
Mantle explained in some detail why the company chose paste as their 3D print material, and there’s much to be learned.
The company’s co-founder and Chief Science officer, Steve Connor, published a long post detailing the technical reasons why the company uses paste as the material in their metal 3D printers rather than filament, powder or liquids as is used by every other metal 3D printer manufacturer.
If you’re not familiar with Mantle, don’t be surprised. They are a new startup in the 3D print space that’s only recently emerged from stealth mode. That, and the fact there hasn’t been many (or any) trade shows for them to exhibit their products.
Their target market is industrial metal tooling, and their entire system is designed around that market.
We took a look at the company’s metal 3D printing process earlier, as well as Mantle’s market positioning.
In short, Mantle uses a paste extruder to precisely deposit a metal-rich layer. This is heated to remove binder and sinter the metal particles together, followed by a CNC milling action to smooth the surface. This repeats layer by layer until the object is built.
Mantle Paste Decision
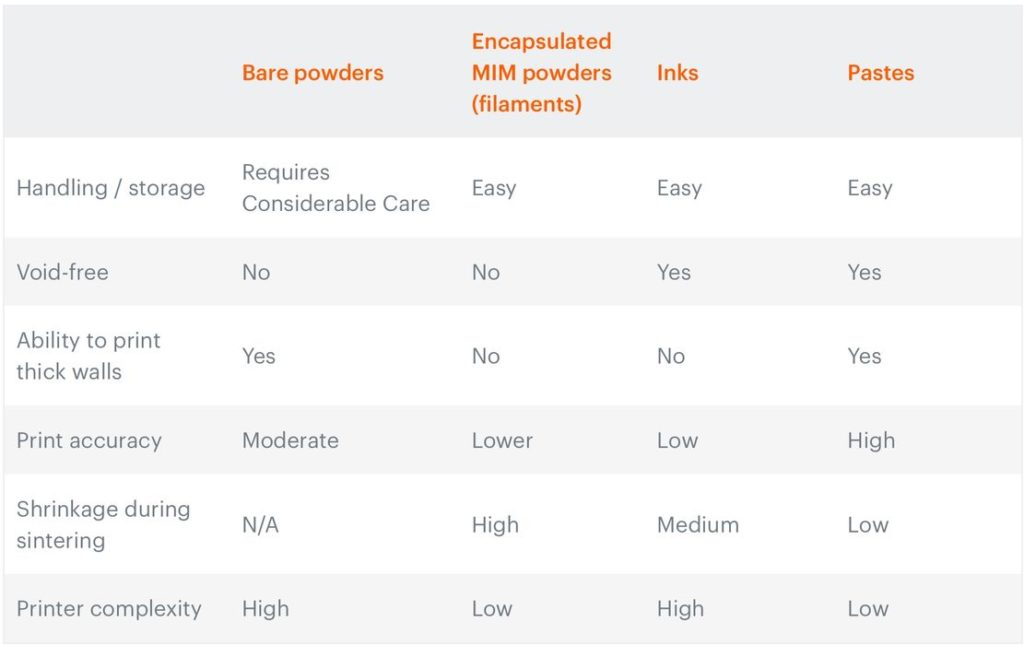
Connor explains that unlike most 3D printer manufacturers, they didn’t start with the technology and then look for a market. Instead they first chose the market. But then there was the question of technology.
Metal 3D printing is now a widespread capability, with multiple vendors offering products. Most options use the PBF process, in which powder is selectively melted by a moving energy source, layer-by-layer. Other approaches involve liquid with metal nanoparticles and high-ratio metal filaments.
While these processes do work and are successfully used by many companies, there are a number of challenges with each. Some processes produce low-resolution parts, others have poor strength, and some involve complex safety regimes to prevent disaster during operations. Most are pretty expensive, too.
Mantle evaluated all of these processes and more, but eventually landed on paste as their material type. That’s unique in metal 3D printing, as far as I know.
Connor explained the many challenges with using “bare metal powders”, which we have explained in this publication frequently. PBF does work, but my goodness, it’s hard to do. And it can be incredibly expensive. Mantle discounted powder almost immediately, because their target market, unlike aerospace, likely could not afford the cost of that process.
They also had problems with liquid approaches, because while liquid flows easily through to a deposition nozzle, it’s hard to control after deposition. This led them to consider a paste approach.
Connor explains the benefits of paste material:
“After testing many different materials, we felt that a flowable metal paste would best meet our core needs for a number of reasons. First, by using a multicomponent paste whose viscosity is tunable at different temperatures, we can print very accurately and fill gaps after extrusion while preventing thick sections from slumping or flowing out of position. This also permits us to achieve high printing density, which means we achieve parts with excellent surface finish and high mechanical properties, Second, pastes simplify handling and storage issues with other feedstocks and provide a long self-life. Third, paste has a low shrinkage rate of 8-10% during sintering, which helps us meet toolmakers’ accuracy requirements. Fourth, paste also allows us to use a much simpler machine design with our printer: we only need one nozzle instead of hundreds or thousands, which reduces cost and simplifies maintenance.”
The low shrinkage rate answers one of my previous questions:
“Other systems typically have parts shrinking up to 20% during de-binding and sintering, and so Mantle must have some interesting software to predict and account for this shifting for a given geometry. If they didn’t, they wouldn’t be able to reliably achieve that accuracy.”
It seems they’ve solved, or at least minimized that issue by significantly decreasing the shrinkage rate.
I’m wondering whether others will consider the use of paste material after hearing its many advantages? The rather expensive PBF systems might become an attractive target for lower cost alternatives using more inexpensive material processes.
Via Mantle