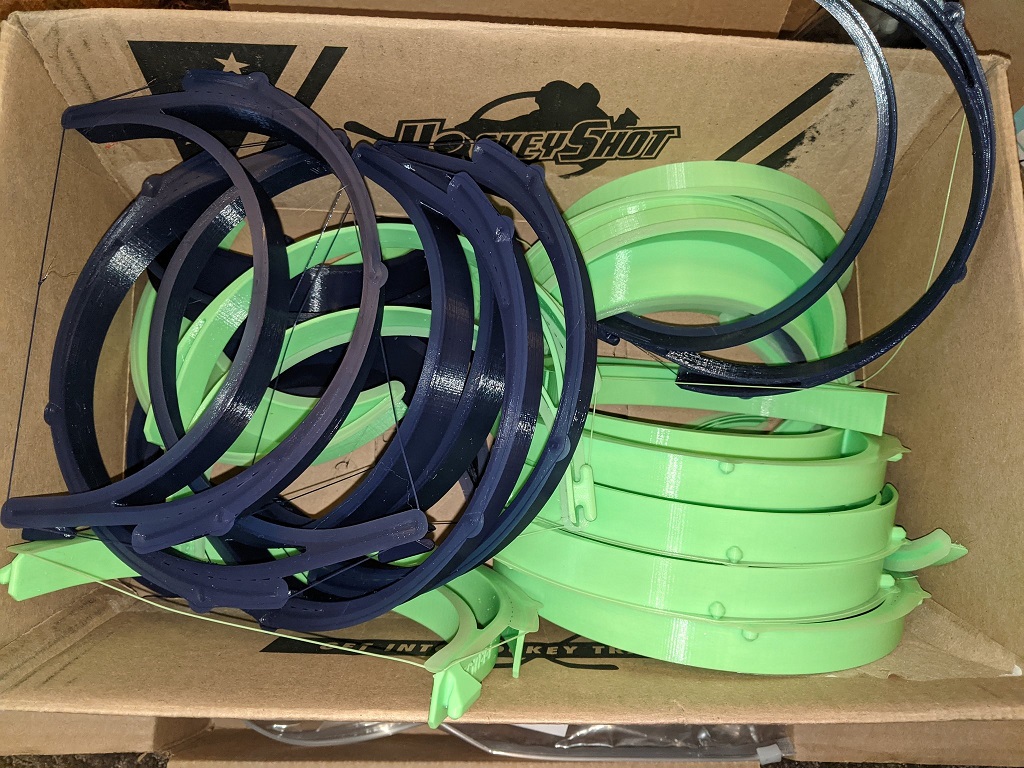
It’s fallen out of the headlines since the spring, but individual makers remain hard at work at their home 3D printers making pandemic protection gear.
Personal protective equipment (PPE) wasn’t a phrase most of us commonly used before this spring. But, like “social distancing”, it’s found its way into our everyday lexicon. Frontline workers have been facing significant shortages of PPE as many hospitals and clinics around the world simply weren’t stocked up to safely face a pandemic.
3D Printing Pandemic Response
Visors for face shields were one of the earliest pandemic-response designs that found their way to 3D printers everywhere. Even with March headlines dominated by the remarkable work some teams were doing 3D printing emergency-use ventilator parts, on an individual level it quickly became apparent that the best way for individuals to help out was with less highly regulated needs.
By the middle of March, the US joined the rest of the world in locking down to flatten the curve. Makers, companies, regulatory bodies, and essentially anyone with access to manufacturing technology quickly came together to pool resources. 3D printing emerged as a fast, accessible way to help in pandemic response, and the community banded together to help.
For those of us in 3D printing news, our inboxes quickly became a tsunami of seemingly-repetitive press releases. We’d receive dozens of announcements weekly, if not daily, of organizations 3D printing face shields for frontline workers. These could be quickly produced and some received national approvals as healthcare-appropriate PPE. In fact, we received so many press releases that by June we had to ask that they be directed where they would have the best impact — with local media and hospitals. There were too many initiatives for us to cover without becoming essentially a dedicated face shield news source.
Which, don’t get me wrong, is awesome — it’s incredible that there were so many initiatives around the world 3D printing PPE.
But the world kept turning and eventually 3D printed PPE became a bit lower profile. This was largely because 3D printing has been used as a stop-gap supply chain solution while traditional manufacturing worked to catch up. 3D printing, as an agile manufacturing technology that doesn’t require tooling, is able to immediately pivot. Many 3D printing operations became effectively factories for PPE and other pandemic-response needs. And then — traditional manufacturing started to catch up.
So more recently we’ve been watching 3D printing companies re-pivot, turning their businesses back to their own focus and away from PPE and pandemic response.
We Still Need 3D Printed PPE
Let’s be very clear, though: this pandemic is still ongoing. In many areas, it’s getting much, much worse. There’s finally some hope on the horizon following recent steps forward in vaccine development, but these won’t be widely available for months yet. Until that time, we need to remain focused on protection and prevention — and the calls to action for 3D printing to help produce PPE remain open.
