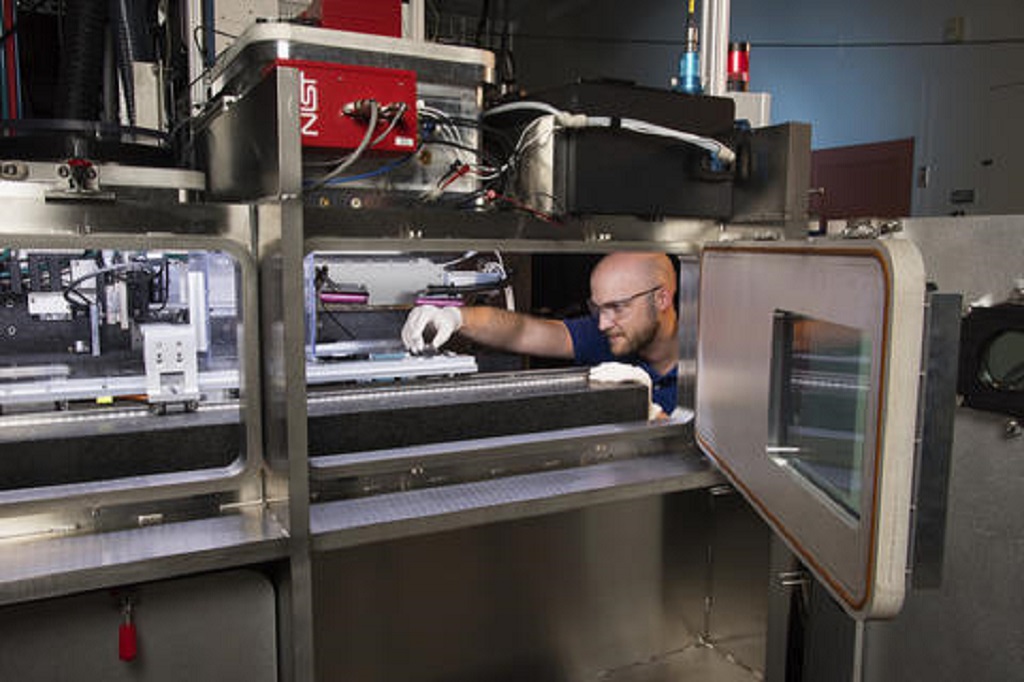
At the end of 2020, the NIST awarded almost $4 million in grants supporting metal 3D printing measurement methods and standards.
The grants, from the U.S. Department of Commerce’s National Institute of Standards and Technology (NIST), are intended to increase US competitiveness in these technologies. With more quality assurance and standards in place, metal AM can see much higher rates of adoption.
Metal AM and NIST
NIST is a “nonregulatory agency of the U.S. Department of Commerce [that] promotes U.S. innovation and industrial competitiveness by advancing measurement science, standards and technology in ways that enhance economic security and improve our quality of life”.
NIST hopes to address barriers in the adoption of metal additive manufacturing such as “surface finish and quality issues, dimensional accuracy, fabrication speed, material properties, and computational requirements” through its own research and the grants which were provided to the following organizations to be spent over two years.
The NIST Metals-Based Additive Manufacturing Grants Program include:
Georgia Tech Research Corporation ($1 million)
This million-dollar project “will analyze detailed data gathered during a powder bed fusion process to both control the manufacturing and predict the final properties of the manufactured parts”. It aims to establish “a comprehensive basis to qualify, verify and validate parts produced by this technique”. An alloy of titanium is the primary focus of this project at the moment with its extensive applications in the healthcare and aerospace sectors.
University of Texas at El Paso ($1 million)
This project will “define a test artifact that will standardize the collection of data on the process inputs and performance of parts made via laser powder bed fusion, an important method of metals-based AM. Academic, government and industrial partners will replicate the artifact and collect data on the key inputs to the process and the resulting properties of the artifact for a data repository”. This will aid in achieving better understanding of the AM process as a whole and will accommodate for more confidence in final parts.
Purdue University ($999,929)
Since parts by AM now need to undergo extensive sets of tests, this project intends to develop a “standardized approach to predict key performance properties through measurements of material microstructures and the use of mathematical models”. This project has the potential to streamline testing and help understand part performance with ease.
Northeastern University ($999,464)
This project hopes to optimize sensing approaches to create “a suite of sensor technologies that will help optimize cold spray additive manufacturing. Cold spray AM processes have the potential to create parts that are more durable and stronger than those made with other AM processes”. These new sensors will allow for better control of the technique by characterizing the properties of powder feedstock and key parameters such as temperatures and part dimensions.
Final Words
Wilbur Ross, the U.S. Secretary of Commerce, says:
“NIST and the entire Department of Commerce are committed to providing American organizations the necessary resources to thrive and build upon their discoveries and innovations. I congratulate these grant awardees, whose contributions to metals-based additive manufacturing will certainly help America play a bigger role in the industry.”
Under Secretary of Commerce for Standards and Technology and NIST Director Walter G. Copan explains:
“By addressing important measurement challenges, these projects will improve U.S. manufacturers’ ability to use metals-based additive manufacturing to make high-quality, innovative and complex products at high volume. We look forward to working with these organizations to further leverage NIST experience and expertise in this key area of advanced manufacturing.”
NIST even anticipates that they will be funding additional projects as a part of the second phase of awards in the first half of 2021.
My Thoughts
3D printing entirely was somewhat of a new field for me just a couple months ago. Yet, while doing my research, metal AM was always projected as a complicated and time-consuming form of manufacturing in comparison to other 3D printing technologies. I love that NIST is investing money into both its own research and that of other organizations to speed up the discovery of more optimized methods that may help make the process easier as it seems to have so many benefits that we don’t want to miss out on because of lack of advancement!
Via NIST