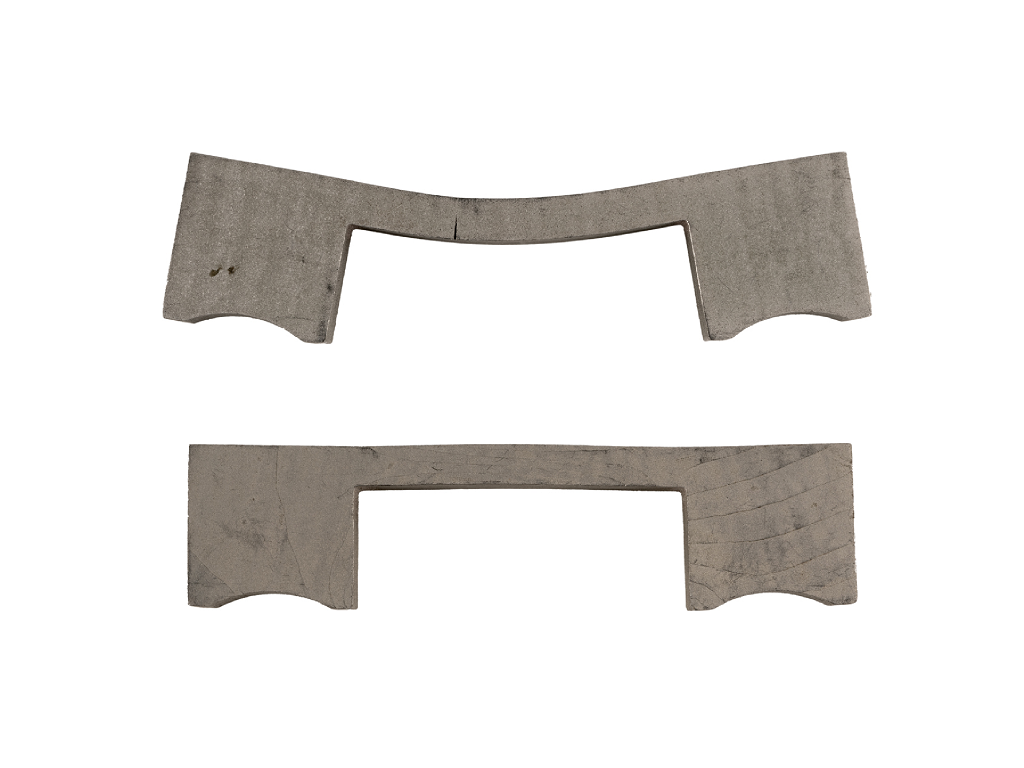
Desktop Metal recently introduced a new software tool focusing on metal sintering simulation; the team behind Live Sinter shares a deeper look.
Live Sinter is a software application that simulates conditions metal prints experience during sintering. Shrinkage of up to 20% can lead to significant distortion of original design files in powder-based metallurgy like binder jetting. When those distortions are accounted for and counterbalanced in the design file, though, the integrity of the intended design can actually come to fruition in the completed part.
That’s what Live Sinter does: it simulates the effects of sintering and comes up with “negative offset” geometry that compensates for distortion. And it does it in minutes.