One maker, Kareese Arneson, recently flagged our attention to her continuing work in 3D printing face shields. She describes her project in a LinkedIn post:
“‘Operation Face Shields’ is a project I concocted to 3d print and donate faceshields to frontline workers. At first I was fully funding the project, buying filament and clear plastic. I also was sacrificing the inner tubes out of my bicycles, racing and all my spare tubes.
Eventually I couldn’t afford to find the project and the entire time I refused payment. I created an Amazon wishlist and spammed it out to everyone I could asking for help to keep the project going. The response was swift, supplies came pouring in along with words of encouragement and thanks from people I didn’t even know.
At the time of writing this I have produced and shipped 75 face shields for Yakama Nation as well as 33 more for other medical care workers, first responders, and other essential workers. I have vowed to continue printing and donating face shields as long as Covid-19 is here and taking the lives; as a promise I made to my stepfather before he died, hep and protect the elders. Thomas Mosqueda was a Yakama Elder, my stepfather, my protector and best friend.”
Yakama Nation, with land near the Cascade Mountain Range, has been hard-hit during the pandemic. So Arneson turned to her 3D printer, a Prusa i3 MK2, and her own stores of filament. She is now 3D printing about 28 face shields on a weekly basis and notes, “I will continue to print until covid is defeated.”
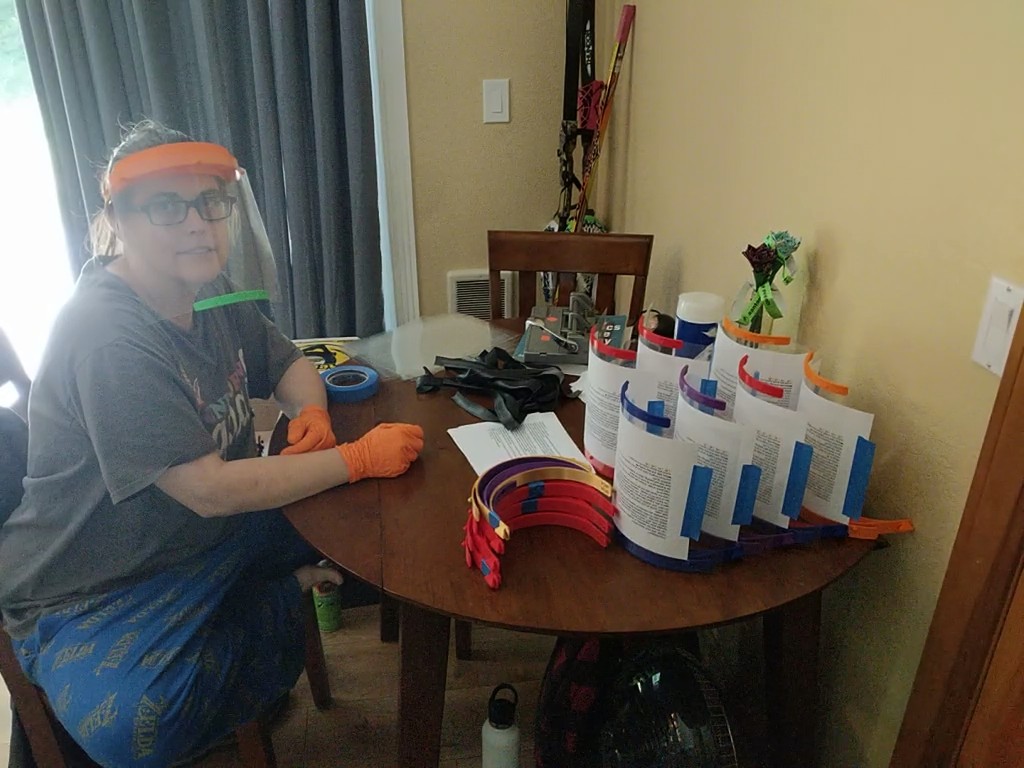
Arneson is among the makers who remain dedicated to individually helping out in the face of COVID-19. While early responses were swift and coordinated, many have been feeling the weight of 8+ months of pandemic life. There is still a need, though, to ensure first responders, medical personnel, volunteers, and those otherwise interacting regularly face-to-face have access to PPE.
Face shields may eventually top lists of “3D printing stories we’re tired of hearing about in 2020” but that’s the pandemic fatigue talking. It’s repetitive because it bears repeating, really, and bears doing over and over. I’m proud to be part of a community where makers can help so directly.
If you’re interested in turning your resources to PPE production, get in touch with your local hospitals and volunteer organizations to see how you can help. Be mindful of the need for validated designs, safe handling, and appropriate packaging and delivery. Ensure that you’re working with the right materials — and responding to actual need with what you want to make.
We reference again the advice laid out from Prusa Research in making such designs:
- “Act as if you were infected by the COVID-19 virus. Wear a face mask and a fresh pair of gloves when collecting each batch of printed parts. Store the parts immediately in a sealable bag.
- Talk with whoever you’re making the shields for, let them know about your manufacturing environment
- There is still debate about how long the virus survives on plastic, but most sources mention 2-3 days. That means that by letting the packed face shields sit for 2-3 days before distributing them, you’ll greatly reduce risk of transmission
- Do not store the entire stock in one place, minimize the risk of cross contamination”