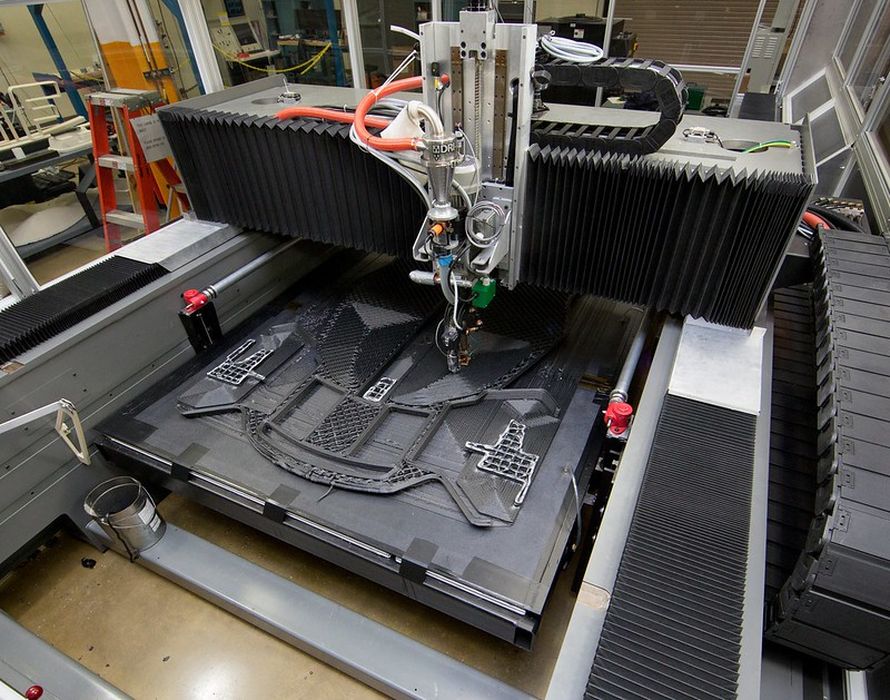
With a roster of engineers from innovation hotbeds such as SpaceX, Tesla and Apple, Freeform Future Corp. is looking to print big and print often.
A new metal 3D printing company has emerged from stealth and is attempting to redefine 3D-printing service bureaus and how manufacturers use production-volume metal additive technology.
Based in Los Angeles, Calif., Freeform Future Corp. boasts a roster of industry leaders from the likes of SpaceX, Velo3D, Carbon, Tesla and Apple, who hoping their new model eliminates historical production barriers and allows manufacturers in any industry to quickly use metal 3D printing to move from idea to volume production.
The model differs from the typical service model in that instead of connecting manufacturers to 3D printing job shops, Freeform is deploying software-defined, autonomous printing factories around the world to bring on-demand production to mainstream industries. That’s right—factories filled with lasers to print many objects at once, at sizes and volumes that are currently not feasible to print
While 3D printing has grown tremendously over the past five years, printing at large-scale production volumes is still uncommon. Several factors are at play, including the technology can be slow, the cost and effort of owning and operating machines is high, and it takes significant expertise to consistently produce high-quality parts quickly.
Freeform’s autonomous printing factories, manufacturing-as-a-service business model and proprietary technology stack promises to bring the scalability of software to physical production by leveraging advanced sensing, real-time controls, and data-driven learning in a scalable factory architecture. As a result, the company says it is able to quickly and cost-effectively produce digitally verified, high-quality parts at mass production scale.
“While at SpaceX, I leveraged metal 3D printing to accelerate the development of numerous rocket engines. We were innovating in ways that were not possible before and accelerating our trajectory toward the future; however, we ultimately realized that it was impossible to print at production scale using even the best current technologies,” said Erik Palitsch, Co-Founder and CEO of Freeform. “We founded Freeform to solve this problem and to make this transformative technology available to all industries, giving anyone the ability to rapidly take an idea and produce it at scale,”
Freeform has partnered with Embark Trucks, a developer of autonomous technology for the trucking industry, to demonstrate Freeform’s metal additive capabilities.
“As Embark brings autonomous trucking technology to market, we need the ability to seamlessly scale up from prototype to production,” said Brandon Connors, head of programs and manufacturing at Embark. “That means sourcing commercial-grade metal parts on short timelines, consistently and at a practical cost. Freeform’s printing service enables us to meet our manufacturing needs, improves supply chain reliability, and gives us the ability to change designs without impacting delivery time, so that we can accelerate the deployment of our technology.”
Read the rest of this story at ENGINEERING.com