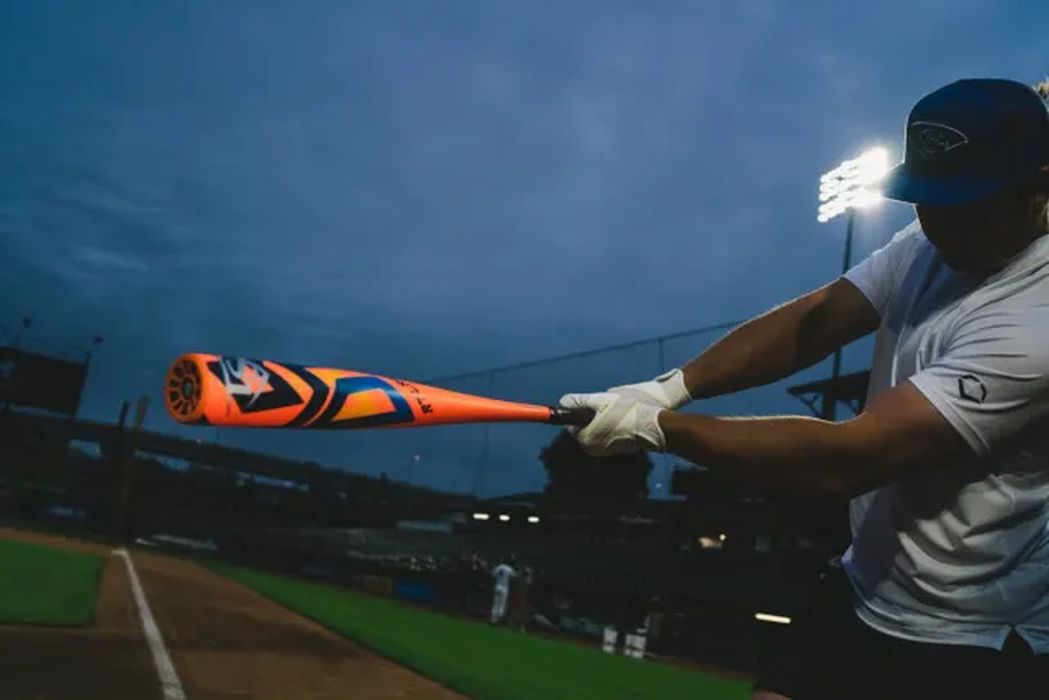
Louisville Slugger is combining modern techniques with tradition by using 3D printing to create next generation equipment.
Americaās pastime and manufacturingās drive to look towards the future come together at the Louisville Slugger Innovation Center in Roseville, Calif. Since 1884 Louisville Slugger has been manufacturing baseball bats and equipment for Major League Baseball as well as college, high school, and youth teams.
At the Slugger Innovation Center, product designer John Steel uses a combination of traditional and modern tools for the design and manufacturing of aluminum and composite baseball bats.
Steel has incorporated a stereolithography (SLA) 3D printer from Formlabs to create both prototypes and manufacturing aids for the composite and aluminum bats used by youth and collegiate players around the world.
āIf youāre not 3D printing, youāre not going to keep up,ā Steel says.
Eye on the Ball
Players are always looking for an edge or little tweak that will help them swing faster and hit harder. For youth players, that edge might be as simple as finding a bat with the right weight that lets them make solid contact and keep their grip while they learn the game.
Both the Innovation Center, which focuses on equipment improvement, and the Slugger Science facility, which focuses on athletic analytics, help Louisville Slugger find that edge from a manufacturing and product development perspective.
Speed of Development
At the Louisville Slugger Innovation center in Roseville, engineers and designers have access to the latest tools and processes to develop the best products possible.
Steelās first manufacturing job provided a solid introduction to the combination of traditional and modern techniques. He then moved to a product design startup where he was using two Formlabs Form 1+ machines to rapidly iterate.
At Louisville Slugger, Steel has used his experience in merging the traditional with the modern to combine desktop 3D printing with traditional lathes, a CNC metal shop and a composites workshop. āWeāre able to rapidly produce prototypes for quick iteration and testing. We use it every week, and if weāre working through a new design, weāll iterate on it every day,ā says Steel.
The speed of iteration allows the Slugger team to release new products regularly while also keeping up with demand for bats. ā3D printing is a great tool to reduce the amount of time it takes to get to market. You can use it from prototyping the initial design, to problem-solving the final manufacturing,ā he says.
Steel and his innovation team are continuously iterating and pitching new ideas, and the Form 3+ helps them get those ideas through to the next stage even faster. āIāll have an idea, design it and send it to the printer in 30 minutes, then bring it to the next meeting. 3D printed visual aids are worth their weight in gold,ā says Steel.
3D printing improves the understanding of the product development process and can help eliminate any crossed wires down the road. That team cohesion enables Steel and other designers to keep their workflow streamlined and the productivity high. āOften when looking at 3D renderings, we lack scale. Printing parts helps when attempting to reference how something compares in size along with being able to test ergonomics and fitment into existing products.ā
Read the rest of this story at ENGINEERING.com