Developing Live Sinter
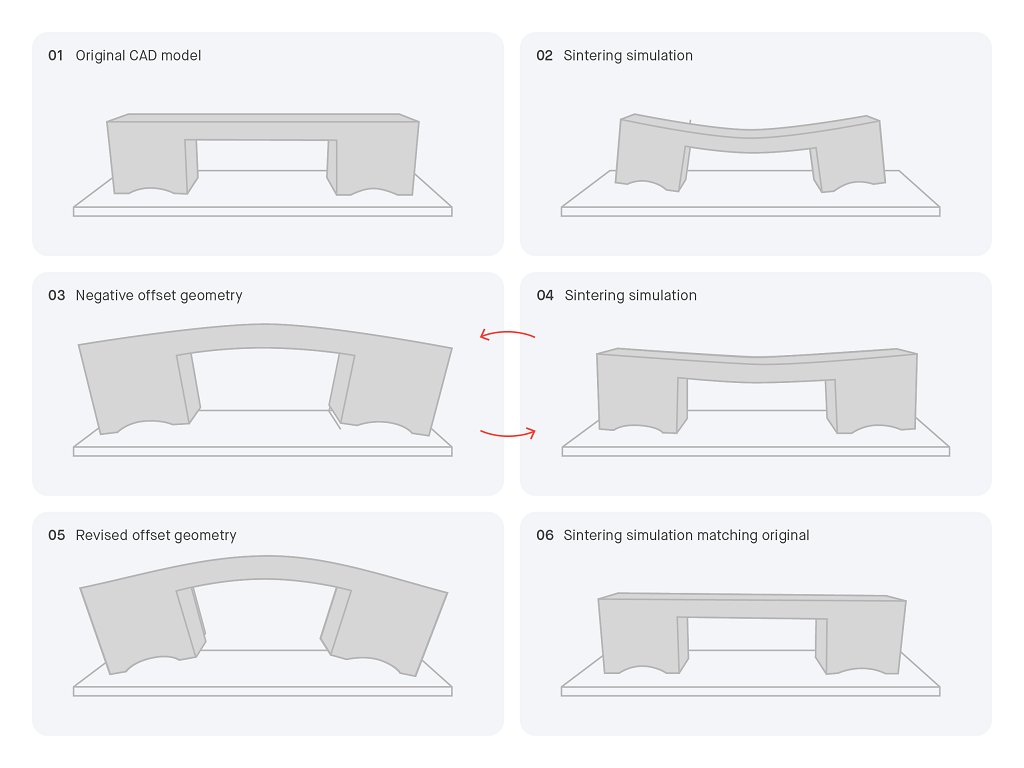
Andy Roberts, Desktop Metal VP of Software, shared a demo as we sat down for an in-depth discussion of Live Sinter.
The product came of “about a year of development,” he explained:
“We built this on top of our generative design program, so we had a head start of about two years on that,” he continued, noting existing work from Desktop Metal’s Live Parts. “There are a lot of generative design tools out there and we used Live Parts because it has a dynamic physics engine in it. ‘Dynamic’ means it develops tools over time, actually modeling something as it changes over time. The dynamic physics engine is using, essentially, particles that are all connected together, kind of like springs and dampers. You can imagine this giant structure of spheres that mush together and can slide; it behaves more like a viscous solid material.”
The motivation to develop the new product came from, basically, need. Metal 3D printing with Desktop Metal’s systems requires supports — for the FFF-based Studio System, during printing and sintering, and for the Production System, only during the sintering stage since the binder jetting process doesn’t require print supports.
“We almost always print supports to work not only in the printing stage but also in the sintering stage. When you put it all in the furnace, it shrinks, and when it comes out you can remove the supports and you have your part. We got into the practice of printing supports at the same time we printed parts. But we realized we waste a lot of material printing supports when we don’t need them for printing, and only need them for sintering,” Roberts noted.
Sagging and deformation require a thorough understanding of what happens in the furnace, though, to inform the best way to have a part keep its intended shape during sintering. The deformation isn’t linear, Roberts observed; “it’s sagging and warping like a potato chip.”
So the focus turned to simulating behavior in the furnace, with the goal to “tweak the geometry to get a part that deforms at the printing stage, but when it comes out of the furnace it would be straight.” This required “adding layers of physics to the engine.”
Roberts and his team coupled “gaming physics engine from NVIDIA with engineering-level mesh analysis,” putting to use NVIDIA’s well-developed work in AI and “using tech developed for other industries.” Fine tuning parameters, checking against real-world samples to ensure the simulation matches what happens with physical parts, and understanding factors like coefficients of friction and compliance of material finally led to a simulation that generally has “less than 1% error” when compared to those physical samples. Desktop Metal has been using Live Sinter internally for about four months, and “we do a lot of benchmarks.”
Live Sinter is coming into play in what Roberts accurately notes as a competitive space. There are, he noted, two general approaches to this type of development:
“One is to scan the parts. Then you use the scan of the final shape to try to tweak the starting geometry, and use an iterative approach. If you were to print the part, sinter it, manually tweak it, then print it again and sinter it, it’s time-consuming. It usually takes one to two days to print and depowder and one to two days to sinter and finish. Of course in a production shop you can do many operations in parallel, but to figure out offset you have to do it serially. That can be four days per iteration, and it would be 20 days to get the design right. Whereas with our approach, we can simulate five sintering runs in about 25 minutes.”
