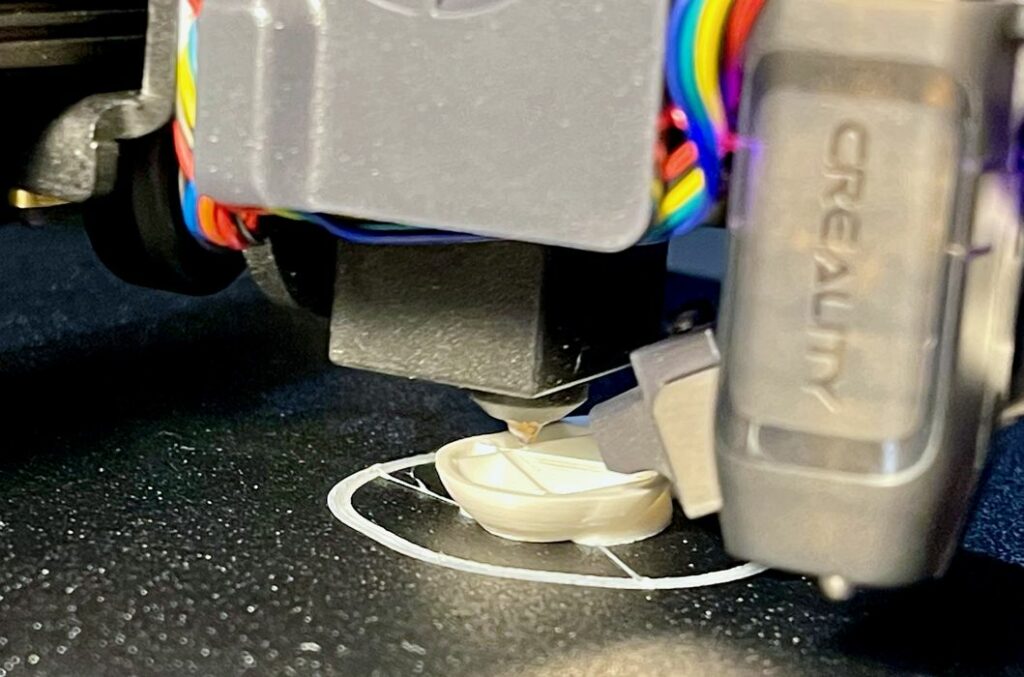
Among the most common questions asked is “how does a 3D printer work?”
The answer is actually quite complicated.
The complexity is because there are actually many kinds of 3D printers, and some are very different from each other. But all 3D printing processes have at least one thing in common: they are additive.
By “additive”, we mean the opposite of “subtractive”, which is the making method people are most familiar with: start with a chunk of material and carve, drill, saw, burn or otherwise remove (subtract) material to “reveal” the desired object.
On the other hand, “additive” is a process where you start with nothing and add material until you complete the desired object. The two approaches are entirely different. Subtractive technologies typically leave quite a bit of waste, while additive tends to use only the material required for the object itself.
With one notable exception (more on that later), 3D printing processes operate on a layer-by-layer fashion. A single layer is produced, then another on top of it. This process repeats until the object is complete. The differences between 3D printing processes are in how these layers are formed, as there are many unique ways to do so.
Some might say there are two kinds of 3D printing: filament and resin, but that’s very far from the truth. Those might be the two most popular materials, but in fact there are dozens of 3D printing processes.
