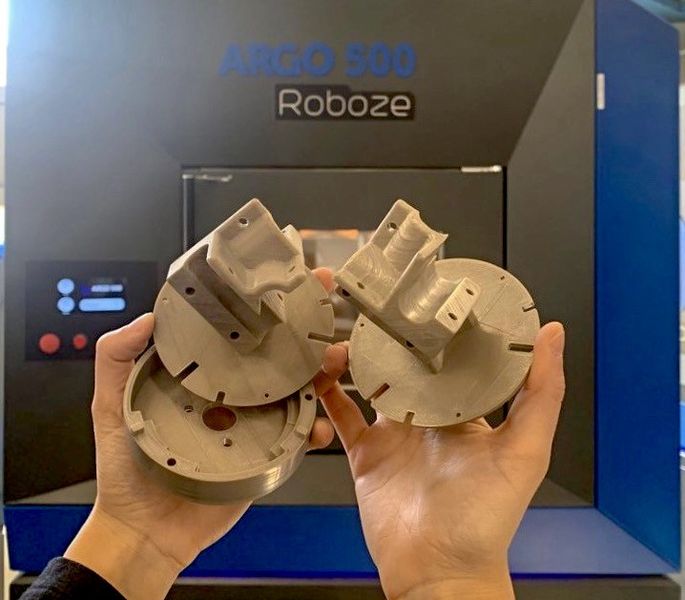
A partly 3D printed research satellite will test the envelope of 3D printed technology.
Roboze announced theyāve partnered with a team at the University of Colorado to develop an unusual 3D printed CubeSat. For those not familiar, a CubeSat is a āsmall format satelliteā design that fits within very strict dimensional and weight parameters. Often CubeSats piggyback on flights of larger satellites as they are so small and thus easy to include.
The CubeSat restrictions can be extremely challenging for satellite designers, as the game is to squeeze in as many components and functions as possible into the weight and size available. More functions means more value, but thatās at the cost of weight.
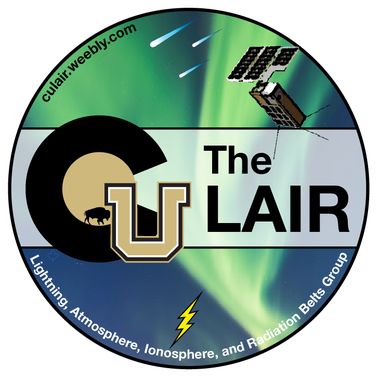
The work is being undertaken by the University of Colorado Boulderās Lightning, Atmosphere, Ionosphere, and Radiation Belt research group (also known as āThe LAIRā), which is part of the Aerospace Engineering Sciences (AES) department. Their research attempts to understand the electrical phenomena that surround the upper atmosphere of the Earth, including radiation, magnetic fields, and such, all the way down to common lightning storms.
By placing a 3U CubeSat far above the Earth they can look down and observe these phenomena to gather data for later analysis. The mission, called āCANVASā, was started a couple of years ago. CANVAS will detect how the magnetosphere is altered when lightning propagates energy into the upper atmosphere.
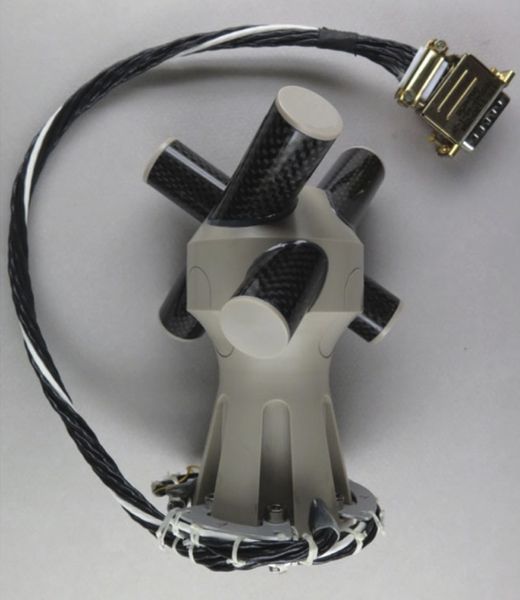
LAIR turned to Roboze to help produce some of the parts for the CANVAS mission. Roboze produces high-temperature 3D printers capable of making parts in unusual engineering materials.
One of those materials is PEEK, a polymer that has a very high heat resistance, great strength, and is quite lightweight, especially compared to metal alternatives.
While CubeSats are typically made from metal parts, it seems that LAIR realized they could substitute high-performance polymer parts for some metal parts in the CANVAS designs. This decreased the weight, but also allowed for more unusual 3D designs to be produced, which also saved physical space on CANVAS.
This is an excellent application for 3D printing, as it leverages the technologyās ability to produce unusual geometries and makes use of powerful engineering materials.
I am still amazed at how far this technology has come. Only ten years ago 3D printing was relegated to prototyping use only, largely due to the lousy selection of materials at the time. But in recent years this has completely changed. New materials have been released, and many more are coming, and each can potentially fill a niche for different applications.
Here we see a technology that could not have been conceived for use in a spacecraft years ago, yet itās being done by Roboze and the University of Colorado. When the CANVAS mission is launched in 2022, no one can say that 3D printing is only for prototyping: this project tests 3D printed parts in the most extreme environment.
Via Roboze