Live With Live Sinter
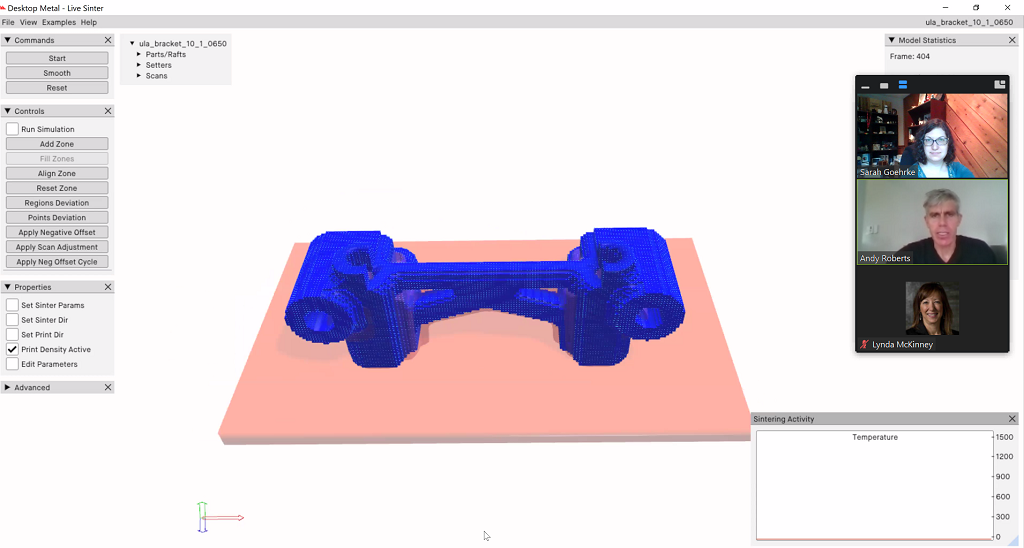
In addition to Desktop Metal’s own internal use, they have made Live Sinter available to one external customer via cloud. Availability will primarily be through local machines — “important because some companies really don’t want their CAD data going outside their walls” — as well as deployment via a cloud option.
From here, we moved into a real-time demo of the desktop application.
Looking at a bracket example, Roberts proceeded to simulate what happens in the furnace. This was a relatively small part, with 91,000 cells (a complex part can have closer to 700,000 cells), requiring a six-minute Live Sinter run.
The program brought the temperature up; at about 900C is “where things start to shrink and it gets interesting.” Different colors on the part represent different behaviors, including different shrinking and stretching in different directions.
Live Sinter is designed to be tuned to the specific material, 3D printer, and furnace in question for a given print. Sample parts, as noted, help compare Live Sinter’s simulation to real-world results for qualitative evaluation.
Once behaviors are understood and predicted, Live Sinter applies the negative offset, using algorithms to figure out what that should look like for a given part. This, Roberts noted, “is an entirely different physics problem.” Live Sinter essentially compares the result to the desired shape, then tweaks the negative offset — then reruns, tweaks again, and runs again, usually four or five times over.
“Usually by five times it’s done, for the most part. This gets it to the point where it simulates something it thinks will come out straight. We take this resulting shape and export it,” he said.
Live Sinter can work with complicated design files, such as those with embossed lettering, to deliver a final product maintaining all the complexity intended.
So far as their own use has shown, Live Sinter is proving its mettle for metal 3D printing. Desktop Metal has used Live Sinter to perfect a part for their carbon fiber Shop System, a nozzle that gets up to 400C. Machining the nozzle wasn’t an option due to its tubular shape, and with a DMLS 3D printer, prices would run significantly higher. Binder jetting it was the best move and, with Live Sinter, become feasible. This is what Roberts calls “a case study for using an affordable 3D printing approach with sintering software.”
Live Sinter will be made available for Shop System and Production System users beginning Q4 2020.
“Live Sinter has the ability to be used with other printing systems, as well as other metal processes,” Roberts added.
In phase two, Live Sinter will allow for additional materials and binders and will allow customers to do their own tuning. Desktop Metal is also planning, eventually, to release Live Sinter as a standalone product, helpful for, for example, those running MIM operations.
“For MIM, they could offset negative geometry with the assumption they would create a mold and print it, then put it in the furnace and it would come out straight,” he said. “Our number one priority is to make our own customers successful with our own printers and furnaces.”
The demo and discussion highlighted an interesting and usable piece of simulation software that could benefit many in metal 3D printing. As always, though, I look forward to hearing from customers once the product is out in the world with actual customers.
Via Desktop Metal