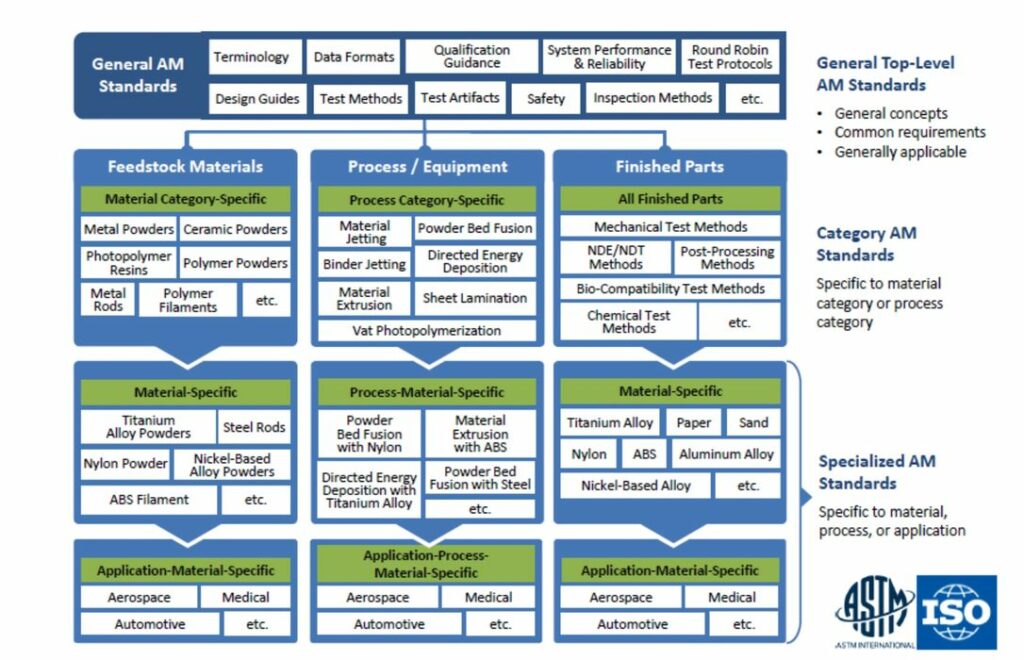
While that number is high — and ever increasing — virtually all of them fall into one of ISO’s seven definitions of 3D printing processes:
- Material jetting
- Powder bed fusion
- Binder jetting
- Directed energy deposition
- Material extrusion
- Sheet lamination
- Vat polymerization
You may read of different 3D printing processes from commercial providers, but the brand names of those processes almost always fall into one of the seven categories above. “MSLA”, for example, is a common method used by inexpensive resin 3D printers, but it’s really a variation of vat polymerization. Similarly, “FDM” is Stratasys’ brand name for their form of material extrusion.
But what, exactly are these seven methods? Let’s take a quick look.
Material Jetting
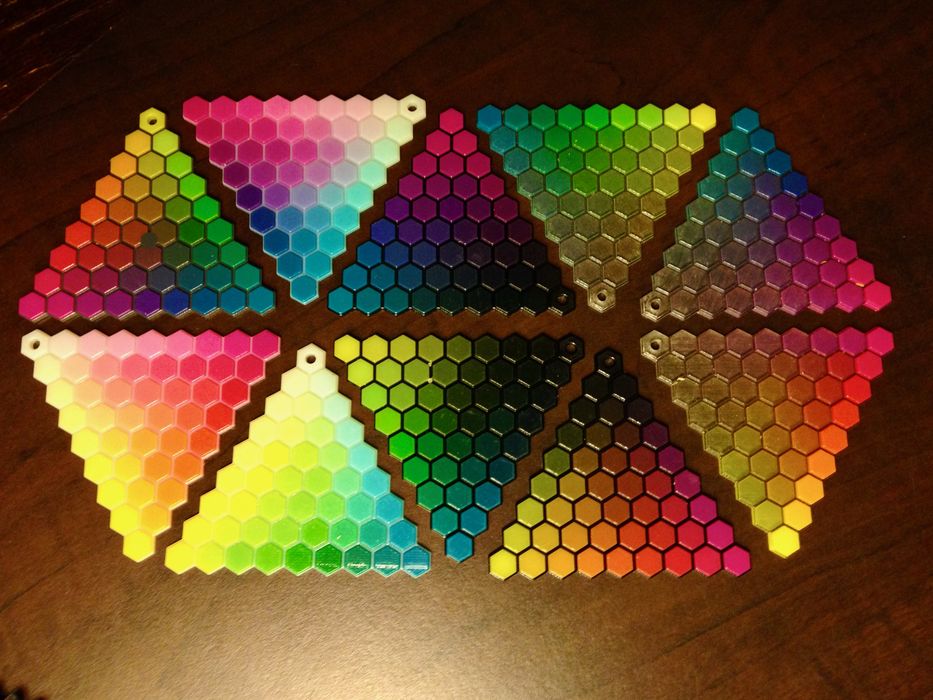
This process involves depositing tiny droplets of material on a build surface to form layers. Typically it’s done using high-resolution inkjet print heads that can deposit liquid material that can solidify, usually with an exposure of UV light.
