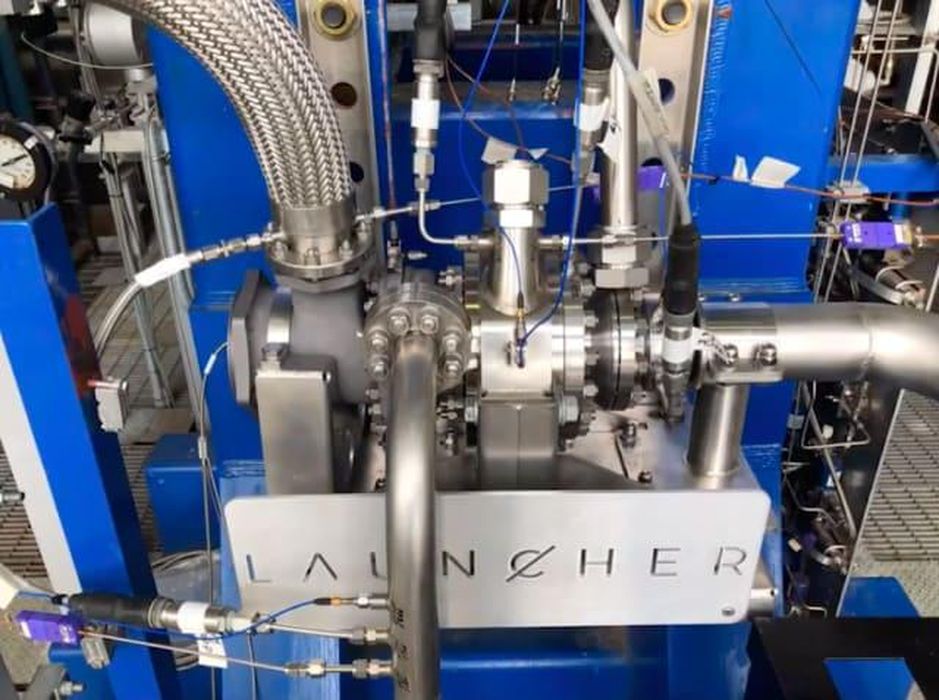
Rocket company Launcher has teamed up with 3D printer VELO3D and simulation software provider Ansys to overhaul the design and manufacture of its liquid oxygen (LOX) turbopump, a critical component of the company’s E-2 rocket engine.
The E-2 project is ambitious: Launcher aims to manufacture the highest performance liquid rocket engine in the growing commercial space industry—a rocket with the most thrust, most efficient propellant consumption, and cheapest cost per pound of thrust on the market. The E-2 will power the Launcher Light rocket, which is currently in mid-development and is expected to test-fly in 2024. The company intends to bring the engine to market in 2026, with a focus on launching small satellites.
For small vehicles such as the Launcher Light, the turbopump played a critical role in helping them reach and achieve the right level of thrust since it is directly responsible for injecting fuel into the engine. Launcher licensed an LOX turbopump design that had been used on the Ukrainian RD-8 rocket—a vehicle that had successfully completed 72 orbital flights as part of the second stage of the Zenit family of launchers.
Having found a component with a reliable performance record, the rocketmaker then worked with VELO3D and Ansys to redesign, manufacture and test the turbopump, installing an upgraded impeller and housings. As a result, the new component now features greater part complexity, lower production cost and faster lead times—and the production process is now able to rapidly iterate future parts.
To optimize propellant flow and pressure to the engine’s thrust chamber, Launcher had to produce and test it in-house. Launcher engineers used the Ansys CFX platform, a computational fluid dynamics (CFD) software for turbomachinery applications, to ensure that the rocket’s projected thrust level matched its actual performance. Simulated test runs helped the engineers to optimize the component’s parameters.
“Before we got into manufacturing, we worked with Ansys to simulate the performance of our flow path in our LOX pump,” said Andre Ivanovic, mechanical engineer at Launcher. “We wanted to do this to ensure that the predicted performance was in line with the desired parameters for our entire rocket engine system.”
Next, components of the redesigned pump—particularly the pump inlet and outlet housing—were 3D printed on VELO3D’s Sapphire metal additive manufacturing platform. The inlet housing was produced with aluminum alloy F357 and the outlet housing was printed using Inconel 718.
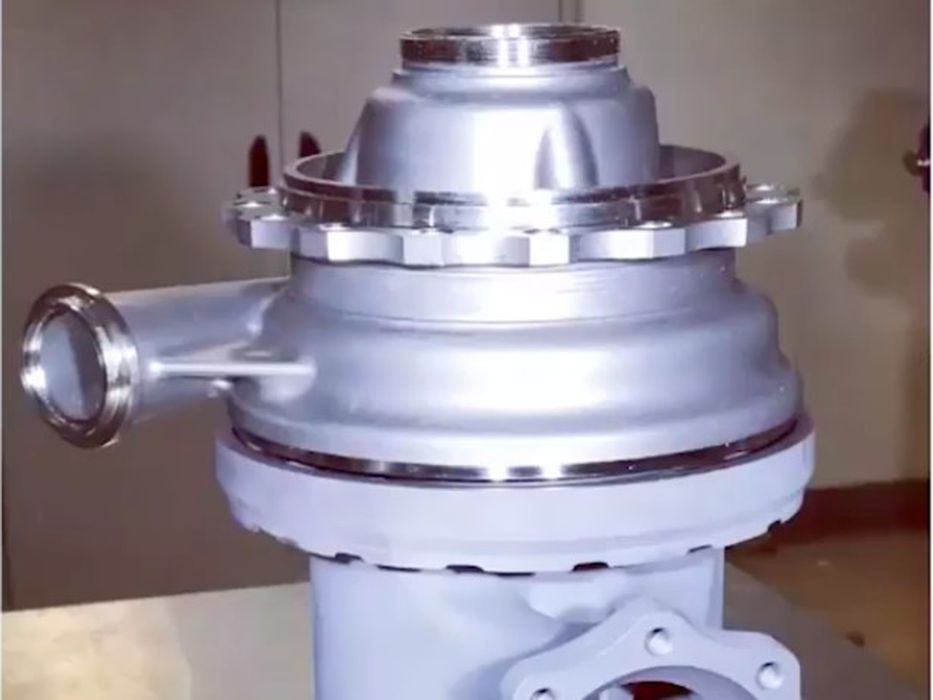
This required an incredible amount of precision because the LOX pump contains overhanging internal geometries that make it difficult to print using conventional powder bed printers. Many 3D metal printers struggle to meet the printing requirements due to limitations imposed by internal supports. The Sapphire system, however, was able to print the part without needing those internal supports.
With Sapphire, the 3D printing process resulted in a part that is significantly less complex, requires less time and wastes less materials than it would have using conventional manufacturing processes. The manufacturing process itself was also far less costly and labor intensive compared to conventional production processes.
Read more at ENGINEERING.com