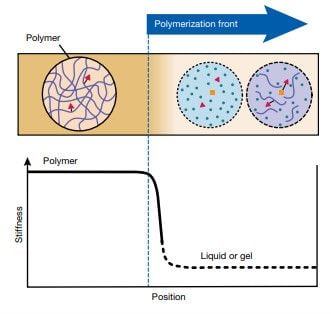
Using a chain reaction, this new polymerization process could save millions in curing costs.
Thermoset polymers and composite materials are important in a wide variety of industries, including aerospace, automotive, and indeed any industry that makes use of fiber-reinforced thermoset polymers. Present technologies for manufacturing high-performance thermoset and fiber-reinforced polymer composite (FRPC) parts rely on curing in large, expensive autoclaves or ovens.
For example, curing a small section of the Boeing 787ās carbon fiber/epoxy fuselage is estimated to require 350 gigajoules (GJ) of energy during its eight-hour cure cycle, producing more than 80 tons of carbon dioxide. Consequently, there has been much interest in producing these materials with less energy, reducing their costs and environmental impact, and furthering their application in commercial markets.
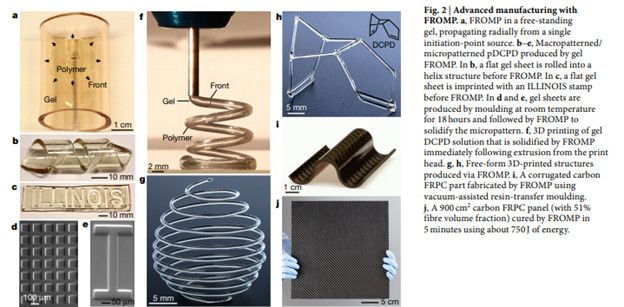
According to a paper first published in Nature in 2018 by researchers at the Beckman Institute for Advanced Science and Technology, frontal ring-opening metathesis polymerization (FROMP) could hold a key to rapid, energy-efficient polymerization.
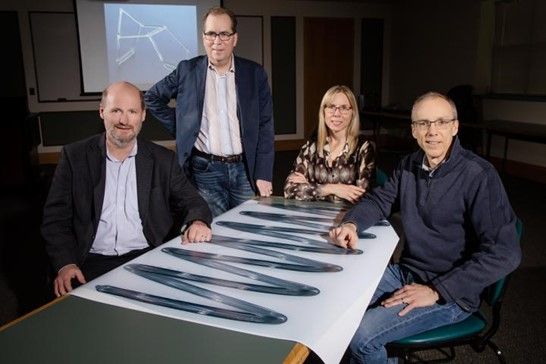
More recently, in 2020, Beckman institute researchers improved their FROMP process. The new method enables a wider range of materials with better control over their thermal and mechanical properties.
How Does Frontal Polymerization Work?
Whereas traditional curing uses heat energy added by an oven for materials synthesis, in FROMP the enthalpy of polymerization provides the energy, with no external heat source needed.
In frontal polymerization, a solution of a monomer and a latent initiator is heated locally until the initiator is activated for polymerization of the monomer, producing heat from the polymerization that further drives the reaction. The autoactivation process produces a propagating reaction wave that rapidly transforms the available monomer into polymer.
āBy touching what is essentially a soldering iron to one corner of the polymer surface, we can start a cascading chemical-reaction wave that propagates throughout the material,ā said aerospace engineering professor and lead author Scott White. āOnce triggered, the reaction uses enthalpy, or the internal energy of the polymerization reaction, to push the reaction forward and cure the material, rather than an external energy source.ā
What Type of Polymerization?
Polymerization describes the formation of longer molecule chains from monomers. For example, ethylene gas is the monomer that is polymerized upon contact with catalysts, such as titanium chloride, to create the commodity plastic polyethylene. This is polymerization of a thermoplastic.
FROMP works on thermoset plastics. For these materials, polymerization or curing refers to the process by which polymer resins (in most cases) are irreversibly hardened into plastic materials by crosslinking the polymer chains to create a polymer network. Silicone, synthetic rubber, and epoxy resins are examples of thermoset plastics.
Read more at ENGINEERING.com