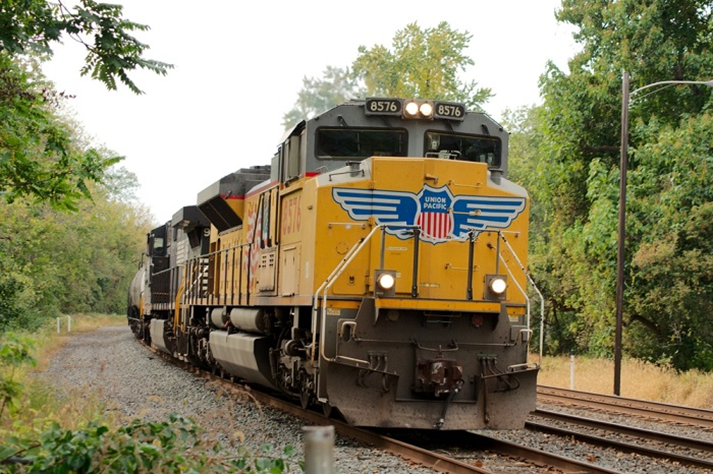
Charles R. Goulding and Preeti Sulibhavi examine how the Union Pacific Railroad has gotten on board with 3D printing.
The Union Pacific (UP) is the second largest railroad in the United States and operates in 23 states. UP is a freight railway essential to western U.S. commerce. Locomotives and rail cars are expensive pieces of equipment that are important to operate on a continuous basis. As part of the quest to maximize efficiency, UP has embraced 3D printing.
UP can benefit from Europe’s railway system and how it has utilized additive manufacturing. For example, the French national railway created a software system to manage the wide variety of 3D printing repair parts needed to service a wide range of rail equipment categories including older components that are no longer manufactured by original equipment manufacturers (OEMs) and/or parts that are difficult to find. In a previous article we authored, “Mobility Goes Additive for RAIL-iability in 3D Printing”, we described the 120 rail industry market participants that are focused on 3D printing for the European rail industry. Kansas City Southern (KCS) has already taken notice of the European rail system’s use of 3D printing.
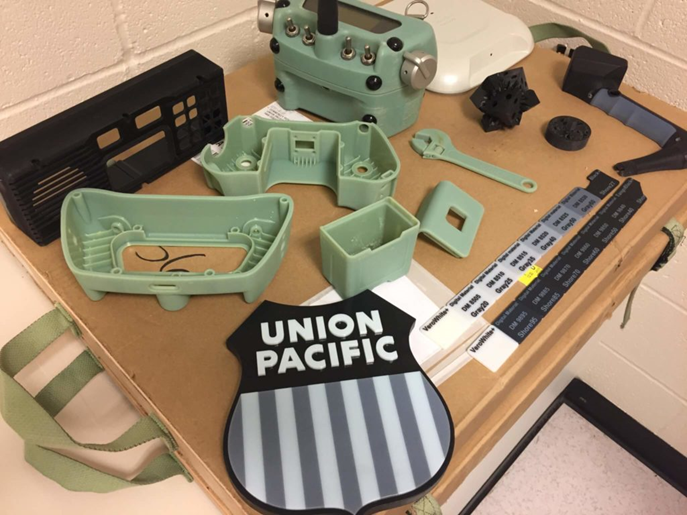
3D Printing and UP
Systems engineers at Union Pacific involved with 3D printing have seen how 3D printing prototypes accelerates the rate of positive change at the company. Utilizing an in-house 3D printer has helped UP make modifications during multiple iterations without waiting for each version to be returned from an external vendor.
And, in standard operations, UP’s 3D printer (pictured below) is playing a key role in “Machine Vision”, an imaging system capable of inspecting 22 components on a passing train. Using a 3D printer, UP designed and developed an air knife that pushes air across a laser (used in the imaging system) for cooling and provides outward airflow to keep debris and particles out.
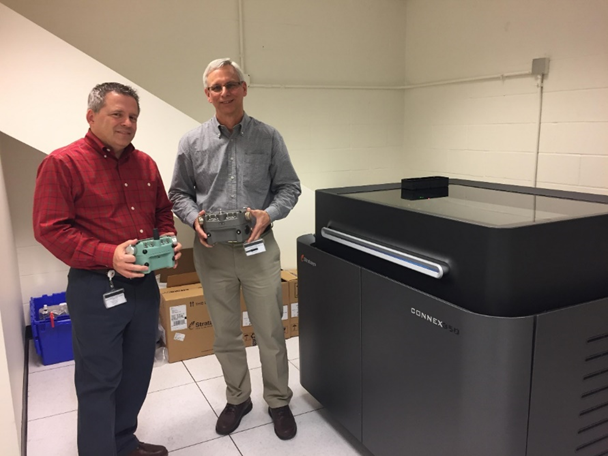
The Research & Development Tax Credit
The now permanent Research and Development (R&D) Tax Credit is available for companies developing new or improved products, processes and/or software. Eligible costs include U.S.-based employee wages, cost of supplies consumed in the R&D process, cost of pre-production testing, contract research expenses, and certain costs associated with developing a patent. As of 2016, eligible startup businesses can use the R&D Tax Credit against $250,000 per year in payroll taxes.
3D printing can help boost a company’s R&D Tax Credits. Wages for technical employees creating, testing and revising 3D printed prototypes can be included as a percentage of eligible time spent for the R&D Tax Credit. Similarly, when used as a method of improving a process, time spent integrating 3D printing hardware and software counts as an eligible activity. Lastly, when used for modeling and preproduction, the costs of filaments consumed during the development process may also be recovered.
Whether it is used for creating and testing prototypes or for final production, 3D printing is a great indicator that R&D Credit eligible activities are taking place. Companies implementing this technology at any point should consider taking advantage of R&D Tax Credits.
Conclusion
The Union Pacific has been in business since 1862 and it enabled the West to greatly develop. 3D printing is now part of the continuing saga of this rail transportation supply chain powerhouse.