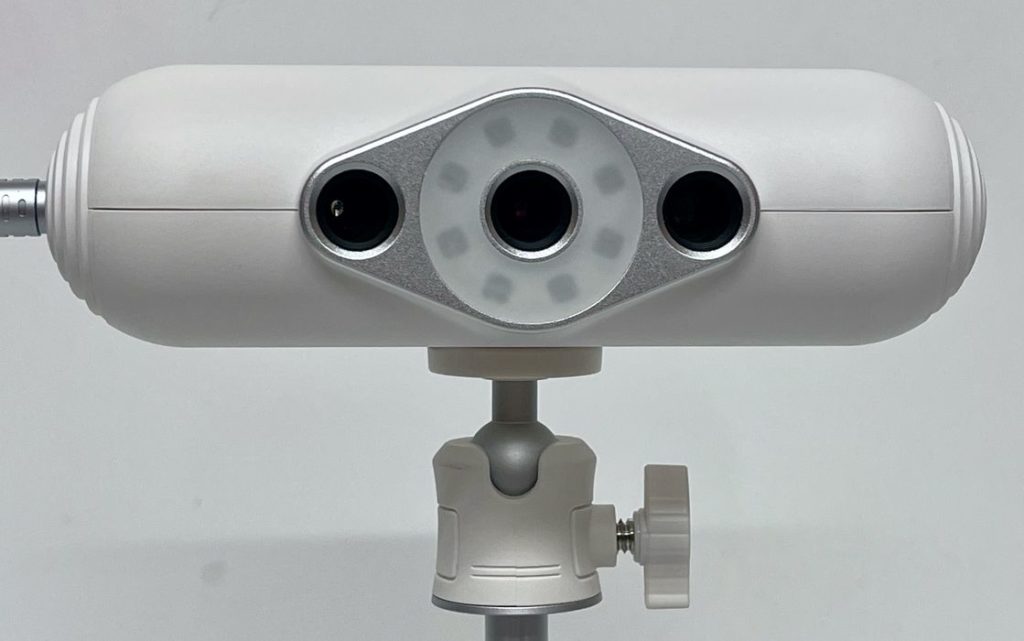
Our testing of the CR-Scan Lizard 3D scanning system from Creality continues with post-scan processing and our summary.
This is part three of a three part series. Please read parts one and two.
CR-Scan Lizard Processing

Processing scans is a critical feature of the CR-Scan Lizard system. Basically itās the process of converting from a captured point cloud to a usable 3D model. The software includes all the necessary functions to do this effectively, although it can be quite tricky to figure out how to use them, as described above.
No scanning system is perfect, and captured point clouds will certainly have a number of stray points. The best practice is to spend some time examining the captures and manually chopping out any obviously bad points that would otherwise confuse the processing algorithms. The software can easily do this, and even provide some editing after processing.
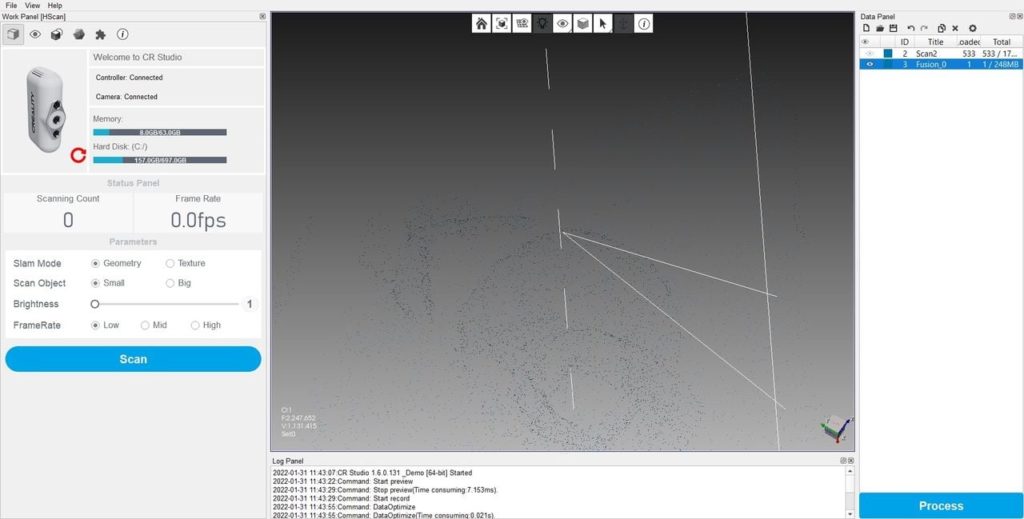
One very annoying limitation is that once a 3D model is created, you cannot spin it around in 3D view. Instead the 3D model disappears and is replaced by axis lines and a very faint outline. When you stop rotating the object reappears. This makes it extremely difficult to examine the 3D model properly and I have no idea why Crealityās software does this, since they can rotate point clouds easily and the PC routinely handles rotation of more complex 3D models in other software tools.
