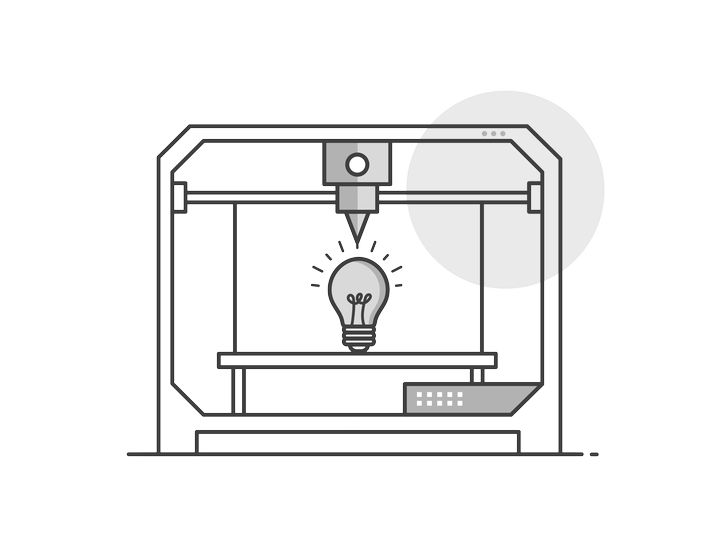
3D printing is prototyping. The two are inextricably linked. Another name for 3D printing is rapid prototyping. To fabricate a part using a manual machining process could traditionally take a month. An analog of that part can now be created with an in-house 3D printer in four hours. Going from four weeks to four hours. I call that instant prototyping. Instant is the best, except coffee.
Prototyping, however, is widely misunderstood. Laypeople and professionals alike think of 3D printing, ironically, as part of a one-dimensional development process. One-dimensional in that it is a linear and sequential development process. The thought is that each iteration must be used to test all aspects of the design simultaneously. All aspects of functionality (works-like) and all aspects of appearance (looks-like). Each iteration is a trial-and-error process to make the design slightly more refined / less crude. Each iteration is an attempt at a complete and final design, that somewhat misses the mark. This can work, to a point.
When working on a design I start with the end in mind. I ask myself, “What would the ideal version of this design be?” This is a mental exercise to remove any perceived limitations. Aim for the moon and land amongst the stars. Then I bring reality back into the equation, keeping the ideal a strategic benchmark, a north star to guide. Decisions about the inevitable pros, cons, and tradeoffs of design become less decisions and more flowchart gates towards that ideal. Often this approach reveals gaps in capabilities and pushes for learning or outside expertise from subject matter experts. Starting with a specific process (such as 3D printing) is to prematurely impose potentially significant constraints on the realm of possibilities. It is deciding to be a design cartographer instead of an explorer, an aviator instead of an astronaut. Time, resources, knowledge, tools; constraints come easily and naturally to any project without any assistance.
To make something great and lasting requires a holistic approach. It requires looking at the design from many angles, from the lens of many stakeholders, and inserting value in many ways. Ironically, to design holistically involves breaking apart the whole into its component parts (physical) and concepts (purposes). Comprehensive design means straying from the well-trodden (1D) path into a complex neural network. Breaking a problem into its sum parts to understand and refine. Then finally recombining and reconstructing the individual learnings, maybe with 3D printing, probably not.
As the Good Fast Cheap paradox goes, pick any two. 3D printing can let you do all three: the Holy Grail. But good to a point. The technology(ies) are coming fast and furious with capabilities and accessibility to size, material, and density homogeneity. A design’s parameters might call for plastic (lightweight, insulative) or metal (strength, shielding). Sometimes a hybrid. There is no one-size-fits-all 3D printing solution and there never will be. 3D printing is not a panacea.
3D printing is a rock star, the lead singer of the band. But it is part of a band, a group with other members (manufacturing processes and prototyping technologies) that may get no spotlight but give every song depth and harmony. Where 3D printing fails is when it tries to be all things to all people. Even powerhouses like Mick Jagger and Ginger Spice can’t go it alone. I like to think of myself as part of a prototyping fantasy sports league, strategically picking the best players with different strengths that form the best overall team.
Where 3D printing adds true game-changing value is when it is used to focus on one aspect of a design. A parallel versus series approach. For example, creating multiple designs and prints whose only purpose is to demonstrate the exterior shape. The sole purpose of the experiment is to define the industrial design. The interior can be featureless for quick design and easy printing. These form designs can be shared, voted on, tweaked, and down-selected until one final design is locked down. One less variable (the appearance) in the 3D multivariable matrix equation that is design. With the exterior shape defined, one can work from the outside in on the next hurdle based on what makes sense from a risk mitigation or variable isolation standpoint. That is an example of how the order of breaking a larger project into subprojects with the help of 3D printing can work. It’s a process, the nature and order of the subprojects can and will change based on the project. This process works. I have used it for 20 years on hundreds of projects in completely different industries. And I’m not the only one.
3D printing is just technology. Technology doesn’t solve problems in and of itself. Technology doesn’t do anything in and of itself except perhaps create internet hype and confuse my parents. It’s a tool. Like any other tool. Sure, a super-awesome next-level game-changing tool that can be used to create better products faster or cat armor. A tool that, when wielded deftly, can create masterpieces or be dropped on a toe.
You can’t use a 3D printer to print anything. You can make anything with a 3D printer.