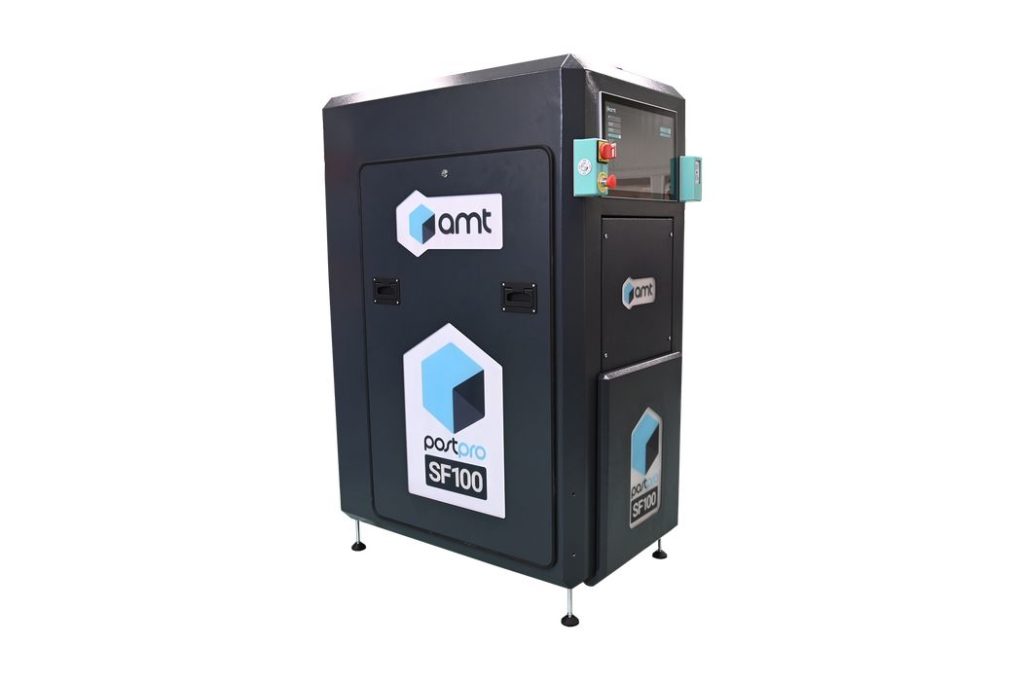
AMT introduced a new line of highly advanced post processing devices for additive manufacturers, the SF Series.
AMT is a relatively young company that focuses on intelligent post processing devices. The unfortunate state of affairs in 3D printing these days is that many 3D printing processes absolutely require parts to be processed after the fact before they can be used.
Post processing typically includes activities such as removing stray powder left in geometric niches, smoothing the surface and dyeing the parts in some cases. AMT has focused on smoothing part surfaces.
They launched their initial products two years ago and have made very significant progress since then. According to CEO Joseph Crabtree, with whom we had a chat last week, AMT’s equipment has, cumulatively, now processed over five million parts. They market in dozens of countries and continue to expand. Crabtree said that the company has grown from around 50 staff in 2019 all the way to over 100 today. They’ve also raised a US$15M Series B investment round to help them build their sales and distribution networks worldwide.
With feedback from over 70 customers that have been using their equipment, they’ve been able to learn quite a bit about their machines as well as the workflow executed by customers. AMT has taken this knowledge and re-engineered their systems over the course of two years and come up with a new system, the SF Series.
Crabtree describes the SF Series as:
“A better, faster, higher throughput machine that’s much more efficient with consumables.”