CR-Scan Lizard Advanced Operations
Processing is done on āscansā. Each scan operation is composed of a number of āframesā representing the infrared sensor array results at each moment. A project is usually composed of several scans because most objects are larger than the rather small scanning area in turntable mode and several scan views are required. These must be joined together in the software to complete the 3D model.
A typical operation on the turntable would involve multiple scans: at different heights to capture the entire object; and with the object turned upside down or sideways to capture the bottom.
This leads us to the advanced operation of joining models together, something CR Studio calls a āFusionā. This is the process of joining two or more scans together, and allows different scanner views of the same object to contribute to the 3D model.
The process is relatively straightforward, but tricky.
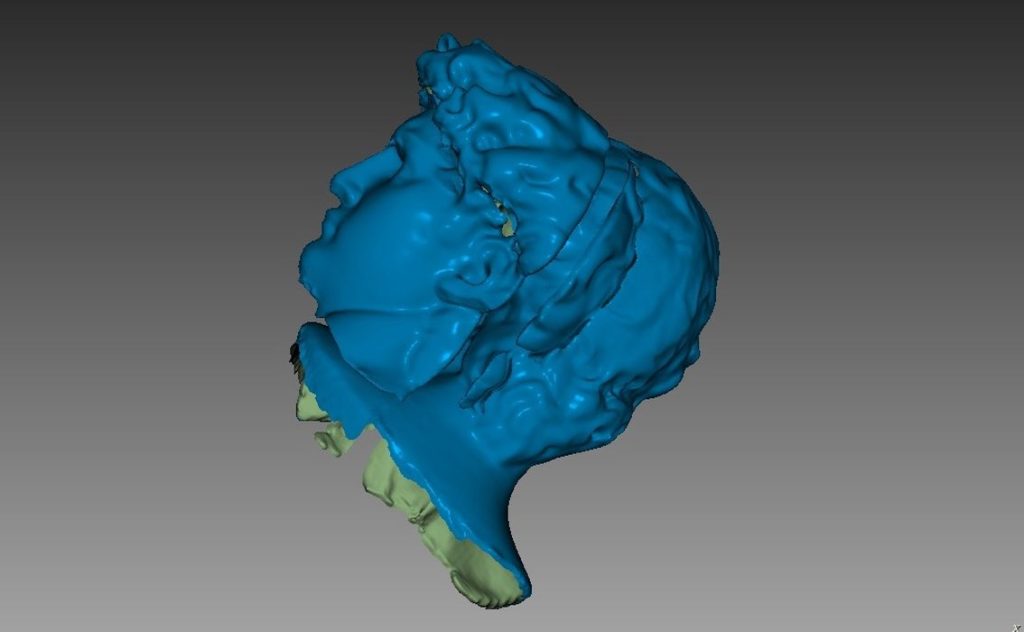
First, there is an automated mode where the software makes a guess as to how to fit the pieces together. This, in my experience, almost never worked properly. I recommend just using the manual alignment procedure.
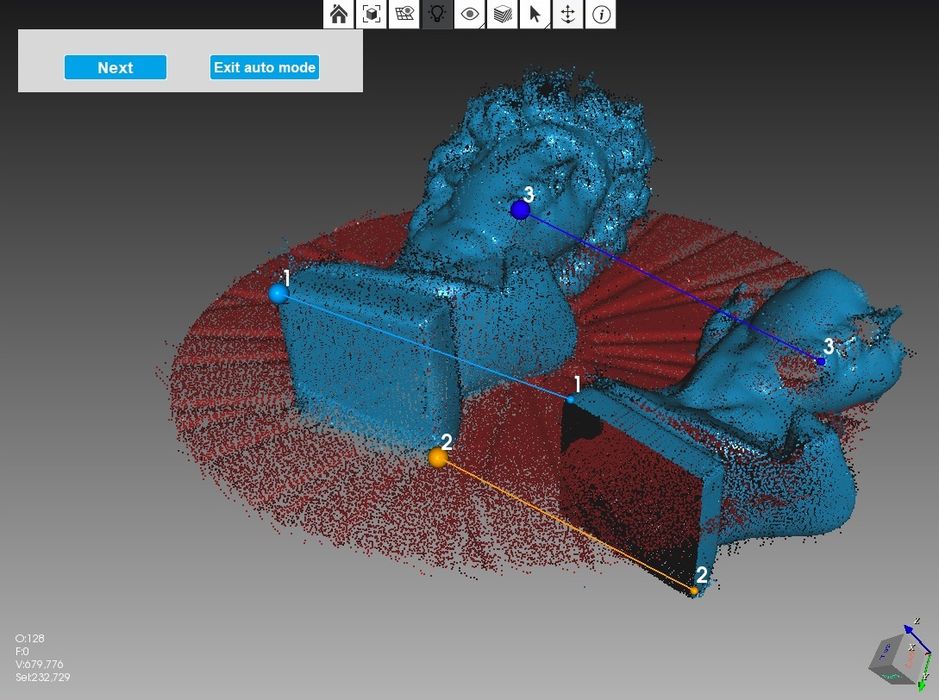
To manually align two captures you must identify at least three spots that appear on both of the captures. For example, scanning a human bust sculpture might have the tip of the nose visible in both. These point pairs are identified manually on each scan and provide the software with good info on where to start the alignment. After this is done the alignment process can begin. By repeating this process with several scans you can build up a pretty decent 3D model of all sides of the subject.