Typical Materials: Polymers
Example Providers: Stratasys PolyJet
Powder Bed Fusion
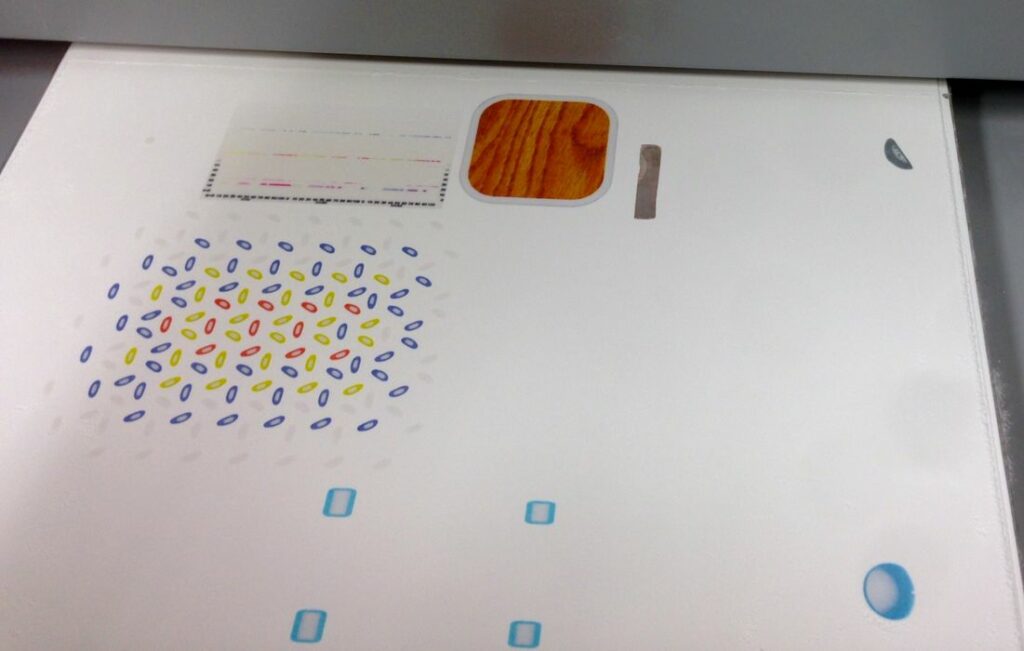
There are many forms of this process, where a thin and flat layer of loose powder is carefully lain down. Then an energy source, usually a laser, traces across the surface of the powder, fusing the particles together wherever it strikes. Subsequent layers of powder are applied and solidified until the object is complete — and buried in loose powder.
Typical Materials: Polymers, Metals, Ceramics
Example Providers: SLM Solutions, GE Additive, EOS, 3D Systems SLS, and many others
Binder Jetting
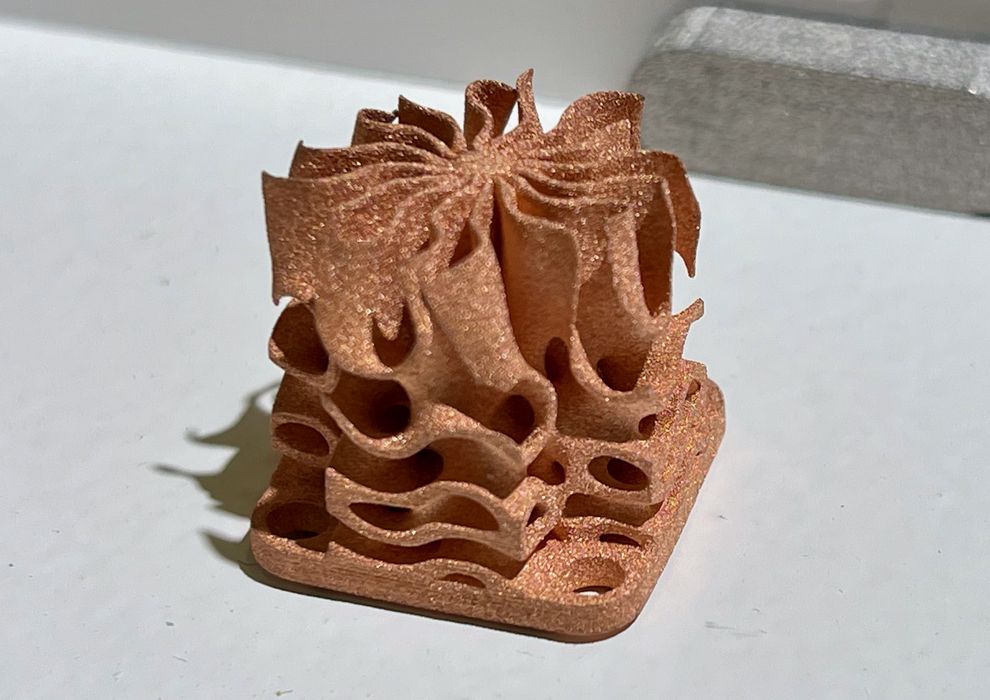
Binder jetting is a bit of a combination of powder bed fusion and material jetting. The material is really the powder, and what’s being jetted is “glue” that causes