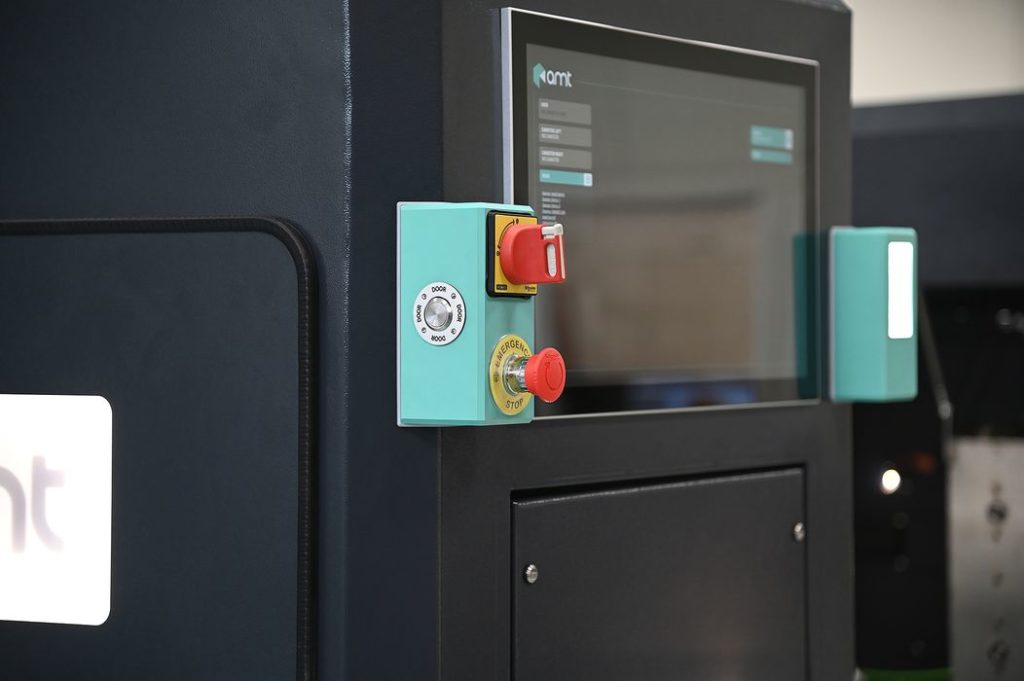
The SF Series includes a number of new features, including compliance with Industry 4.0, automatic consumables re-ordering, an ability to use multiple consumables for different applications, and a new ergonomic design.
There are three SF models: the SF50, SF100 and yet-to-come SF150. There’s also a special SF100+ model that I’ll describe shortly.
All of these devices are used to perform consistent part surface smoothing on a variety of materials using a proprietary chemical process. The system is intelligent and uses automation to complete the job with as little effort and consumables used as possible.
While the SF50 is targeted at smaller workshops and research institutions, the SF100 and above are designed for production workflow.
The key design feature is speed. Crabtree explains:
“Processing time is reduced by 25% on the SF Series. This leads to increased throughput, which is very important for manufacturing as the part cost is reduced. Capital expenses don’t matter so much, but the unit part cost is incredibly important when millions of parts are produced.”
In other words, AMT — and myself — expect a massive increase in the use of 3D printing for larger volume production in the near future. They’ve positioned the SF Series to be able to handle that level of volume by speeding up their processing time.
But wait, there’s more. The SF100+ model doubles throughput to only 40 minutes processing time. To provide a perspective on how productive this upgrade could be, AMT’s original PostPro3D could process 280 parts in 120 minutes, while the new SF100+ can process 269 parts in only 40 minutes. That’s almost doubling the throughput.
There’s another very interesting aspect of the SF Series: size. Crabtree explains:
“Everyone has a problem with floor space, so we miniaturized the technology, but with same chamber size. This is much more cost effective from a floor space point of view. We’re extending the real estate upwards!”
If you were to look at the SF units with squinty eyes, you’d immediately see that AMT has basically flipped the old design on end, making it indeed a vertical setup that takes up far less space. This apparently saves some 75% of the floor space required for operation.
This is an important point. While each SF Series unit is itself more productive than prior models, the floor space advantage provides another way to increase throughput: parallel operation. With the same space you can install almost three SF Series units as compared to previous models.
For a manufacturer processing as many parts as possible, this could be extraordinarily important: adding machines can dramatically increase throughput and increase sales.
Via AMT