It is possible to obtain color 3D models by selecting the texture option during scanning. Basically the scanner captures a color image every once in a while during the scan and these are imprinted during a texturing phase of processing. This can take considerable processing time, so use this only if necessary.
CR-Scan Lizard Results
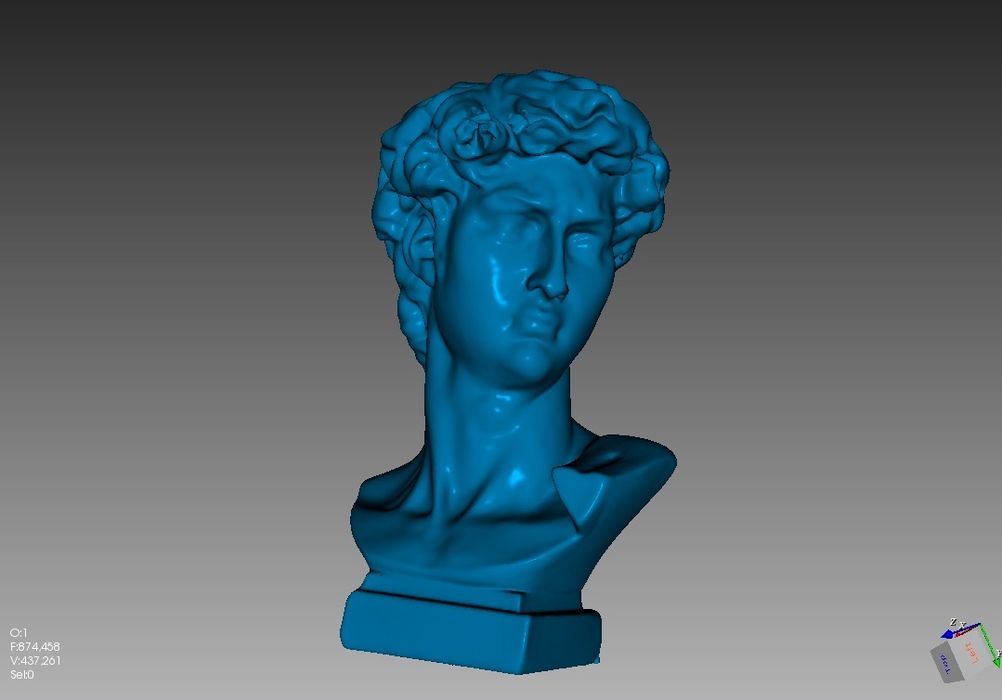
Despite the frustrations of using the sometimes incomprehensible CR Studio software, you can obtain very good scan results with the CR-Scan Lizard.
Surfaces are usually properly captured, with minimal noise. Although I did not perform any specific measurement tests, it appears the scans can be fairly accurate.
