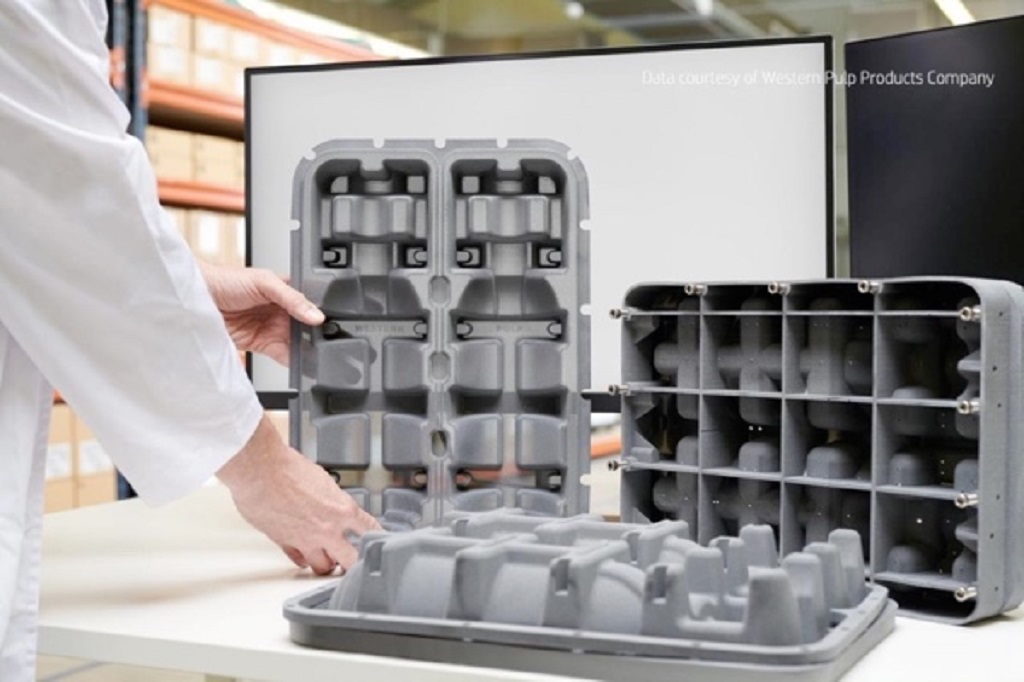
HP has developed a new and innovative Molded Fiber Advanced Tooling Solution with the intention of delivering lighter, faster, more durable, user-friendly, cost-efficient, customizable, and environmentally friendly packaging.
HP’s Collaboration
There’s not much new to say about the popular information technology company. In HP’s words:
“HP Inc. creates technology that makes life better for everyone, everywhere. Through our portfolio of personal systems, printers, and 3D printing solutions, we engineer experiences that amaze.”
The company is partnering with Pulp Moulding Dies Inc. (PMD) to deliver “the next-generation of durable, lighter, faster, and easier to use tools”. HP is also working with packaging solutions companies such as Veritiv, which “works with customers from design concept to completion, to accelerate the adoption of more innovative and sustainable molded fiber packaging designs for customers across industries including food service, consumer product, medical, and industrial markets”. Customers who are already using HP’s new molded fiber applications include Fiber Innovation, Pacific Pulp Molding Inc,, Pulp Moulded Products Inc. (PMP), and Western Pulp Products Company.
Mariona Company, Global Head of Molded Fiber Solutions, HP Inc. said:
“As businesses around the world, including HP, make the commitment to plastic-free packaging initiatives, the molded fiber industry is leading the way with its production of renewable, recycled and natural fiber for products and packaging. HP operates with sustainable impact at the core of our business and we are proud to bring breakthrough HP innovation and world-class services to manufacturers of molded fiber products. Powerful design capabilities and the advanced production capabilities of our new HP solution are opening up entirely new packaging possibilities for the industry.”
The Breakthrough Solution
Molded fiber or molded pulp is usually made from recycled paperboard and or newsprint, though it can also be made using plant cellulose fibers like bagasse, bamboo, and wheat straw. Renewable molded fiber packaging products are currently being used in handling and packaging thousands of products such as food containers, household items, electronics, and single-use medical service items for their biodegradable and recyclable properties.
HP’s brand new Molded Fiber Advanced Tooling Solution deems the time- and labor-consuming processes involved in traditional manufacturing processes unnecessary. With the help of HP’s innovations and findings in digital manufacturing software and data intelligence such as their new digital design platform and HP’s industrial 3D printing technology, this solution offers a “digitally-designed experience enabling more efficient, optimized design” and replaces “the need for handcrafted screens, CNC machining, and manually drilled form tools”.
Not only is HP’s molded fiber packaging sustainable, their tooling is also made from vegetable castor oil, which is 100% renewable. HP also states that it enables “70% reuse of surplus material in the production of its tools”.
The strength and flexibility of the material allows for tools to have optimal performance in terms of mechanical properties and consistency. Improvements in the overall equipment effectiveness and flow enhancement through HP’s new tooling solution should enable manufacturers to “produce more parts using less fiber for more sustainable production processes”.
HP’s partnership with PMD has allowed them to advance molded fiber tooling capabilities for customers of PMD from around the world who produce a variety of packaging. PMD’s expertise in molded fiber tooling and advanced design paired well with the production capabilities of HP’s digital manufacturing platform which has allowed for advances in custom screens and improvements in the overall dewatering process to result in PMD being able to produce molded fiber tools that are 10 to 20 times lighter than conventional tools.
Troy Mutton, President of PMD, says:
“We’re all in with HP’s new solution.”
He explains:
“We’ve used every machine and tool under the sun and they are all heavy, massive dinosaurs with major limitations compared to HP’s innovative 3D printing solution. I’ve been ready to take advantage of the time savings and unlimited design opportunities provided by 3D printing for more than two decades, but until now, no technology has met our needs for quality and consistency like we are seeing from HP. HP has delivered a true production technology that meets our needs and will help us continue to lead the industry.”
Thoughts On This Solution
I think in recent years, we’ve especially come to realize how bad the climate crisis is in our world and how it’s not a matter to be taken lightly. While the individual plays just as much a part in bettering this crisis, large companies also have a sizable impact on our environment. They also serve as a role model for the rest of the world as they are under constant scrutiny of the media.
I think it’s great that a company like HP has used their resources and partnered with several other leaders in the industry to come up with a solution that doesn’t take a heavy toll on the environment but also delivers in terms of performance, because at the end of the day, the goal is for any solution to solve a pre existing problem with its counterparts while not reducing the efficiency of the tool in and of itself. When HP is able to demonstrate that their parts are just as effective if not more so than before while also being better for the environment, I think we are in a win-win situation and hope to see more such innovations in the near future!
Via HP