portions of each layer to fuse together. Again, this repeats with subsequent layers of powder and binder to complete the object. Note that many of these systems require post processing to finalize the object, perhaps through a heat treatment or sintering.
Typical Materials: Polymers, Metals, Ceramics
Example Providers: HP MJF, Digital Metal, XJET, several others
Directed Energy Deposition
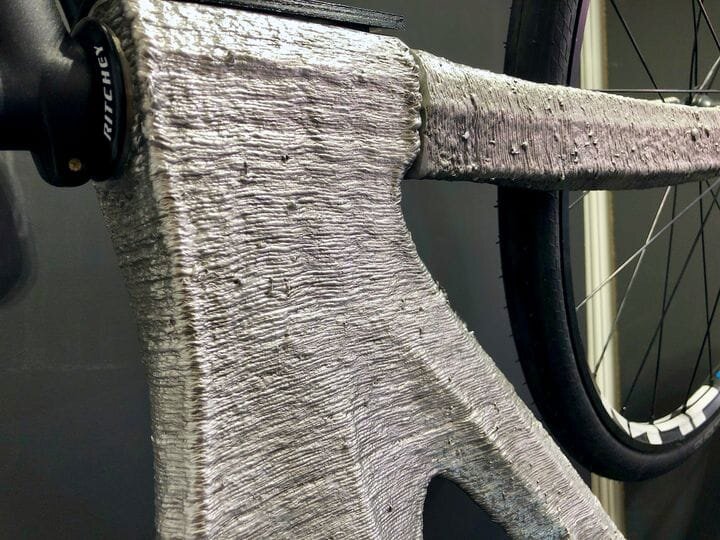
“DED” is a process where material is presented at a toolhead, and energy — usually a powerful laser or electrical arc — instantly melts the material, which fuses onto nearby structures. Often the material is a solid input wire, but sometimes it’s a powder. By moving the toolhead around in 3D space, it’s possible to build an object, and again this is most often done in horizontal layers.