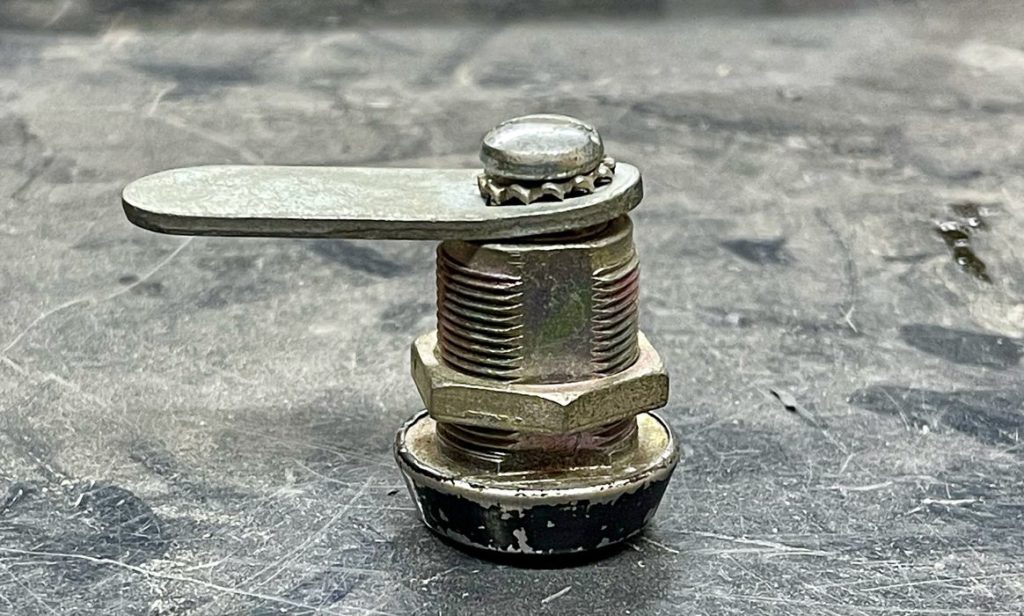
I did have some issues scanning metal parts that had a bit of a shine on their surface. Here you can see a small metal part I attempted to scan, and the result below. For objects like this, itās best to coat them with a dulling agent. This can be done with any of several sprays designed for 3D scanning.
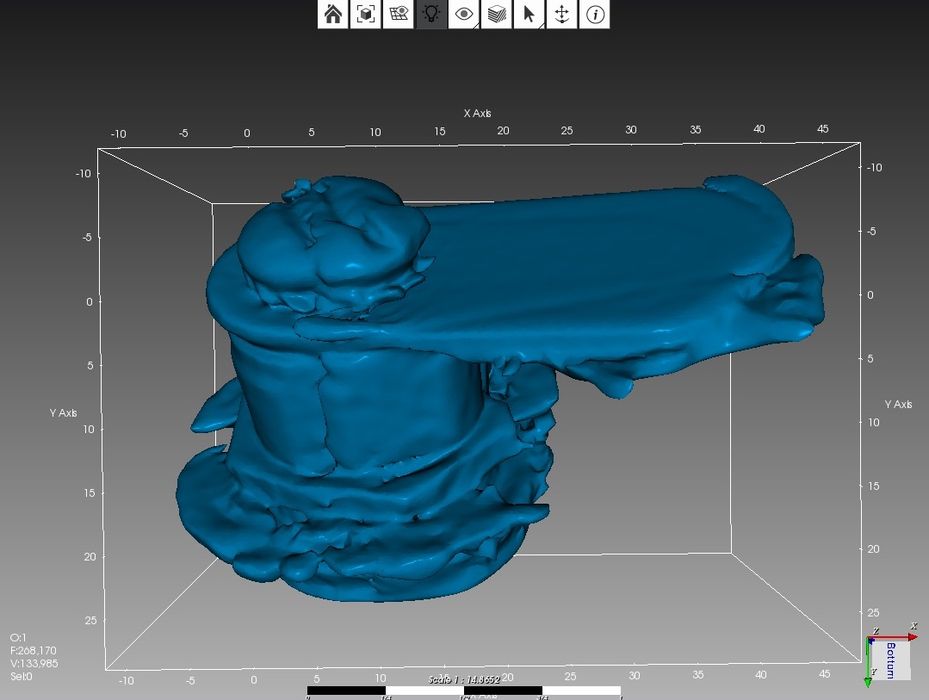
Once the software is tamed it does indeed produce very good 3D models, and if youāve filled the inevitable holes you can proceed to 3D printing.
CR-Scan Lizard Pricing and Availability
The CR-Scan Lizard scanning system is now available through a Kickstarter campaign. Creality offers quite a number of product combinations, but as of this writing the lowest combo cost for a working system is only US$329, which has to be about the lowest price for a decent 3D scanner Iāve yet seen. Even the final MSRP of US$599 is still a very good price, given that other commercial scanners can cost many thousands. Creality expects to ship units some time in April, only a few weeks away.
The system also comes with a one year warranty, something few hardware items come with in this space.
CR-Scan Lizard Final Words
I am very impressed with the Creality CR-Scan Lizard hardware. It is definitely capable of capturing high quality 3D scans, albeit with a rather narrow field of view, thus requiring additional scans and processing.
The accompanying software is very challenging to use, not because it doesnāt work, but because it is very difficult to figure out how to do many operations. My hope is that Creality spends additional effort to make their software far more usable, particularly for those who have never used scanning software.
If you are up for a long period of ādiscoveryā with the software, you definitely can learn how to use it well and your scans will be effective. On the other hand if you have an impatient attitude, you may not have a good experience.
As of this writing, Creality has sold thousands of these devices, so it seems to be a big success already.
This is part three of a three part series. Please read parts one and two.
Via Kickstarter
I own a scan lizard How do you get your model in the right position for printing cant find any info anywhere