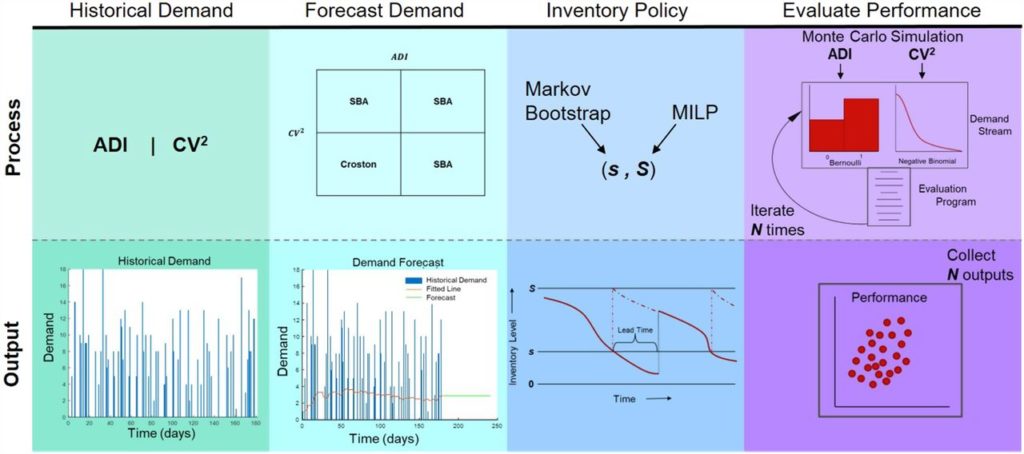
Much has been said about using additive manufacturing to alleviate problems in supply chains, but how do you do so?
Itās 2021 and supply chains are still horribly messed up worldwide. Factories canāt produce products to plan, shippers canāt deliver products where they need to be. Buyers are left waiting and scrambling for alternatives.
One alternative is to use additive manufacturing options. This is because the nature of 3D printing technology is fundamentally different than standard mass manufacturing:
Mass manufacturing: produce large numbers of identical parts at low unit cost
Additive manufacturing: produce smaller numbers of different parts at moderate unit cost
For some supply chain situations it may be that the company is short only moderate quantities of parts, and it is theoretically possible to produce them with additive manufacturing. However, these parts may cost a bit more each, but if the alternative is to have no parts, then perhaps thatās a good option.
Many companies have turned this way, and it makes sense.
But how, exactly, does one implement additive manufacturing into a supply chain?
Supply chains can be extremely complex and distributed in nature, making the insertion point not obvious. Should the AM center be placed here, or there? How many centers are required? What parts should be considered for AM production? When should a part be produced with AM?
There are many questions. Itās not as simple as installing a 3D printer inside a factory. There may be many factories. There may be factories where assembly takes place. There may be multiple stages to product development taking place in different regions.
While AM may seem to be an answer, it is unknown how best to use it to strengthen a given supply chain.
Until now, that is.
It turns out researchers have been working on this very issue, and have come up with some answers.
Researchers from North Carolina State University and West Point published their findings in a paper entitled, āPerformance tradeoffs for spare parts supply chains with additive manufacturing capability servicing intermittent demandā, where they examine the factors governing optimal use of AM in supply chains.
This is, of course, a big consideration for the US military, which operates in a vast number of distant locations, each requiring parts of various types at different frequencies. The research should enable the military to optimize their use of AM, and certainly this could be the case for private companies as well.
The researchers used a simulation approach to evaluate different styles of AM use. They explain:
āThis work evaluates various AM-enabled supply chain configurations through Monte Carlo simulation. Historical demand simulation and intermittent demand forecasting are used in conjunction with a mixed integer linear program to determine optimal network nodal inventory policies. By varying demand characteristics and AM capacity this work assesses how to best employ AM capability within the network.ā
Specifically, they focused on answering three questions:
- When should adding AM capability into a logistics network be considered?
- If using AM, where should AM capability be located in the network?
- After establishing it, how should the AM capability best be resourced, managed and employed?
As I read through their paper, it becomes clear very quickly that this is an insidiously challenging problem with many factors involved. For example, one is determining a build time for a given part. That might sound like an easy question, but it depends on multiple factors, including print time, materials, operational processes, GCODE, part geometry, post processing, shipment and more.
There are many similar complex factors in the equation.
What did they find? They explain:
āThis research assesses the preferred AM-enabled supply chain configuration for varying levels of intermittent demand patterns and AM production capacity. We demonstrate that variation in demand patterns alone directly affects the preferred network configuration and highlight the dominance of the centralized configuration in the high ADI, CV2 value range due to pooling of both AM capacity and demand upstream in the supply chain. The tradeoffs between the centralized and distributed configuration are quite clear in our results. Further understanding of the tradeoffs between the distinctly opposite allocation strategies is brought about through sensitivity analysis of the relationship between demand volume and relative AM production capacity. The results show that the relationship between the demand volume and relative AM production capacity also affects the network configuration performance.ā
Any manufacturer facing these challenges should certainly review this paper, which apparently is the only paper yet produced on this complex topic.
Via Emerald