Typical Materials: Metals
Example Providers: MX3D, AML3D, MELTIO, others
Material Extrusion
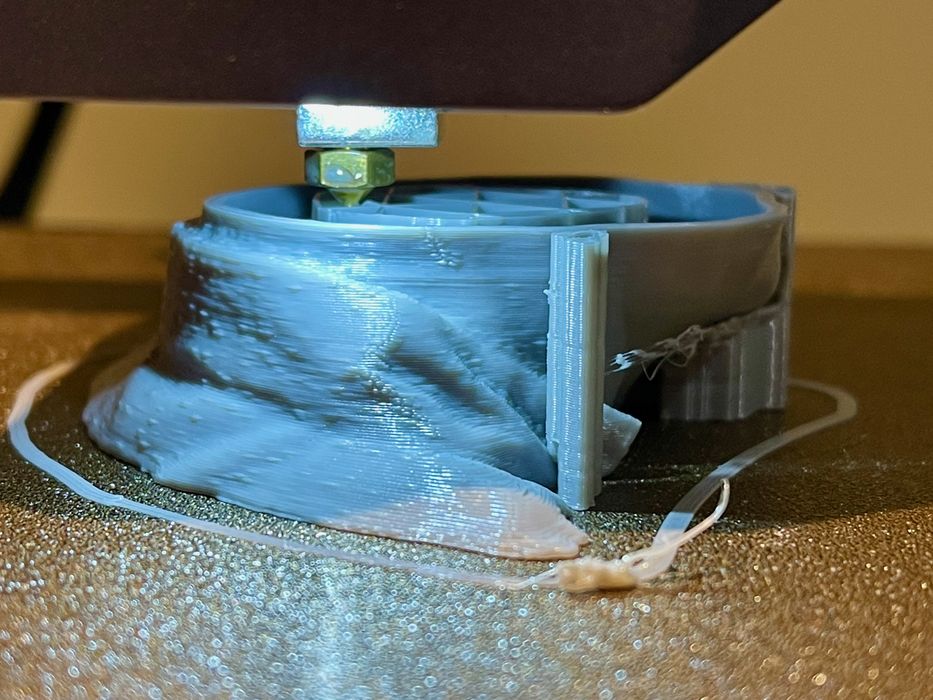
Filament 3D printing, or FFF, is this type, where a thermoplastic is softened by heat. It’s then pushed through a nozzle by a moving toolhead that traces the structure of the object. Layer by layer, the object is gradually built.
Typical Materials: Polymers, some metals if sintering is done after printing
Example Providers: Stratasys, Prusa Research, Creality, Anycubic, many others
Sheet Lamination
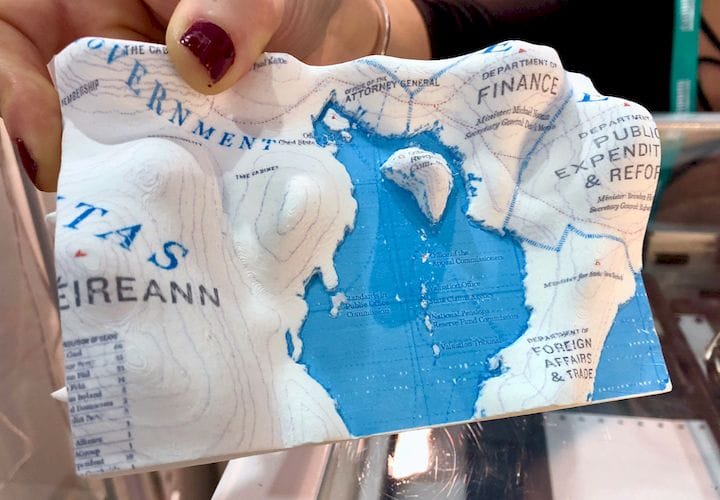
This is now a very rare form of 3D printing, and I’m not sure it’s particularly additive, as it requires subtractive steps. Basically, a sheet of material — polymer, paper or other substance — is laid down, and a blade cuts the outline of the layer. As these sheets are selectively glued down, the object is built. When complete, the portions outside the object’s perimeter are simply lifted away, as the cuts align vertically.
