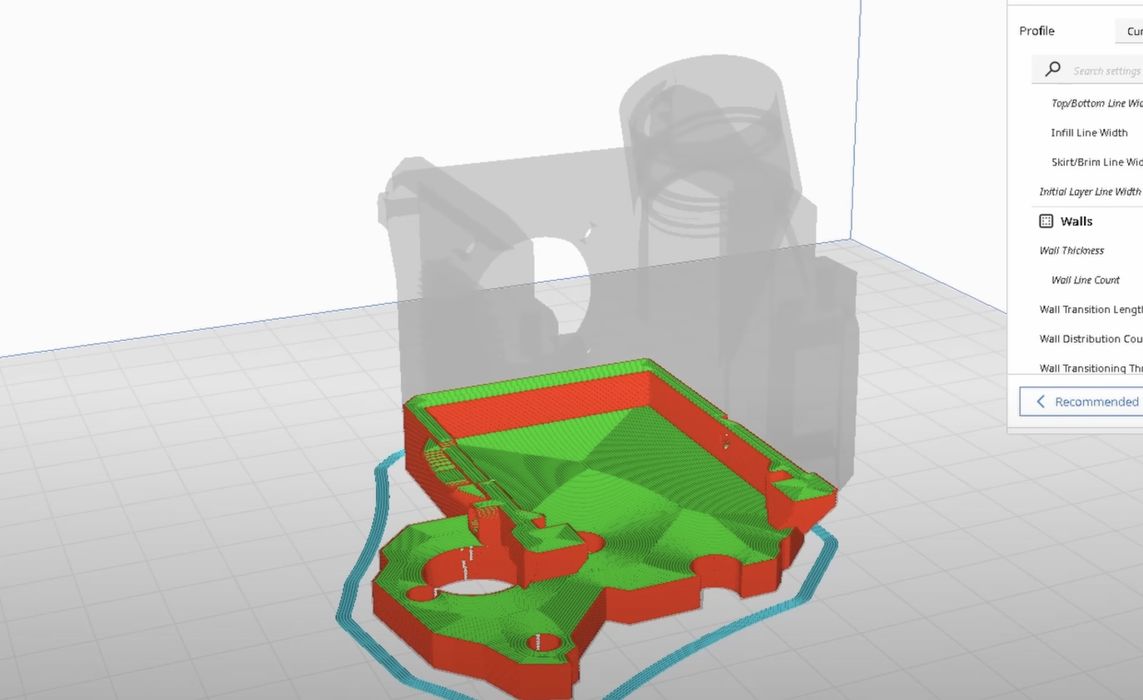
The extruder has been designed to be easily adapted for direct mounting on many common FFF 3D printer platforms. This suggests a conversion to a pellet system might be almost as easy as swapping in a new extruder, something thatās commonly done today.
At the moment Friesen is collecting feedback on the initial design so that it can be improved further before the official release. There is a survey form available here.
This is quite an intriguing project, as it could allow many people to almost immediately drop their costs to 3D print objects. However, to achieve the lowest costs one must buy pellets by the pallet, and thatās not something everyone can do. Nevertheless, smaller quantities of pellets will still beat filament pricing. They have to: filament is made from pellets!
Itās not clear when Friesen will release the GreenBoy3D Pellet Extruder, but it seems close. We are also unsure of the costs of the device, but many of the parts are 3D printable. However, the savings gained by using pellets could very likely pay for the upgrade.
Another interesting outcome from this project might be the proof that the industry could switch from filaments to pellets. That could be a major turning point for 3D printing, as lower costs would enable all sorts of new activity.
Finally, thereās the problem of waste 3D prints. If one had the pellet extruder installed, and a suitable grinder, it would be possible to recycle the plastic. Discarded prints, support structures and other trash could be ground up into small pellets that might be able to be processed by the pellet extruder. This would certainly save even more money for operators, and reduce plastic waste.
Via YouTube