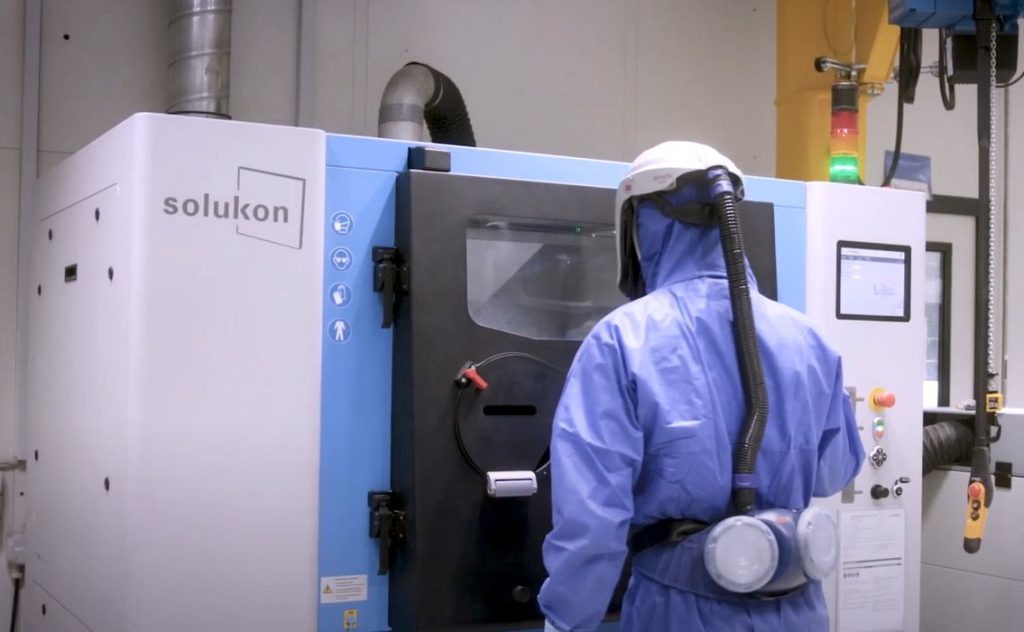
I’m looking at a new solution from Solukon that can automatically depowder 3D prints.
Depowdering is a process required for parts built with several different 3D printing processes, including SLS, DLMS and binder jetting. Each of these processes has the common element of loose powder integrated with the print itself.
In fact, at the conclusion of print jobs using these processes, you’ll find a build chamber completely full of powder with the print buried somewhere within it. Powder will also be in any gaps or voids in the object’s structure.
This powder must be removed before further post processing and part use can be considered. This is actually a critical step, because in certain applications stray powder would disqualify the part.
Imagine, for example, if you received a hip implant, only to find there was loose powder inside the complex structure that became dislodged and traveled through your body. That’s why depowdering is so critical.
Early depowdering equipment consisted of a sealed chamber in which a vacuum could slurp up the loose powder. Bottom grates would catch powder as it fell off the print during manual manipulation. The operator would turn the print to and fro, hoping to coax out the remaining particles from nooks and crannies within the structure.
As you can imagine, this process is tedious and requires experienced manual labor. It’s also prone to mistakes and inconsistency, which is certainly not what you’d want in an end-use part manufacturing operation.
Solukon’s depowdering system is quite different. It’s a smart device that is now powered by their advanced SPR-Pathfinder software, and the method of operation is very interesting.
The workflow is to first perform an extraction of the part from the build chamber and mount it in the Solukon depowdering system. Then the CAD file for that part is uploaded to SPR-Pathfinder.
The software then analyzes the structure of the part using the CAD file to develop a simulation of the particle flows when the object is tilted in different directions. Eventually it develops a sophisticated rotational sequence that, when executed, is guaranteed to remove all loose powder from the part.
The rest is easy: the operator simply runs the machine and the process is entirely automated from that point. According to operators at Siemens Energy in this video, “no witness is required” to guarantee that the part was properly depowdered.
Solukon explains how it works:
“To remove excess powder from complex internal structures, SPR-Pathfinder® uses the build job’s CAD file to calculate the ideal motion sequence in the Solukon system. The SPR-Pathfinder calculations are based on a flow simulation that analyzes the part’s digital twin. The individually calculated motion sequence is then read by the Solukon system, which in turn runs the programmed paths. This ensures that even the most complex parts are cleaned—in record time and without any human programming effort.”
This is a significant development, as the use of advanced 3D print applications is colliding with post processing: the more complex the part design, the challenging is the powder removal.
These days, the game is to make incredibly complex parts, leveraging additive technologies to lightweight parts or create highly complex fluid flow chambers, all of which pose significant difficulties for manual powder removal.
Solutions like automated depowdering from Solukon are part of the answer that will lead to true mass manufacturing using 3D print technology.
Via Solukon