Typical Materials: Polymers, Paper
Example Providers: Solido (now defunct), MCOR (now defunct) and Clean Green 3D
Vat Polymerization
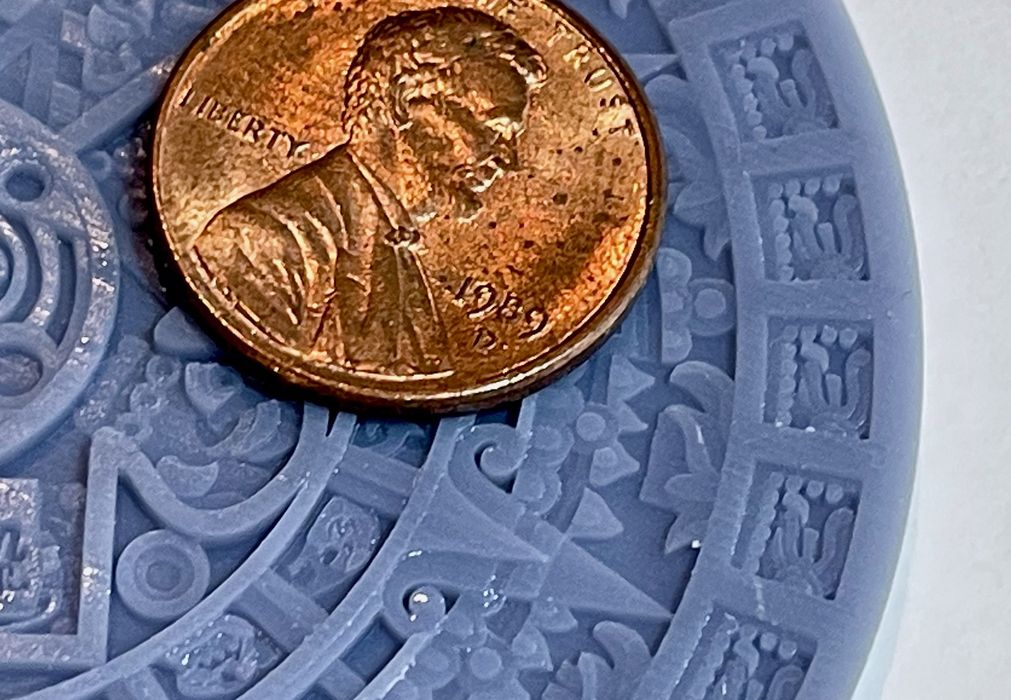
This is the second most popular approach, and it relies on the chemical properties of photopolymers. These are special molecules that bind together (or “polymerize”) when exposed to certain frequencies of light. The process involves a vat of photopolymer resin that is selectively exposed to this type of light, usually by a laser, DLP projector or masked light source. As each layer cures, fresh resin floods in to prepare for the next layer.
Typical Materials: Polymer and Ceramic Resins
Example Providers: 3D Systems SLA, Stratasys RPS, Anycubic, Phrozen, Creality, and many others
Which 3D Printing Process?
Each approach has advantages and disadvantages, sometimes quite dramatically so. The list of possible materials for use in each process is also quite restricted. For example, it’s next to impossible to make a practical metal photopolymer resin, so metal production is mostly limited to powder bed fusion, binder jetting and material extrusion systems.
The result is that we have an array of possible 3D print solutions, and usually there is one that’s best for each given job. It’s critical to select the correct process and material, otherwise the application could fail.
Unlike what many may assume, having “a 3D printer” doesn’t mean you can print anything. Workshops usually have several different kinds of 3D printers in order to cover as many bases as possible.
What all 3D printers do have in common is that they can all tackle incredibly complex objects. There are many geometries that are literally impossible to make using any other technology.
Consider injection molding: you can’t make an object with “parts inside”, because no mold could do that. But with any 3D printing process this is a straightforward approach.
Layer By Layer Only?
As mentioned above, most 3D printing processes are layer-by-layer affairs, which can indeed produce almost any geometry you can imagine.
However, that ability comes with a cost. While a injection mold can produce “all the layers” simultaneously, 3D printing processes must proceed through each and every layer to complete the object. This usually means that 3D printing processes are vastly slower than most traditional making methods.
Because of that slow speed, 3D printing is being slowly adopted by industry, which usually requires fast turnaround. Nevertheless, 3D printer manufacturers and researchers continue to identify ways to speed up the seven basic 3D printing processes listed above.
The Future — And Beyond
Building objects layer by layer can be extremely time consuming, and researchers have now identified a method of 3D printing that could be as much as 100X faster. The new approach is known as “volumetric” 3D printing, and is a variation of vat polymerization.
Volumetric 3D printing works by having a large, rotating vat of photopolymer resin, and a projector. The projector emits light patterns deep into the resin, and as the vat rotates, the patterns change. These patterns are essentially “X-Rays” of the intended object. As energy accumulates in certain areas frequently exposed to the light patterns, the resin solidifies. This essentially builds the object “all at once” instead of layer by layer.
As of now there are no commercial volumetric 3D printers on the market, but at least one is under development. It may be that in the near future we will see new devices emerge that can literally produce new objects in minutes or seconds.
Until then, you’ll have to make do with the many 3D printing processes of today.