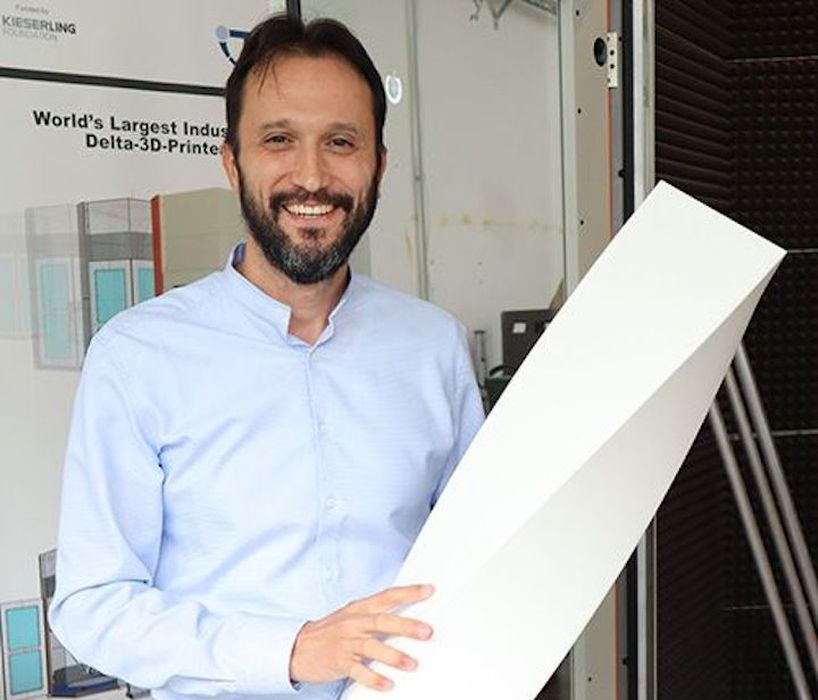
Researchers at Jacobs University in Germany are developing a large format 3D printer.
Said to be the āworldās largest industrial delta 3D printerā, the Honeycomb device is certainly big.
The machine itself is 4m tall, and the cylindrical build volume is 3m across and 2.5m tall. Thatās definitely large, and I am unaware of any other delta device that is even slightly close to this size.
The delta mechanism choice for this device is interesting, as it has not been used in large scale 3D printers previously. All of the large format devices Iāve seen from 3D Platform, BigRep, Thermwood and others are cartesian affairs.
The delta approach has the advantage of being a lightweight mechanism that should allow the toolhead to be more easily moved around due to lower mass and momentum. Theoretically, this should speed printing.
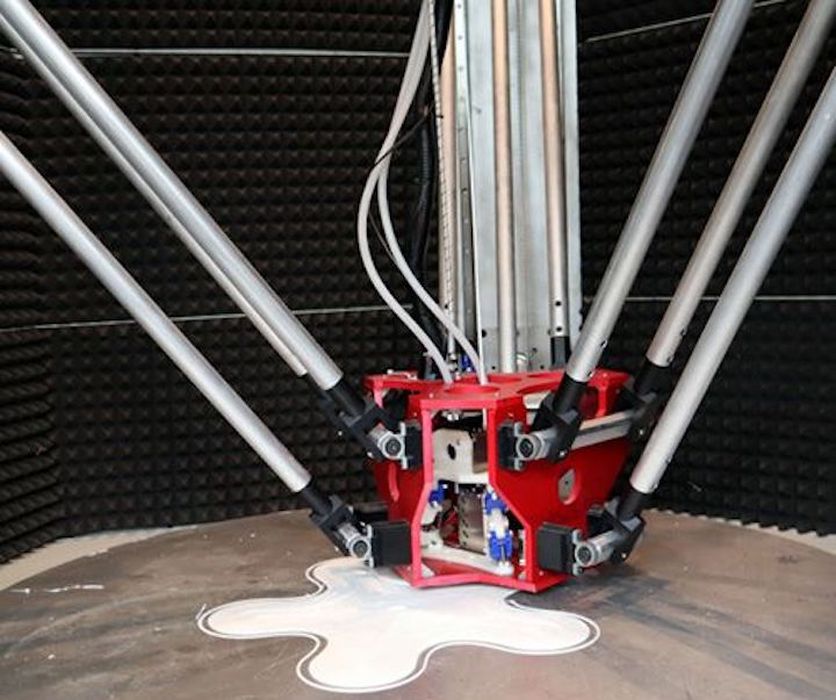
According to the release by Jacobs University, the Honeycomb can print up to 5kg per hour, and surprisingly uses PLA, PET and ABS filament. Normally large-scale machines use inexpensive pellets, but a future version of the device will be adapted for pellet material.
It appears the Honeycomb is a research platform, where the team will investigate the use of different nozzle diameters and even multiple print heads, something never seen with delta equipment.
The researchers also intend on developing an optical system that can provide real time print feedback for adjustments on the fly and thus achieve high quality printing.
While the machine is now testing prints of wind turbine parts, the team says they have been approached by multiple parties seeking use of the device for pilot projects.
This is an interesting project, but I do have some questions, specifically about the materials being used. Other companies that built large-format 3D printers quickly discovered that the slight warp incurred at small scales with common 3D print materials became problematic at large scales. The shrinkage is amplified along the long axes of the prints, and can cause print failure or corruption.
To counteract this effect, several manufacturers took two approaches: they used specifically designed materials that donāt warp nearly as much at the given thermal conditions; and they enclosed the build chamber to raise ambient temperatures and reduce the thermal gradient.
Both of those approaches donāt yet seem to be in the plans for the Honeycomb device, but itās likely they will as the project proceeds.